Power Recovery Turbines
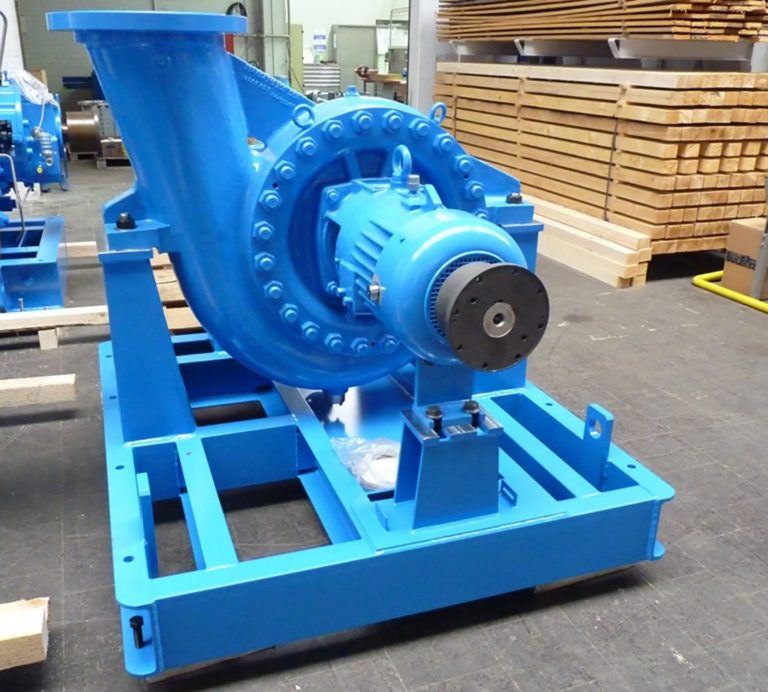
The HPRT delivered 470 kW and CAPEX will be repaid in less than three years (Image source: Sulzer Ltd.)
Manufacturing processes that pressurize fluids often need to reduce these pressures between different stages and this can be achieved using orifice or throttle valves. However, this wastes the potential energy in the liquid or gas. A better solution is to harness this energy and use it to reduce operational costs. Installing a pump, or expander train, which acts as a turbine and is connected to a generator or an existing pump unit, can create additional income and offset some operational expenses.
Reducing operational costs
Any new processing equipment will be designed with HPRTs built-in, so the energy savings are incorporated to the running costs from the outset. For existing infrastructure, pressure reducing valves are a cost-effective way to reduce process pressure, but they make no contribution to operational costs.
More businesses, such as a downstream petrochemical plant in Taiwan, are looking at ways to reduce operating expenditure (OPEX), preferably with a short payback period. Sulzer’s expertise in pump design and manufacturing makes it the ideal partner to develop engineered solutions based on existing pump models.
In this case, as a long-standing customer, the petrochemical plant held regular meetings with Sulzer to discuss upcoming requirements. During one of these events, the customer enquired about HPRTs because they believed they had several potential locations around the plant where energy recovery might be feasible by installing a HPRT into the process.
Sulzer presented various solutions depending on the applications along with general arrangement drawings to show how the HPRTs would fit with the surrounding infrastructure. Discussions with the plant’s technical team focused on some of the details as well as the benefits of HPRTs and how they can be easily integrated into the process with the lowest modification effort.
Minimising the return on investment
Having discussed the technical issues, Sulzer presented the first solution which would deliver 470 kW from a 10 bar pressure drop with an efficiency above 80%. The energy generated by the HPRT would contribute to the local power grid and calculations could be made to estimate the return on investment (ROI), using the electricity cost the plant had negotiated with the utility.
The refinery operator went into the project with an expectation for the capital expenditure (CAPEX) to be repaid in around three years. This would include any changes to the infrastructure to facilitate the installation of the HPRT. In fact, once the calculations were completed using the numbers from the proposed design, the ROI was less than three years, which was an additional bonus for the customer.
The solution was based on Sulzer’s OH2 API 610 design pump, that is used in many applications across the petrochemical and refining industries. It included a single mechanical seal with Plan 11 sealing system and a direct driven generator. Designed with a stainless steel casing and a 450 mm impeller, the HPRT will undergo functional acceptance tests at the manufacturing plant in Germany to confirm the 470 kW output as well as the efficiency rating, all witnessed through Sulzer’s online facilities.
Comprehensive solutions
Although the basic design is based on proven pump technology and materials, there are always wider aspects that need to be properly assessed as part of the complete project. Sulzer’s expertise in delivering HPRTs is essential for a comprehensive solution that will continue to deliver reliable and efficient service.
In this case, the biggest challenge was understanding the customer’s process sufficiently and supporting them with safety systems that protect the HPRT during start-up and shutdown, as well as in the event of a loss of generator main power supply. The turbine (pump) must be able to withstand a certain amount of overspeed conditions before the shut-off valve is closed to slow down the unit by reducing the process pressure.
Sulzer’s knowledge and expertise ensured that all the necessary safeguards were installed as part of the project for a comprehensive solution that will be installed in 4th quarter 2023. Sulzer’s Field Services will accompany the delivery to support installation and commissioning.
Sulzer is involved in different projects with energy recovery solutions, ranging from 50 kW up to 3 MW, for customers with gas expanders or high-pressure process fluids around the world, optimizing their operations both in terms of OPEX and improved sustainability. The key to efficient and reliable operation is ensuring the design is correctly matched to the application, all the necessary safety devices are included and the output promised at the design stage is realised during testing and process operation.
Source: Sulzer Ltd.