Foam Extrusion: Precise Dosing of Blowing Agents with Fluctuating Extruder Pressures
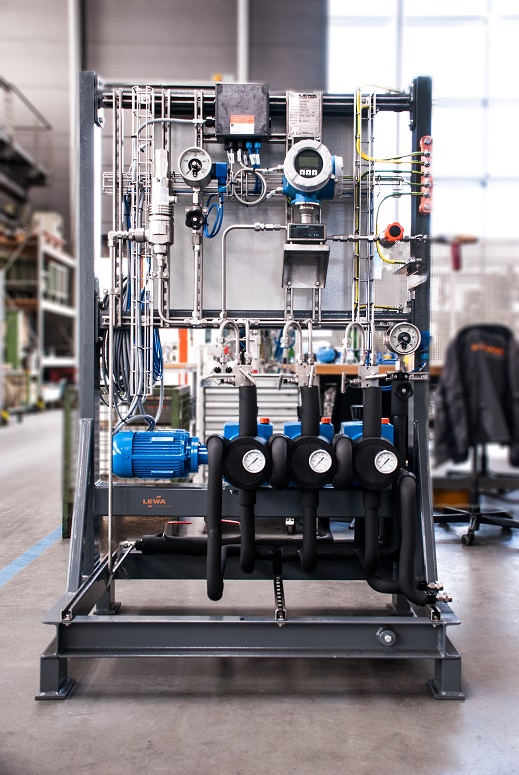
The LEWA ecofoam testing system offers users a cost-efficient opportunity to see the reliable quality of the extruder system and the end products for themselves in everyday operation without obligation.(Image source: LEWA GmbH)
However, the variance in blowing agents and their process conditions, such as high pressure or deviating temperatures, require specified systems and quickly make the extrusion process relatively complex. The LEWA ecofoam metering system provides a remedy. A fail-safe complete solution for all known blowing agents, it is characterized by consistently precise metering even for fluctuating parameters. The LEWA ecofoam testing system offers users a cost-efficient opportunity to see the reliable quality of the extruder system and the end products for themselves in everyday operation without obligation.
Depending on the intended use and desired properties of the plastic product, different blowing agents are used in foam extrusion. For example, they can be carbon dioxide, propane, butane, pentane or halogenated hydrocarbons such as Freon 152a. Although the discharge pressures and temperatures of these media differ from one another, the metering of the blowing agent into the plastic melt must be consistently precise in order to achieve a homogeneous and high-quality end product. The proven LEWA ecofoam metering system was therefore specially designed to meter all common blowing agents precisely and reliably.
Universal extruder system for testing with all blowing agents
To ensure the required constant foam quality, the quantity of blowing agent in the LEWA ecofoam is adjusted proportionally to the rotation speed of the extruder. The smart control technology developed by LEWA itself comes into play here. It continuously compares the signal from the flow meter with the guide signal and regulates the rotation speed of the drive motor accordingly. Due to the pump's pressure-stiff characteristic curve, metering remains constant even for fluctuating extruder pressure.
At its core, the hermetically tight and therefore low-maintenance system consists of a LEWA ecoflow diaphragm metering pump, which delivers the blowing agent at a pressure of 50 to 350 bar. The flow rate depends on the set pressure and the compressibility of the medium. For example, it can be 13 kg/h CO2, 8 kg/h i-butane or 20 kg/h H2O at 250 bar. Since the LEWA ecofoam testing system was designed for all known blowing agents, it is already explosion-proof for flammable media such as propane or butane as standard and is equipped with a cooling unit for carbon dioxide.
To ensure that the system can be easily transported for testing purposes, all components are securely mounted on a common mount base. It can be rented for up to six weeks without obligation, although longer periods are also possible by arrangement. This gives users the opportunity to test the reliable quality of the system and the consistently precise metering of different blowing agents in a real application environment – entirely without financial risk.
Source: LEWA GmbH