Druckerei spart Energie mit neuer Druckluftstation und nachgerüsteter Wärmerückgewinnung
Hohe Produktivität und nachhaltige Produktion: Mit dieser Philosophie ist Aumüller Druck in vierter Generation erfolgreich. Effizient und zukunftsfähig ist auch die Druckluftversorgung: Anlässlich der Einführung einer neuen Generation von Druckmaschinen und der Erweiterung der Produktionsfläche wurde das Druckluftkonzept komplett erneuert – mithilfe modernster Kompressoren und Wärmerückgewinnung von Atlas Copco.
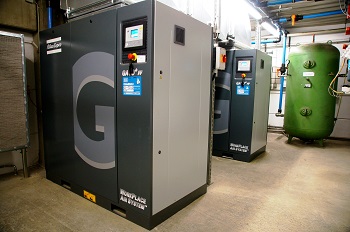
In Station 1 arbeiten zwei öleingespritzte Schraubenkompressoren des Typs GA 30+ FF von Atlas Copco. Kältetrockner, Druckluftfilter, Kondensatableiter und -trenner sind bereits integriert. (Foto: Atlas Copco)
Wer der Aumüller Druck GmbH & Co. KG in Regensburg einen Besuch abstattet, kann dort durchaus schon mal dem Bürgermeister von Regensburg begegnen. Denn der 1888 gegründete Familienbetrieb blickt nicht nur auf eine langjährige Firmentradition zurück, sondern engagiert sich kontinuierlich für seine Heimatstadt. So lobt das im Stadtteil Haslbach ansässige Unternehmen beispielsweise seit dreizehn Jahren den mit 10.000 Euro dotierten Aumüller-Schulpreis aus, der besondere Leistungen und Konzepte von Lehrern oder Lehrer-Teams honoriert. Dieser wird im jährlichen Wechsel mit dem Aumüller-Integrationspreis verliehen, der Integrationsprojekte im Raum Regensburg würdigt.
„Wir sind ein Mittelstandbetrieb mit rund 150 Mitarbeitern“, erklärt Geschäftsführer Christian Aumüller, der gemeinsam mit seinem Bruder Stefan das Unternehmen leitet. „Bei dieser Größe ist es eigentlich ungewöhnlich, dass wir eigene Preise vergeben.“ Auf der anderen Seite habe Aumüller Druck selbst bereits eine ganze Reihe von Auszeichnungen erhalten – unter anderem als Familienbetrieb, Umweltbetrieb und Innovationsbetrieb. Gerade sei man wieder nominiert, als sozialstes Unternehmen bei den Druck & Medien Awards in Berlin.
Streben nach höchster Produktivität
60 Prozent aller Mitarbeiter bei Aumüller Druck sind echte stille Gesellschafter und damit am Unternehmenserfolg beteiligt. Auch das, so Aumüller, sei für den Mittelstand ein eher ungewöhnliches Modell. „Wir definieren uns über die Produktivität“, konstatiert der Firmenchef. Der Wettbewerb sei in der Branche sehr stark, in den letzten zehn Jahren sei jede dritte Druckerei vom Markt verschwunden. Dem Trend müsse man etwas entgegensetzen: „Wir positionieren uns am Markt durch Produktivitätsführerschaft, nicht durch Kostenführerschaft. Wir wollen einen hohen Output und nutzen daher ausschließlich industrielle Maschinen mit sehr großer Druckkapazität.“
Qualität und Kontinuität
Ebenfalls Teil der Firmenphilosophie sind langjährige Geschäftsbeziehungen. Mit BMW arbeiten die Regensburger bereits seit 60 Jahren zusammen. Bei Audi besitzt die Druckerei die Lieferantennummer 89 – inzwischen sind diese Zahlen sechsstellig. Auch in Sachen Druckluft setzt Aumüller auf Kontinuität und Qualität: Seit Jahren vertraut man auf die Technik und die regelmäßigen Innovationen von Atlas Copco.
Druckluft wird bei Aumüller in fast allen Produktionsschritten benötigt. Angefangen bei der Belichtung der Druckplatten, wo der sehr empfindliche Laserbelichter mit absolut ölfreier Druckluft arbeitet. Die benötigte Qualität wird durch einen separaten Ölabscheider sichergestellt. Ferner wird das Papier mit viel Druck- und Saugluft durch die Maschinen gezogen. Auch die gesamte Weiterverarbeitung, also Schneid- und Falzprozesse, das Sammelheften und Klebebinden, benötigen Druckluft: „Unsere Druckmaschinen arbeiten eigentlich autark mit eigenen integrierten Kompressoren“, erklärt Hans Zenger, der den Bereich Logistik leitet und für die Betriebstechnik verantwortlich ist. „Sie haben zur Sicherheit aber auch Anschlüsse für externe Druckluft.“ Darüber hinaus wird das für den Falzprozess benötigte Vakuum ebenfalls mittels Druckluft erzeugt. Hier arbeitet Aumüller Druck mit einem sogenannten Piab-System, das die zentral erzeugte Druckluft über spezielle Düsen an Ort und Stelle in ein Vakuum umwandelt.
Druckluftversorgung muss mit wachsender Produktion mithalten
Mit dem Start einer neuen Druckmaschinen-Generation im Jahre 2008 und einer Erweiterung der Produktionsfläche 2011 hat Aumüller seine Kompressoren-Stationen komplett modernisiert, das Druckluftnetz saniert und neu organisiert. Damit wurde die Druckluftversorgung nicht nur der stark gestiegenen Produktivität des Unternehmens angepasst, sondern deutlich effizienter gestaltet. Seinen Abschluss fand das Projekt im August 2015 mit der Inbetriebnahme der integrierten Wärmerückgewinnung bei den letzten beiden der heute insgesamt fünf Kompressoren.
„Wir haben unsere Druckluftversorgung in den letzten Jahren stetig erweitert, denn sie musste mit unserer stark wachsenden Produktion mithalten“, erklärt Zenger. „Zunächst hatten wir hier zwei getrennte Netze mit je einer Druckluftstation. Mit der Fertigstellung von Bauabschnitt 5 im Jahre 2011 haben wir eine Verbindung zwischen beiden Produktionsbereichen geschaffen und in der Folge beide Druckluftnetze vereinigt.“ Die Zusammenlegung ging mit einer kompletten Sanierung des Netzes einher. Heute umschließt eine Ringleitung die komplette Produktion; Stichleitungen versorgen die einzelnen Verbraucher. Aufgrund des stark gestiegenen Bedarfs wurde zudem ein größerer Leitungsquerschnitt gewählt. Die Druckluft wird aus Platzgründen weiterhin in zwei Stationen erzeugt, die nun aber in das gemeinsame Netz speisen. „Eine zuverlässige und konstante Druckluftversorgung ist uns sehr wichtig“, betont Zenger, „und die haben wir mit dem neuen Konzept erreicht.“
Druckluftaufbereitung komplett im Kompressor integriert
In Station 1 arbeiten zwei öleingespritzte Schraubenkompressoren des Typs GA 30+ FF von Atlas Copco. Bei der FF-Version (Full Feature) sind ab Werk bereits Kältetrockner, Druckluftfilter, Kondensatableiter und -trenner im Kompressorgehäuse integriert. Beide Kompressoren verfügen über eine integrierte Wärmerückgewinnung. Diese wurde im August 2015 in Betrieb genommen und gibt in der kalten Jahreszeit einen Teil der Wärme über Wärmetauscher an den Vorlauf einer der beiden Heizungsanlagen ab. Im Sommer muss die überschüssige Wärme abgeleitet werden. „Die beiden GA 30+ FF laufen unter der Woche kontinuierlich durch und werden je nach Bedarf von einem oder mehreren Kompressoren aus Station 2 flexibel unterstützt“, erläutert Hans Zenger das Druckluftkonzept.
Neue Kompressoren sparen 17 % Energie
Die GA 30+ FF sind die jüngsten der nun insgesamt fünf Kompressoren bei Aumüller Druck. Sie sparen gemäß der Vorab-Simulation von Atlas Copco gegenüber der früheren Installation etwa 17 % an Energie – oder jährlich über 20.000 Euro sowie 71 Millionen Kilogramm CO2. Und das schon ohne die Wärmerückgewinnung. An den tatsächlichen Werten ist Christian Aumüller nur in zweiter Linie interessiert: „Mir geht es gar nicht so sehr um die Amortisationszeit, sondern um das optimale System für hohe Produktivität und Effizienz“, erklärt der Druckerei-Inhaber. „Denn Umwelt und Nachhaltigkeit stehen bei uns an erster Stelle: Ich möchte mit so wenig Energie wie möglich unseren Bedarf an Druckluft erzeugen.“ Ob sich die Investition dann in drei, vier oder fünf Jahren auszahle, sei zweitrangig. Dass sie es tut, steht für Aumüller außer Frage. „In jedem Fall wird die nun neu aufgebaute Wärmerückgewinnung an den beiden neuen Kompressoren die Energieausnutzung noch einmal deutlich verbessern“, betont Aumüller.
Nachgerüstete Wärmerückgewinnung rechnet sich in sechs Monaten
In Station 2 stehen die beiden drehzahlgeregelten Schraubenkompressoren GA 30 VSD FF und GA 18 VSD FF sowie ein GA 22+ FF. VSD steht für „Variable Speed Drive“, das heißt, die Motordrehzahl wird exakt an den jeweiligen Luftbedarf angepasst. Alle drei Kompressoren sind mit externen Energierückgewinnungsmodulen ER-S1 von Atlas Copco verbunden. Diese speisen die bei der Verdichtung entstehende Wärme je nach Bedarf in den Vorlauf der zweiten Heizungsanlage oder in einen 2000 Liter großen Pufferspeicher ein. „Die Wärmerückgewinnung haben wir 2011 zusammen mit dem Bauabschnitt 5 verwirklicht“, berichtet Aumüller. „Die Amortisationszeit für diesen Projektabschnitt betrug nicht einmal ein halbes Jahr.“
Dass heute bei Aumüller Druck insgesamt fünf Kompressoren arbeiten, ist dem stetig steigenden Druckluftbedarf im Unternehmen geschuldet. „Es ist nicht so, dass wir genau mit dieser Anzahl geplant hätten“, erläutert Christian Aumüller. „Wir hatten die Anlage ursprünglich mit zwei Kompressoren konzipiert. Und dann mussten wir über die Jahre aus dem Bestehenden immer wieder ein optimales Netz machen. Das war eine Herausforderung.“ Gesteuert werden die fünf Kompressoren effizient und übergeordnet vom ES-Energiesparsystem von Atlas Copco. Dieses koordiniert die Maschinen so, dass diese möglichst immer an ihrem optimalen Betriebspunkt laufen. Am Wochenende reicht die Leistung des GA 18 VSD FF, um den wesentlich geringeren Druckluftbedarf zu decken.
Service und Wartung für die komplette Druckluftanlage liegen in den Händen von Atlas Copco. Aumüller vertraut bereits seit vielen Jahren auf die Erfahrung der lokalen Partner im eng geknüpften Servicenetz der Essener Druckluftspezialisten. Seit März 2015 profitiert das Unternehmen nun auch von der Xtended Warranty+ – einem neuen Angebot von Atlas Copco. Dieses umfasst nicht nur alle Service- und Wartungsleistungen für die Druckluftanlage, sondern ist darüber hinaus mit einer auf fünf Jahre verlängerten Garantie für die Maschinen verbunden.
Betriebsdruck von 10 auf 6,5 bar gesenkt
Durch die Sanierung des Leitungsnetzes und die Optimierung der Druckluftversorgung konnte der Betriebsdruck von 10 bar auf 6,5 bar gesenkt werden. Wendet man hier die Faustformel an, die von 6 bis 7 % geringeren Energiekosten pro Bar ausgeht, konnte Aumüller Druck seinen Stromverbrauch allein durch diese Maßnahme um rund ein Fünftel reduzieren. Die absoluten Zahlen sind schwierig zu interpretieren, da über die Jahre mit der Produktion auch der Luftbedarf gewachsen ist. „Aber auf das Gesamtkonzept sind wir schon stolz“, sagt Christian Aumüller.
„Mit unserer Operation Nachhaltigkeit haben wir vor 25 Jahren begonnen und sind noch lange nicht am Ziel“, resümiert Aumüller. „Nachhaltigkeit bedeutet für uns, effizienter zu werden bei Produktion, Logistik und Energie. Es bedeutet, Mitarbeiter durch geringere Lärm- und Staubemissionen zu schützen und die Umwelt durch verminderte Emissionen und weniger Abfall zu entlasten. Außerdem sehen wir es seit Jahren als unsere Aufgabe und Pflicht, in neueste und möglichst energiesparende Maschinen und Produktionsmittel zu investieren.“
Quelle: Atlas Copco Holding GmbH