New Pump Energy Optimization Solution Launched to Drive Cost and Carbon Savings
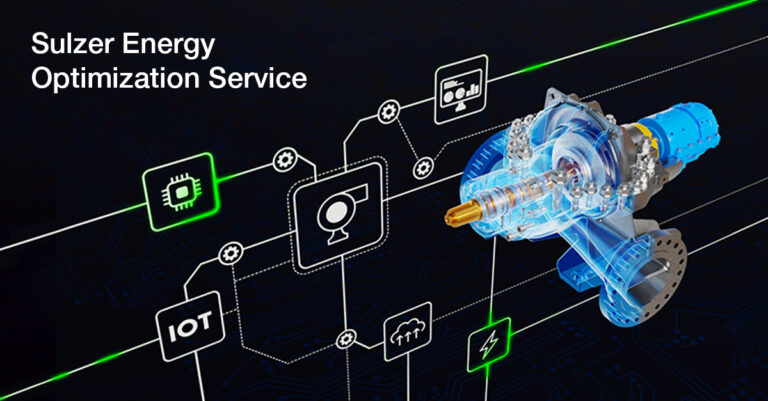
Image source: Sulzer Ltd.
Launched to address growing demand for industrial energy efficiency, the solution brings together digital analysis, machine learning and ongoing monitoring with Sulzer’s decades of engineering expertise to drive down carbon emissions, enhance reliability, and reduce energy costs. A 1% increase in global pump efficiency would save around 59TWh of electricity – equivalent to New Zealand’s annual power needs; some pumps’ efficiency could be increased by as much as 20-30%.
Announcing the solution, Ravin Pillay-Ramsamy, Services Division President at Sulzer said:
“Inefficient and unreliable pumps cost operators in the industrial sectors millions of dollars in unnecessary downtime, energy costs and carbon emissions every year. Sulzer Energy Optimization Service offers a comprehensive solution that tackles this inefficiency – from identification through to improvement and monitoring.
“A pilot customer in Spain will now save €1 million in energy costs and over 2,300 tonnes of carbon dioxide a year as a result of energy optimization improvements identified by the Service. By rerating five pumps, energy efficiency increased from 72% to 83% saving the operator 5,000MWh in electricity every year.”
Consisting of four steps, an initial pump energy audit identifies areas of inefficiency with Sulzer’s proprietary calculator – PumpWise – outlining the potential energy, carbon and monetary savings.
A tailored proposal is generated by Sulzer’s expert team presenting a range of options to return the pump to run at its best efficiency point through an engineered retrofit, with varying techniques such as hydraulic re-rates, specialized coatings, wear clearances and more. Each option weighs operational costs, investment, downtime, payback and efficiency guarantees. The upgrades are then implemented with support from Sulzer’s established retrofit team which has delivered more than 4,000 retrofit projects globally since its setup in 2010. The team is supported by a network of more than 120 service locations globally.
Post retrofit, Sulzer offers a performance agreement to maintain optimized reliability and efficiency. This includes access to Blue Box, Sulzer’s proprietary machine learning technology which turns pump performance data into actionable insights.
Ravin adds: “For operators who are constantly challenged to do more with less, making energy efficiency improvements is a win-win. With pumps accounting for 20% of the world’s electricity demand, we want to offer a streamlined, futureproofed way for customers to improve their energy efficiency regardless of their pump OEM.
“To do so, we’ve combined the competence of our people and longstanding engineering expertise with our proprietary innovations and wrapped them in a collaborative and customer-centric approach. Altogether we believe this solution creates a new best practice standard for pump operation that goes above and beyond in supporting operators to remain future-ready.”
Source: Sulzer Ltd.