Editorial: Surface for Mating Hardware
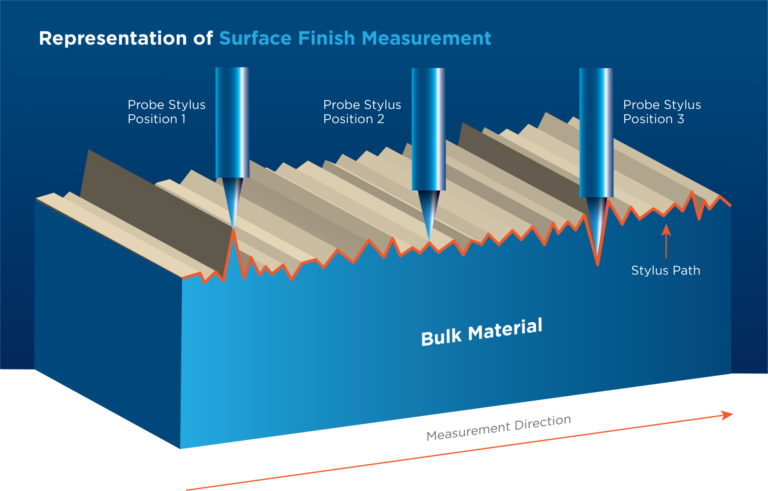
(Image source: Green Tweed & Co. - Corporate)
But what about the hardware that goes with it? Well, some aspects of hardware design can make or break a seal's ability to function and affect the dynamic life of a seal element. The surface finish - the roughness of the two fitting surfaces that compress the seal - of the mating fitting is one such factor that should be considered in the design, as the ideal surface finish determines seal performance and can maximize seal element life.
Surface finish requirements depend on whether the seal is made of elastomer, thermoplastic or other material. The general malleability of elastomers allows for greater variation in surface finish, while stiffer thermoplastics are less adaptable but can sometimes require less lubrication due to their tribological properties. For this reason, surface finish recommendations for a thermoplastic seal are generally finer than those for an elastomer seal.
In addition, the surface finish requirements for applications that seal liquids differ from those that seal gases or vacuums. For sealing gases or against a vacuum, a finer surface finish is recommended because the structure and size of most gases allow them to penetrate through smaller gaps than would be possible for a liquid.
In a dynamic application, the surface finish of the fittings also directly affects the life of a seal. The surface of the fittings must vary to hold process media or lubricants to the surface and reduce friction. However, if the surface is too rough, the movement against the fitting will abrade the sealing element. It is critical to find the right balance to both provide lubrication and maximize seal life.
Further below is a plot of local variations in surface height and roughness, showing how surface finish is generally measured. It's easy to imagine that if there were too many peaks like the one on the left of the diagram, the seal materials would be abraded or worn down by the dynamic contact, not to mention having difficulty adjusting to all the variations in local surface height. The valley on the right side of the image shows how a pocket can form to trap the process medium or lubricant to reduce friction through continuous dynamic cycling.
Choosing the right surface finish for the hardware components in the application can be complex. Generally, 8 to 12 microinches Ra (average roughness) is recommended for dynamic seals and 16 to 32 microinches Ra for static seals. Greene Tweed's experienced engineers can help by accessing application parameters to assist S in selecting the proper surface finish.
Source: Greene, Tweed & Co. – Corporate