Innovative Rohrverbindungen erleichtern den Bau einer Prüfanlage für Kompressordichtungen
Phastite, der innovative neue Rohrverbinder von Parker Instrumentation, vereinfachte den Bau einer modernen Einrichtung für das Testen der Dichtungen von Trockengaskompressoren in der neuen Turbomaschinen-Betriebsstätte von John Crane in Slough, Großbritannien.
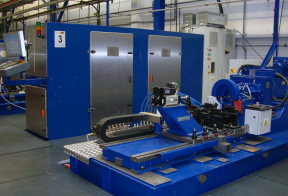
Phastite-Fittinge wurden für Hochdruckverbindungen mit permanentem Durchfluss in jeder der fünf neuen Anlagen in der neuen, mehrere Millionen Pfund teuren Testanlage von John Crane eingesetzt (Foto: Parker Instrumentation).
Die Kombination aus Hochdruckmontage und „Push-Fit“-Installation der neuen Fittinge ermöglichte es dem Unternehmen, erhebliche Zeiteinsparungen im Vergleich zu den herkömmlich verwendeten Montageverfahren mit ’Konus/Gewinde’- und geschweißten Verbindungen zu realisieren.
John Crane ist der weltweit größte Hersteller mechanischer Dichtungssysteme und hat über 3 Millionen Euro in seine neue Gasdichtungs-Prüfanlage investiert. Dazu gehört die Installation von fünf neuen Hochdruck-Testständen, die eine Vielzahl von Betriebsbedingungen der Verdichter reproduzieren. Die aufgerüsteten Testanlagen bieten im Vergleich zu vorher die Möglichkeit, mit höheren Drücken bis zu 800 bar zu testen. Die Anlagen können außerdem Dichtungen mit Wellendurchmessern bis 500 mm oder mit Drehzahlen bis 42.000 U/min testen.
Phastite-Fittinge wurden für Hochdruckverbindungen in zwei Bereichen eingesetzt: für Verbindungen mit permanentem Durchfluss in den fünf Prüfständen selbst sowie an den Gasversorgungsrohren mit großem Innendurchmesser, die Druckluft und Heliumgas zu den Testzellen führen.
Bei der früheren Prüfständen für Kompressordichtungen setzte John Crane üblicherweise ’Konus/Gewinde’-Fittinge für die Hochdruckleitungen ein, die erheblichen Zeitaufwand für die Montagevorbereitung und die Montage benötigten. Die vor kurzem erfolgte Markteinführung von Phastite von Parker bot den Anlagenherstellern eine neue zeit- und geldsparende Option, da diese Hochdruckverbindungen mithilfe eines ’Push-Fit’-Arbeitsgangs innerhalb von Sekunden montiert werden können.
Die fünf Testanlagen erzeugen den Gasdruck, der tatsächlich in den Verdichtergehäusen vorhanden sein wird, und messen mit ultragenauen Instrumenten jegliche Leckagen in den Dichtungen. Jede der fünf Anlagen benötigt ungefähr 20-25 permanente Hochdruckverbindungen, wobei Phastite im Vergleich zur Installation mit ’Konus/Gewinde’-Fittingen dem Anlagenhersteller die maschinelle Vorbereitung der Rohrenden und das nachfolgende Gewindeschneiden ersparte. Phastite-Fittinge werden einfach auf die Rohrenden geschoben und innerhalb von Sekunden mithilfe eines Handwerkzeugs montiert.
Ein Sprecher des Anlagenherstellers bemerkte: „Phastite bot uns einen viel schnelleren und effizienteren Montageprozess. Für Anwendungen mit hohem Druck und hoher Strömungsgeschwindigkeit bietet die neue Verbindungstechnologie von Parker eine interessante Alternative, wenn permanente Rohrverbindungen erforderlich sind. Die Fittinge sind außerdem wegen ihrer ’eingebauten’ Widerstandsfähigkeit gegenüber Vibration für diese Anwendung sehr attraktiv.“
Phastite-Fittinge wurden auch bei zwei Versorgungs-Rohrleitungen mit großem Durchmesser für Druckluft und Helium eingesetzt. Diese langen Rohrleitungen führen oberhalb der Anlage die Gase rund um den Testbereich. Phastite T-Stücke werden verwendet, um die Gase zu jeder Testzelle abzuzweigen. Bei dieser Anwendung sind Phastite-Fittinge eine Alternative zu Schweißverbindungen und sparen damit die Kosten und den Zeitaufwand für das Orbitalschweißen. Ungefähr 30 Verbindungsstellen waren insgesamt erforderlich, um die Versorgungsleitungen zu realisieren, von denen jede mithilfe des Handwerkzeugs innerhalb von weniger als 2 Minuten montiert wurde. Die komplette Installation für die Gasversorgung, einschließlich des Schneidens und Montierens der Rohrleitungen, benötigte insgesamt nur einen Tag. Die Einfachheit dieser Vorgehensweise ermöglichte es John Crane, die Installationskosten auf einen Bruchteil der Kosten eines geschweißten Systems zu verringern.
Die Investition von John Crane führte dazu, dass die Prüfanlage jetzt doppelt so viele Dichtungen testen kann wie bisher und außerdem Hochdrucktests möglich sind. Daneben verfügen die neuen Anlagen über ein hochentwickeltes Datenerfassungssystem, mit dessen Hilfe Kunden von Ihren Standorten aus das Testen ihrer eigenen Dichtungen online überwachen können. Dies beschleunigt die Auslieferung und spart Kunden, die normalerweise jemanden für die Beobachtung der Tests abordnen würden, Zeit und Geld. Da John Crane Kompressordichtungen weltweit liefert, können diese Einsparungen erheblich sein.
Über Parker
Parker Instrumentation ist Teil der Parker Hannifin-Gruppe. Mit einem Jahresumsatz von über $ 12 Mrd. ist Parker Hannifin der weltweit größte Hersteller von Geräten und Systemen für Bewegungssteuerung und Steuerungstechnik und bietet präzisionsgefertigte Lösungen für zahlreiche Kunden in Gewerbe, Automobil, Industrie und Luftfahrt. Das Unternehmen beschäftigt über 61.000 Personen in 48 Ländern. Parker hat seine jährlichen Dividendenzahlungen an die Anteilseigner über 52 Jahren in Folge stetig erhöht und gehört damit zu den fünf Firmen des S&P 500, die ihre Dividenden am längsten konstant erhöhen konnten.
Quelle: Parker Hannifin GmbH