New Edition of White Paper Concludes Peristaltic Pump Technology can Deliver 70 percent+ Water Savings for Mining Industry
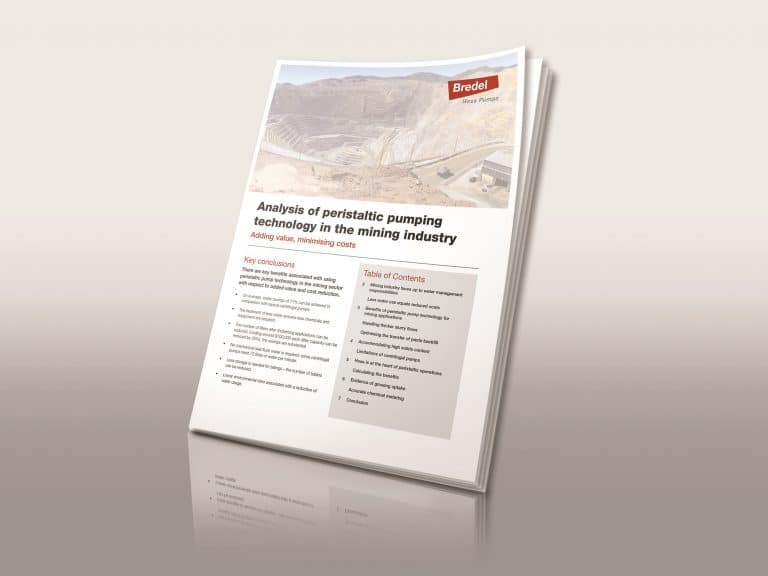
White paper. (Image source: Watson-Marlow)
The publication of the 2019 edition of the white paper coincides with an update to the mining section of the company’s website – which provides a wealth of information on a range of transfer and metering applications.
First published in 2011, the latest version of the white paper presents data and real-life case study examples of mines that have deployed WMFTG’s peristaltic hose pump technology and have seen significant reductions in water use as a result.
For the mining sector, the paper’s findings continue to be welcome news. Water use (and re-use) is critical element of the sector’s global commitment to minimising its environmental impacts and footprint. All over the world, mines are now required to assess the impact of their operations on local and regional water quantity and quality, in order to retain a social license to operate. With this in mind, best practice water management defines credibility for the mining industry while negating the potential impact of additional costs.
However, the relationship between maintaining a reliable supply of water to support mineral processing, and using as little water as possible in order to have the smallest volume on hand at any time, to both treat process wastewater or provide pump service water time, means that water inventories must be managed carefully.
Pumps have a vital role to play; and peristaltic pumps specifically can be considered water-saving devices, not simply because they accommodate very high solids-content materials found commonly in mining operations, but because they do not have seals they don’t require water for flushing, thus eliminating the requirements to both treat process wastewater or provide pump service water.
The paper goes on to conclude that there are key benefits associated with using peristaltic pump technology in the mining sector with respect to added value and cost reduction.
The most significant of these findings is that on average, water savings of 71 percent can be achieved in comparison with typical centrifugal pumps.
Paste backfill and accommodating solids
One of the most commonly pumped materials in mining operations is paste backfill, and the goal for the high density paste formulations is to produce a ‘pumpable’ material that does not segregate when placed – the fines content should be a minimum of 15% by weight of the paste. Naturally, choosing the right pump technology for the task is vital.
The white paper offers real-life examples of mines where the wear-free performance of peristaltic pumps has arguably been the most attractive benefit. Obviously, the longer a pump can operate without maintenance or failure, the better.
The wear-free performance of peristaltic pumps is an attribute that results from a unique operating principle. Unlike other pumps, the abrasive nature of the product has no bearing on pump life and the need for routine maintenance and spare parts is reduced greatly.
Accurate chemical metering
Also covered by the white paper is the potential for savings that can be achieved through accurate chemical metering. Peristaltic pumps will maintain the floatation rates of ore extracts to ensure economical use of expensive chemicals and create significant process efficiencies.
The upshot is that peristaltic pumps have become first choice in mines throughout the world for applications that include dosing process reagents and pumping shear-sensitive polymers for flocculation and coagulation, abrasive lime slurries for pH control, or corrosive chemicals like cyanide for gold recovery.