Editorial: Optimizing Processing Performance and Reliability in Refineries
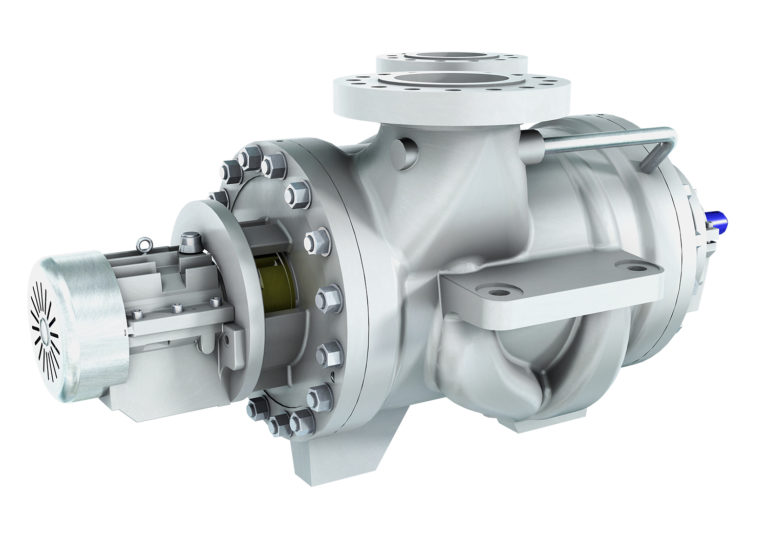
A typical coker charge pump would be a 2-stage radially split pump, API 610 type BB2 (Image source: Sulzer Ltd.)
Throughout the delayed coker plant, pumps of various designs are used to transport high temperature, corrosive fluids through the process.
Scott Graham, Global Product Portfolio Manager - Oil & Gas for Sulzer, looks at the pumps involved in DCUs and how their design affects process reliability and efficiency.
Of the three main types of coker used in oil refineries, the delayed coker is the most common. It supports a non-catalytic thermal process that converts a wide range of residues into high value liquid products such as liquefied petroleum gas (LPG), heavy coker gas oil (HCGO), light coker gas oil (LCGO) and almost pure carbon residue, known as coke, which is also further processed for use in other industries.
The feed material for the DCU is typically the residue from the vacuum distillation tower and often includes other heavy oils. It is heated and sent to one of the coke drums at a temperature between 450 and 500 °C (840 and 930 °F), where typical overhead pressures range from 2 to 8 bar (30 to 115 psia). Under these conditions, cracking occurs and the lighter oil fractions are separated into gas, petroleum and other high value liquids.
A solid coke residue is also produced and remains in the drum before being removed by a high pressure water lance. While this process is being completed, the feed material is directed to the second drum and the process is repeated.
Specialist engineering
Within this process each pump has a specific purpose that requires certain characteristics to retain reliable operation. Depending on the application, the pumps need to meet a variety of design criteria and this requires specialist engineering to deliver the necessary durability in arduous conditions.
From the outset, all process pumps operating in a refinery setting are normally required to meet the current edition of API 610 standard. After that, individual applications will dictate the exact specifications. The coker charge pump would typically be a 2-stage radially split pump, API 610 type BB2, capable of operating at around 370 °C (700 °F) and discharge pressure around 42 bar (600 psi). More importantly, the pump needs to be capable of operating over a wide flowrate while maintaining maximum reliability.
Operating at these higher temperatures means that internal wear part clearances are slightly more than those seen in other applications. However, in this situation the power is lost as heat energy to the fluid, reducing load on the furnace.
Material considerations
One of the major challenges for the coker charge pump is the coke particles that are entrained in the liquid. To prevent the larger particles from choking the eye of the impeller, pumps can be equipped with coke crushers, which reduce the size of the particles and allow them to pass through the impeller.
Predominantly, coker charge pumps are manufactured using API C-6 and A-8 materials, but for naphthenic crudes, 317L stainless steel can be used for its high strength and corrosion resistance. However, 317L is not dimensionally stable when pressurized at high temperatures, allowing wear ring clearances and other toleranced dimensions to become distorted.
An experienced pump manufacturer can resolve this shortcoming by implementing a dimensional stabilizing heat treatment process on 317L casings and pump case covers that are destined for high temperature service.
Close cooperation between the refinery, the engineering procurement construction (EPC) provider and the pump supplier is essential to establish the most effective design of coker charge pump. Agreeing on materials, abrasive service levels, specialized coatings and bearing systems is a vital aspect to developing the most appropriate pump design.
Jet cutting pump
The coke that remains in the drum is periodically removed and during this process the feed material is directed to another drum. Once the coke has been steamed and cooled, high pressure water jets are used to loosen the coke and wash it out of the bottom of the drum.
Jet cutting pumps are high pressure units, around 4’300 psi (300 bar) with a flow rate typically 150 m3/hr (660 GPM) to 300 m3/hr (1320 GPM) and therefore require multi-stage, barrel type diffuser design, API 610 type BB5. All the impellers are stacked in a row and the axial thrust is balanced by a large diameter balance drum.
The water that is used to remove the coke is filtered and recycled back to the jet cutting pump. This means it is possible for some coke particles to pass through the pump, causing accelerated wear, especially on the balance drum, which can dramatically affect efficiency and axial thrust.
Remedial actions
One of the primary indicators of balance drum wear is the temperature of the thrust bearing; a reading over 240°F (115°C) indicates that action is required and that coke cutting efficiency has been reduced. Maintenance can be needed every few months. However, this interval can be significantly extended by working with an expert in specialized coatings.
By installing hard-facing coatings in high velocity areas, it is possible to extend this maintenance period to years, rather than months. But, the process of preparing the base material and applying these coatings requires considerable expertise and knowledge of materials science.
A specialized coating enhances the performance of a component, but each one is different and the processes to apply them vary as well. Only through years of experience and expertise in the metallurgical properties, the application technology and quality control procedures, can a reliable and durable protective system be realized.
Performance through partnership
Every pumping application within the setting of a refinery has unique challenges. By working in partnership with an experienced manufacturer, such as Sulzer, it is possible to optimize the performance of existing assets and streamline the process to design and deliver replacements. Furthermore, as a specialist maintenance provider, Sulzer can also provide expert support for a wide variety of rotating equipment, improving reliability and efficiency.
With a wide range of API 610 pump designs, Sulzer engineers each pump to suit an individual application, ensuring optimized efficiency and reliability. With a worldwide network of manufacturing and maintenance centers, the company offers unrivalled support the oil and gas sector.
Source: Sulzer Ltd.