Electronic Maintenance Support System by Gemü Improved
The new version 1.2 of the Conexo app and the Conexo portal not only has an expanded range of functions but is also simpler for the user to operate.
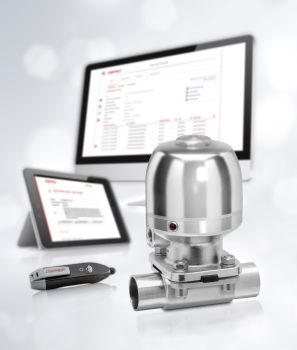
Gemü
With Conexo, Gemü has brought a system to market which electronically supports the user with a wide variety of servicing and maintenance tasks. For it to work, each relevant component of a plant is equipped with an RFID chip. This chip can then be read out by the RFID reader, the Conexo pen. To complement this, the Conexo app is installed on a mobile device. With this system, the entire servicing process becomes more transparent and easier to document. The app actively guides maintenance technicians through the maintenance schedule and directly provides them with all the information assigned to the component, such as test reports, testing documentation, assembly instructions and maintenance histories. The Conexo portal acts as a central element, helping to collect, manage and subsequently process all data.
Close communication with users helped to improve and supplement the system with new functions. Thus, users can not only look forward to even easier operation and a significant increase in data processing performance, but also to greater flexibility when it comes to carrying out servicing. Optimization of functions such as the component search or rights management features, as well as the option to depict components without RFID chips, represent only a selection of the newly added options for the user. "With these new functionalities, we will not only meet our customers requirements even better but will simultaneously increase the productivity of the entire system," says Mario Niklas, the product manager responsible for Conexo.