Custom Vertical Progressing Cavity Sump Pump Provided for Oil Storage Application
When a major energy pipeline company looked to streamline their pumping system for their waste oil tanks for the temporary storage, they called on Netzsch to design and build customized vertical cavity sump pumps for lower maintenance and opera-tional efficiencies.
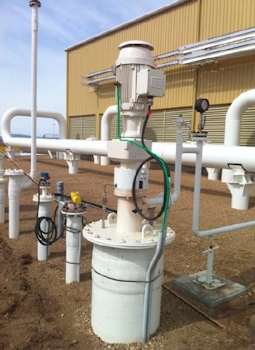
A need to reduce maintenance and simplify the transfer of oil from an underground tank back into the pipeline required Netzsch to design and build a custom, 10-stage vertical progressing cavity sump pump to satisfy customer requirements. (Image: Netzsch)
Along the customer’s pipeline are pumping stations needed to power the liquid fuels through the pipeline. At each pump station, there is a 5,000-gallon (19,000-liter) underground storage tank (buried below the frost line to prevent the liquid from freezing) used as a collection point for waste oil from service work that is performed on main pipeline pumps.
As the collection tanks fill to capacity, the customer needs to pump the liquid from the tank back into the pressurized pipeline. This process had consisted of a two-pump system – with a cantilever pump used to lift the waste oil out of the tank and a high-pressure piston plunger injection pump to move the oil back into the pipeline system.
Netzsch PC Pumps are tailor-made for this application, with dimensions (length, mounting flange, etc.) to fit the customer’s existing underground tank. This pumps are also designed to operate in reverse. The rotor/stator system (pump elements) are located at the lowest point, so dry-running will be avoided. The space-saving design of the entire pump (besides the drive and discharge flange) is integrated into the tank, providing for a very neat and clean installation. This also means that there is no additional effort needed to heat and isolate external equipment – a very important attribute in ambient operating temperatures down to -40 degrees C.
With the critical operating nature of the oil and gas transport industry, the customer has very high quality control requirements. Netzsch Nemo Pumps are produced in accordance with API 676 and shaft seals in accordance with API 682.
Netzsch was successful in supplying 14 pumps for the customer. To date, all of the pumps are in operation with no concerns or issues from field operators. With many of these pump stations in remote locations, major benefits to the customer include less operational cost and field maintenance with only one electric motor running a single pump as well as solving the pipe pulsation issue. With the success of this installation, the customer has changed their current specification regarding these sump pumps to recommend the use of the Netzsch pump for this application.