New High-Performance Seals for Butterfly Valves
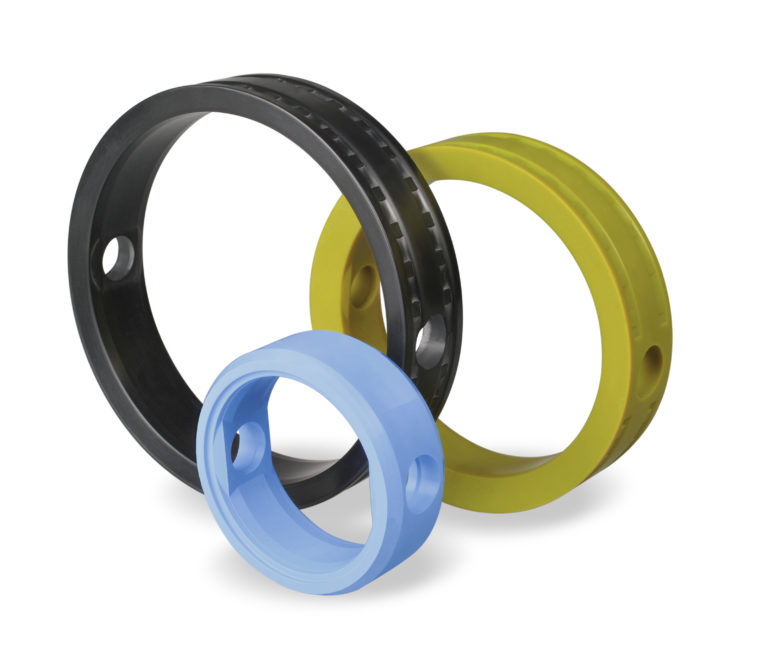
Freudenberg Sealing Technologies and customer develop new high-performance seals for butterfly valves (Image source: Freudenberg Sealing Technologies)
Definox produces valves and stainless steel equipment for the process industry and specializes in producing components for processes in the food, beverage, pharmaceutical, cosmetics and animal feed sectors.
Definox needed a customer-specific sealing solution for the development of a new series of high-performance butterfly valves. Based on their previous positive experiences, the developers proposed this task to the sealing experts at Freudenberg Sealing Technologies in order to benefit from their expertise in development and materials. The resulting 70 EPDM 291 O-rings have already been delivered, and Definox is using them successfully.
The goal was to find the ideal combination of uncompromising tightness, simple installation, dead space-free sealing geometry and wear-resistant materials. With this premise in mind, the Freudenberg development team set to work. In an initial phase, it performed extensive validation tests of the new valve seal on the in-house test stand. The experts tested seals in three reference dimensions under real conditions in original Definox valves. The results of the long-term tests could then be transferred to other seal dimensions. This method provides reliable information about the seal properties while also saving time and money in the development process.
Validated on the Freudenberg test stand
The test stand is designed as a CIP system with multiple containers that makes it possible to simulate various cleaning processes with acids, lye and disinfectants. Up to three valves can be tested simultaneously or successively on test tracks. Operating parameters such as temperature, pressure and flow rate are recorded digitally. The inspections provide tested findings on the material’s resistance and functional reliability – and thus important information for choosing the appropriate seal.
This cooperative project has resulted in an innovative butterfly valve seal whose combination of wear-resistant materials and innovative design is a perfect fit for the demands of the process industry. Butterfly valve seals should close with little force and, when closed, have high compression to ensure the sealing function. The sealing geometry also has to be developed free of dead space and leak-free to meet the demands for hygienic design. The new sealing solution from Freudenberg Sealing Technologies excels with very good pressure resistance and extremely low torque. The pressure resistance is maintained multiple switching operations. These properties guarantee a long service life and high reliability even under challenging operating conditions.
Materials with high media and temperature resistance
“We convinced our customer with our new, high-performance butterfly valve seal, which is tailored to meet specific requirements, so that they asked us to start replacing the seals of existing valve types,” said David Brenière, Sales Manager, Process Industry at Freudenberg Sealing Technologies. The result is a series of butterfly valves with different dimensions, which is available in the three FDA- and EU (VO) 1935/2004-compliant materials 75 EPDM 253356, 75 Fluoroprene XP 41 and 75 HNBR 254067. 75 Fluoroprene XP 41 is additionally tested in vivo according to USP chapter 88 at 121°C and certified to Class VI, and meets the 3-A sanitary standards and regulations of the BNIC (Bureau National Interprofessionnel du Cognac).
Thanks to the partnership-based cooperation with the customer, the new high-performance butterfly valve seal now provides the process industry with a sealing solution for butterfly valves that is optimally designed to meet its demands.
Source: Freudenberg FST GmbH