Papierhersteller spart mit neuen Kompressoren 100.000 Kilowattstunden im Monat und steigert Verfügbarkeit
Generalüberholen oder neu planen? Als bei Propapier die Sanierung der Druckluftversorgung anstand, entschied man sich für den Kauf neuer Schraubenkompressoren von Atlas Copco. Dank einer detaillierten Bedarfsanalyse, hocheffizienter Maschinen und eines Gesamtkonzeptes, das die unterschiedlichen Druckluftqualitäten berücksichtigt, profitiert der Papierhersteller heute von einer verbesserten Versorgungssicherheit und deutlichen Energieeinsparungen.
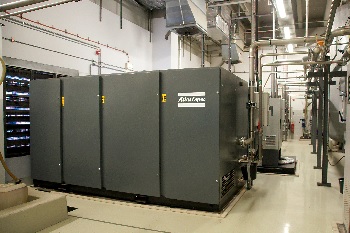
Eine Station mit insgesamt sechs Schraubenkompressoren von Atlas Copco versorgt die beiden Druckluftnetze der Propapier GmbH. (Foto: Atlas Copco)
Um aus Altpapier einen sauber gerollten Bogen Wellpappenrohpapier herzustellen, braucht es in der Fabrik der Propapier PM1 GmbH in Burg bei Magdeburg eine Strecke von 170 Metern. „Wir verarbeiten hier zu 100 Prozent Altpapier“, erklärt Michael Hanke, Leiter Technische Dienste bei Propapier. „Das wird unter Zugabe von Wasser in einer großen Trommel zerkleinert und aufgelöst. Auf diese Weise trennen wir die für unseren Prozess wertvollen Papierfasern von den unbrauchbaren Reststoffen.“ Anschließend werden die Fasern gereinigt und sortiert und in entsprechender Verdünnung auf die 5,8 m breite Papiermaschine gebracht. Bei den folgenden Prozessen geht es dann vor allem darum, geschickt das Wasser zu eliminieren, so dass am Ende Papier übrig bleibt. Dazu durchläuft der Papierbrei die Sieb-, die Pressen- und die Trocken-Partie. Es folgt eine Veredelungsstelle, in der Leim auf das Papier aufgebracht wird, um die technischen Eigenschaften zu verbessern und die Bedruckbarkeit des Papiers herzustellen. Zuletzt wird das Papier aufgewickelt, auf die gewünschte Breite zugeschnitten und an die Kunden versandt.
„An unseren Standorten in Burg und in Eisenhüttenstadt stellen wir pro Jahr über eine Million Tonnen Wellpappenrohpapiere her“, beziffert Hanke den Output der beiden Papierfabriken. „Wir beliefern damit die insgesamt acht europäischen Wellpappenwerke der Progroup AG, zu der auch Propapier gehört.“
Ohne Druckluft steht die Produktion
Bereits seit der Unternehmensgründung im Jahr 2000 wird die Druckluftanlage in Burg von der Magdeburger Dr. Weigel Anlagenbau GmbH betreut. Der Atlas-Copco-Vertragshändler hat ehemals die Druckluftversorgung aufgebaut und in den Folgejahren Service, Wartung und Modernisierung der Anlage übernommen. „Eine verantwortungsvolle Aufgabe“, betont Hanke, „denn wenn die Druckluft steht, steht auch unsere Papiermaschine und damit das ganze Werk. Wir haben hier sehr hohe Stundenausfallkosten, deshalb muss der Service immer direkt verfügbar sein.“ Mit Dr. Weigel habe man einen Wartungsvertrag samt Komplettservice abgeschlossen, und das laufe – auch aufgrund der räumlichen Nähe – bislang ausgezeichnet.
Um die Produktion am Laufen zu halten, benötigt Propapier Druckluft in zwei verschiedenen Qualitäten: Instrumenten- und Arbeitsluft. Die Instrumenten-Druckluft betreibt alle Regelarmaturen und bewegten Teile, wie Ventilinseln und Zylinder. Diese Luft wird mittels Adsorptionstrockner und Filtern so aufbereitet, dass sie die Anforderungen des Papiermaschinenherstellers sicher erfüllt. Ein zweites Druckluftnetz liefert die Arbeitsluft, die unter anderem zu Kühlzwecken sowie zum Aufführen oder Abschlagen der Papierbahnen benutzt wird. An diese Druckluft werden keine besonderen Anforderungen gestellt.
Unterschiedliche Anforderungen an die Qualität waren wichtig für die Planung
Als vor zwei Jahren die Sanierung der kompletten Druckluftversorgung anstand, waren die unterschiedlichen Qualitätsanforderungen an die erzeugte Druckluft ein entscheidender Planungsfaktor. „Nach 15 Jahren Dauerbetrieb hatten wir von der Dr. Weigel Anlagenbau GmbH die dringende Empfehlung bekommen, unsere Druckluftanlage entweder generalüberholen zu lassen oder die Station komplett auszutauschen“, erklärt Hanke. „Die Generalreparatur wäre uns in Summe kurzfristig kostengünstiger gekommen, aber wir hätten damit den technischen Stand von vor zehn bis 15 Jahren manifestiert und die Probleme, die wir mit unserer Anlage hatten, nicht lösen können.“ Die Schwierigkeiten resultierten vor allem daraus, dass bis dato die Instrumenten- und Arbeitsluft aus einem gemeinsamen Netz gezogen wurden. „Die Druckschwankungen aus der Arbeitsluft schlugen auf die Instrumentenluft durch und hatten des Öfteren einen Druckabfall zur Folge, was wiederum die Prozesse störte“, erinnert sich Hanke. Weitere Störungen ergaben sich aus der Luftkühlung der Kompressoren. Die erforderliche Luftumwälzung konnte nicht gewährleistet werden, so dass in den Sommermonaten häufig Ausfälle durch Übertemperatur entstanden. „Außerdem war der Adsorptionstrockner zu klein. Dadurch hatten wir einen höheren Druckverlust und mussten mehr Energie aufwenden, um den benötigten Volumenstrom zu erzeugen.“
Zwei Druckluftnetze verbessern Versorgungssicherheit
Propapier entschied sich deshalb für den Austausch der Kompressoren und ein neues Versorgungskonzept auf Basis zweier Druckluftnetze, die im Normalfall voneinander getrennt arbeiten, sich jedoch im Störungsfall ergänzen können. Ziel war es, die Versorgung noch sicherer zu machen, Leerlaufzeiten so gering wie möglich zu halten und mit einer effizienteren Fahrweise und Technik Energie zu sparen. Ein wesentlicher Punkt war auch die Umstellung der Anlage auf Wasserkühlung.
Heute versorgt eine gemeinsame Station, in der insgesamt sechs Schraubenkompressoren der Essener Atlas Copco Kompressoren und Drucklufttechnik GmbH arbeiten, die beiden Druckluftnetze. Ein drehzahlgeregelter GA 90 VSD und ein GA 160 mit fester Drehzahl und installierten Motorleistungen von 90 bzw. 160 Kilowatt (kW) liefern die Instrumenten-Druckluft. Diese durchläuft einen Adsorptionstrockner und einen Partikelfilter, bevor sie in der geforderten Qualität ins Netz gespeist wird.
Die Arbeitsluft wird von einem GA 160 FF und einem GA 90 FF mit fester Drehzahl, einem drehzahlgeregelten GA 160 VSD FF sowie einem drehzahlgeregelten GA 90 VSD FF erzeugt. Das Kürzel FF steht für die „Full-Feature“-Variante, bei der bereits ab Werk Kältetrockner, Kondensatableiter sowie alle Anschlüsse für eine Wärmerückgewinnung in das Kompressorgehäuse integriert sind. Beim GA 90 VSD FF handelt es sich um einen luftgekühlten Kompressor, der bereits vor drei Jahren im Zuge einer Systemoptimierung angeschafft und nun ins neue Konzept integriert wurde. Die anderen fünf Maschinen arbeiten wassergekühlt. Sie sind an das Kühlsystem der Papierproduktion angeschlossen. In Kürze wird über zusätzliche Wärmetauscher die Kompressorenabwärme zurückgewonnen und damit das Prozesswasser für die Papierherstellung erwärmt.
Ein ES-360-Energiesparsystem von Atlas Copco lässt alle Kompressoren an ihren jeweils optimalen Betriebspunkten laufen. Das ES 360 hat den Vorteil, dass es mehrere drehzahlgeregelte Kompressoren effizient steuern kann. Andere Steuerungen können den Kompressoren demgegenüber nur ‚Start‘ und ‚Stopp‘ vorgeben, aber keine Drehzahl. Außerdem können bis zu drei Netze unabhängig voneinander gesteuert werden. Somit ist eine optimale Energieeffizienz bei größtmöglicher Versorgungssicherheit garantiert.
Bei Propapier hat immer die Instrumentendruckluft Vorrang. Gibt es eine Störung, wird automatisch einer der Arbeitsluft-Kompressoren zugeschaltet. Um die nötige Druckluftqualität einzuhalten, liegt die Schnittstelle beider Netze vor dem Adsorptionstrockner. „Durch die Trennung der Netze haben wir die Druckbänder stabilisiert. Die Instrumenten-Druckluft wackelt eigentlich gar nicht mehr“, erklärt Hanke. „Die Schwankungen liegen heute bei maximal plus/minus 0,2 bar bei einem Betriebsdruck von 6 bar.“
Detaillierte Bedarfsanalyse liefert Basis für neues Anlagenkonzept
Das Konzept für die aktuelle Druckluftstation erarbeitete Hankes Abteilung im Vorfeld der Ausschreibung gemeinsam mit den Ingenieuren von Dr. Weigel. Dafür wurde zunächst über einen längeren Zeitraum der Volumenstrom an den einzelnen Abnehmern von Instrumenten- und Arbeitsluft gemessen. „Auf dieser Basis haben wir Betriebszustände wie beispielsweise Normalbetrieb, ‚Shut-down‘, wenn die Maschine in Reparatur ist, oder An- und Abfahrbetrieb festgelegt“, erläutert Hanke die Vorgehensweise. „Für jede dieser Positionen haben wir den genauen Bedarf ermittelt und danach die Kompressoren in Summe und auch im Detail ausgewählt. Wir haben ja zum einen eine Grundlast und müssen darüber hinaus jeden Betriebszustand sicher abdecken, ohne dass wir aus dem Regelbetrieb herauskommen.“ Parallel sei es gelungen, auf der Produktionsseite Bedarfsspitzen zu glätten und so die erforderliche Kompressorenleistung zu reduzieren.
Die Kompressoren werden automatisch entsprechend der abgenommenen Druckluft kombiniert. „Den Zustand ‚Stillstand‘ können wir bei der Arbeitsluft allein mit der großen VSD-Maschine abdecken“, beschreibt Hanke. „Im Normalbetrieb brauchen wir zusätzlich eine GA 90 als Konstantläuferin, und wenn wir beim Aufführen der Papierbahnen unseren maximalen Bedarf haben, dann gehen alle Maschinen ans Netz.“ Bei der Instrumenten-Druckluft arbeite die GA 160 als Konstantläuferin und die GA 90 VSD als Regelmaschine. „Wir haben auch ein paar Druckluftspeicher“, ergänzt Hanke, „aber die helfen uns aufgrund der hohen Bedarfe nur im Sekundenbereich.“
Enges Zeitfenster für den Umbau
Eine Herausforderung war auch die Auslegung des Kühlsystems. Das Kühlsystem der Fabrik konnte die Wärmemenge der Kompressoren nicht aufnehmen. Die notwendigen Erweiterungen inklusive Redundanz bei Ausfall von Systemelementen wurden vom Betriebsingenieur der Papierfabrik, Volker Krug, berechnet und gemeinsam mit den Ingenieuren von Dr. Weigel definiert.
Nachdem das Grundkonzept für die Druckluftanlage stand, ging es im nächsten Schritt darum, die passende Kompressortechnik zu finden. „Wir haben den Markt sondiert und gesehen, dass es sehr ähnliche Angebote gibt“, fasst Hanke zusammen. „Dr. Weigel lag in Kombination mit Atlas Copco in der Spitzengruppe. Die angebotene Lösung war am effizientesten, die Technik war uns bekannt, ebenso der Servicepartner.“ Es habe alles zusammenpasst. „Deshalb hat Dr. Weigel den Zuschlag für die Lieferung der kompletten Technik und für die Montage der Anlage bekommen.“
Der Umbau sollte möglichst ohne Maschinenstillstände realisiert werden. Dies gelang, indem man ein Zeitintervall wählte, in dem die Papierproduktion aufgrund verschiedener Wartungsarbeiten ruhte. In diesen drei Tagen arbeitete das Dr.-Weigel-Team mit 25 Mitarbeitern rund um die Uhr, um die alte Druckluftstation zu demontieren und die neue zu installieren und in Betrieb zu nehmen. Zwei Kompressoren – der luftgekühlte GA 90 VSD FF und eine der alten Maschinen – liefen währenddessen weiter und deckten den Bedarf für Reinigungs- und Nebenprozesse. Eine komplette Totzeit gab es nur über 24 Stunden.
Neue Anlage spart 100.000 kWh pro Monat
Schon vor der Installation der neuen Anlage wurde eine Online-Messung installiert, so dass der Druckluftverbrauch kontinuierlich gemessen und im Betriebsleitsystem dokumentiert werden kann. „In unserer Leitwarte ist der Druckluftverbrauch an jeder Maschine sichtbar“, sagt Hanke. „Dort gehen auch die Störmeldungen hin und können direkt von uns bearbeitet werden.“ Auch die monatlichen Stromverbräuche für die einzelnen Kompressoren sowie die Summe der Leerlaufstunden lassen sich über das Leitsystem generieren und stehen dann unter anderem für das Energiemanagementsystem nach ISO 50001 zur Verfügung.
Dass die neue Station effizienter arbeitet als die alte, wurde bereits in den ersten Monaten ihres Betriebs deutlich. Der Grund liegt nach Ansicht aller Beteiligten vor allem in der kontinuierlich optimierten Technik der Atlas-Copco-Kompressoren – denn die sind heute weitaus effizienter als 15 Jahre alte Maschinen. Einen weiteren Beitrag leistet die Umstellung der Luftkühlung auf Wasserkühlung. Insbesondere in den Sommermonaten können nun die Kompressoren im optimalen Betriebszustand gefahren werden. „Mit unserer neuen Station ist der Stromverbrauch bei gleicher Lastlaufzeit pro Monat um rund 100.000 Kilowattstunden gesunken“, beziffert Michael Hanke die Energieeinsparungen. „Das entspricht mehr als 20 Prozent unseres ursprünglichen Verbrauchs. Mit fünf Prozent Einsparungen hatten wir bei der Planung gerechnet, und das bekommen wir übers Jahr gesehen locker hin.“
Quelle: Atlas Copco Holding GmbH