Optimizing asset performance – Sulzer offers long-term maintenance support for Colombian industries
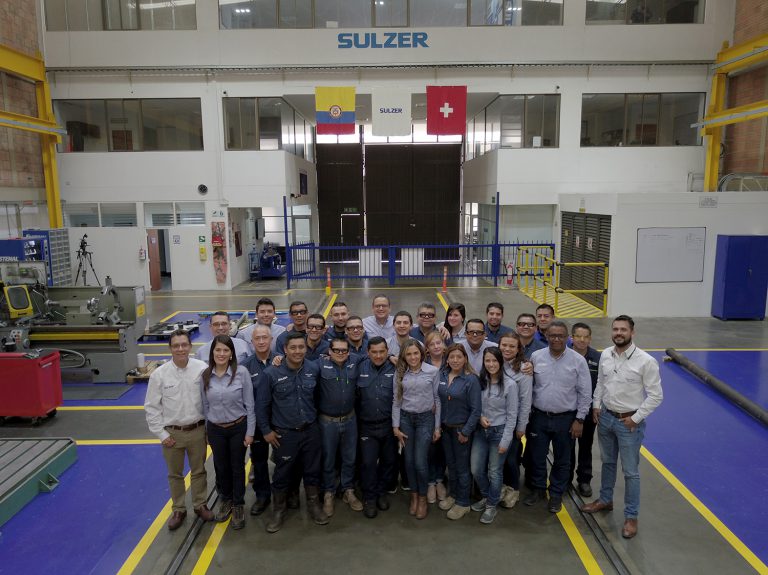
The team at Sulzer’s Colombian service center has extensive in-house expertise to support customers in power generation, oil & gas, mining and water as well as general industry. (Image source: Sulzer Ltd)
Today, specialist teams offer a wide range of services for rotating equipment to support customers in power generation, oil & gas, mining and water as well as general industry. In Colombia, the Bogota Service Center provides a comprehensive range of services that includes long-term parts and service contracts, which simplify maintenance projects and reduce lead times for components.
Many industrial operations use rotating equipment for a range of applications. Having in-depth knowledge about pumps, compressors and steam turbines, no matter who built them, is very valuable. Sulzer’s Colombian service center has extensive in-house expertise and can also call on a worldwide network of engineering facilities. This enables repairs and upgrades to be completed efficiently and cost-effectively.
Expert maintenance support
Major industries in Colombia can minimize downtime and improve reliability by taking advantage of Sulzer’s expert maintenance support. Extensive industry knowledge and expertise in rotating equipment ensures that customers receive a fast response for spare parts and servicing.
As a pump original equipment manufacturer (OEM) and independent maintenance provider for all rotating equipment, Sulzer has decades of experience in maximizing reliability and optimizing costs. In-house designers, manufacturing facilities and testing capabilities ensure a comprehensive service.
David Lora, General Manager of Sulzer Colombia, adds “We offer customers the opportunity to take advantage of Sulzer’s expertise in repair technology and to benefit from this knowledge. We are able to organize long-term parts and service contracts for assets, which ensure that maintenance is completed on time and continued reliability is assured.”
In-house specialists
To determine the most opportune time for repairs to be completed, Sulzer can design and install vibration monitoring equipment and analysis tools to implement a preventative maintenance schedule. Using pre-planned outages for repairs is the most cost-effective way to deliver improved reliability.
For pump equipment, Sulzer can also design, build and install the electrical control equipment, including drives and accessories. Matching equipment to the application is just the first step, it is important for the controls to be properly integrated with the wider infrastructure.
In addition to these services, Sulzer also provides experienced field service engineers for on-site support of existing machinery as well as the installation and commissioning of new equipment. These skilled engineers receive regular training, for example API 686, 4th edition, to ensure they are up to date with the latest guidelines on the on the recommended practices for machinery installation and design in the petroleum sector.
Customer training
To help customers with their in-house maintenance, experts from Bogota can deliver training courses on operational best practice and routine maintenance for a wide range of equipment. This helps to extend reliability and the efficiency of important assets, which in turn, optimizes productivity for the customer.
David Lora concludes: “We appreciate the challenges of working in heavy industry and the importance of asset reliability. Our goal is to deliver the most effective and efficient maintenance service for our customers and help them to achieve their objectives.
Source: Sulzer Ltd.