Croissance du marché des canettes: Coca-Cola European Partners investit dans deux gammes KHS
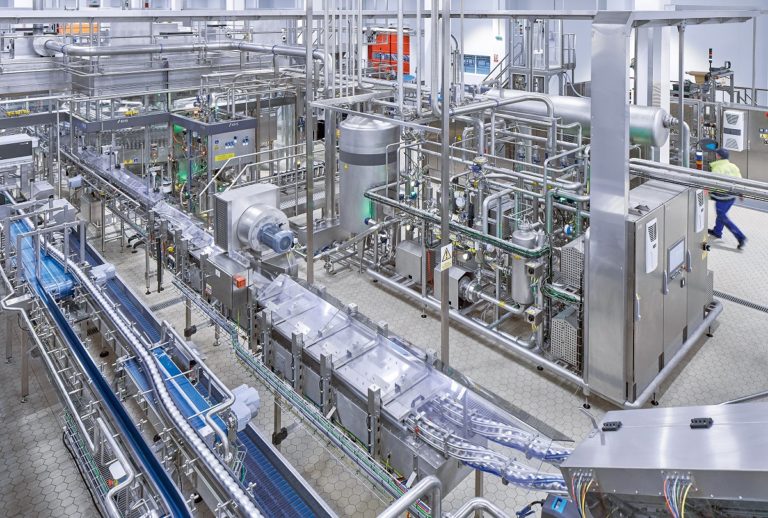
Sur la droite se trouve le système de mélange KHS Innopro Paramix C, au premier plan le bidon vide alimente le remplisseur et à gauche le convoyeur qui transporte les bidons remplis et sertis vers le conditionneur. (Source de l'image: KHS GmbH)
À la fin du 19e siècle, la ville de Wakefield, dans le nord de l'Angleterre, est devenue une plaque tournante de la révolution industrielle britannique. Autrefois l’un des principaux fournisseurs d’orge et de malt du pays, des filatures de laine, des briqueteries et des ouvrages d’ingénierie ayant des liens étroits avec l’industrie minière à croissance rapide s’établissent. Parmi les entreprises locales se trouvaient plusieurs brasseries, ce qui signifie que la ville peut aujourd'hui se prévaloir d'une certaine tradition dans la production de boissons.
Cela a maintenant été relancé: depuis 1989, Wakefield, qui, avec Leeds, Bradford et Huddersfield, constitue l'une des zones les plus densément peuplées du Royaume-Uni, abrite la plus grande usine de boissons non alcoolisées d'Europe. Ici, sur l'un des cinq sites de production en Grande-Bretagne, Coca-Cola European Partners (CCEP) remplit jusqu'à 10 000 canettes et 1 800 bouteilles en PET de boissons gazeuses par minute - 24 heures sur 24, 7 jours sur 7. Cela représente 45% du volume total produit par CCEP au Royaume-Uni: exprimé en chiffres absolus, soit 176 millions d’unités de vente ou un milliard de litres de produit fini par an.
La plus grande usine de boissons d'Europe
L'usine dispose d'un total de huit lignes de remplissage; cinq de ces canettes de traitement avec des volumes de 330 et 500 millilitres, les trois autres bouteilles en PET contenant 500 millilitres et 1,0 à 2,25 litres, produisant environ 300 unités de gestion de stock ou SKU. Le plus grand embouteilleur indépendant de Coca-Cola au monde coopère avec KHS en tant que partenaire technologique: le fabricant de machines et de systèmes de Dortmund est responsable de quatre des cinq remplisseuses de boîtes et de deux lignes de mise en conserve clé en main. Les deux dernières lignes 4 et 5 ont été installées et mises en service en un an. Après que la ligne 4 ait été un succès total dès le premier jour en ce qui concerne la disponibilité et l'efficacité, l'embouteilleur a alors chargé KHS de fournir une deuxième ligne de mise en conserve. Le cœur de chaque ligne est le remplisseur de canettes Innofill Can DVD - ici avec une capacité allant jusqu'à 120 000 canettes par heure.
Flexibilité requise
«L’objectif de notre investissement était bien entendu d’augmenter la capacité», déclare Michail Skarpathiotakis, chef de projet senior au siège du CCEP à Uxbridge, près de Londres. «Chacun peut compter!» L'accent a donc été mis sur les multipacks en carton qui sont produits dans une grande variété contenant entre quatre et 30 conteneurs. Pendant la crise corona, où les gens passent plus de temps chez eux, ce type de pack connaît actuellement une croissance des ventes qui se chiffre à deux chiffres. Les emballeurs rétractables enveloppants Innopack Kisters intégrés sur ces deux lignes sont ainsi extrêmement puissants et fiables.
En tant qu'embouteilleur qui vise à maintenir son stock au minimum grâce à son vaste portefeuille de produits, CCEP attache une grande importance à une flexibilité maximale dans la production. Cela nécessite avant tout des changements de format rapides. Le fait qu'environ 40% du temps disponible sur la nouvelle ligne 5 soit consacré aux changements de format et au nettoyage en dit moins sur le temps nécessaire aux changements de produit, mais indique plutôt qu'il y en a un grand nombre. Lorsqu'on lui demande combien il y en a réellement, le directeur des opérations de Wakefield, Kerry Morgan-Smith, répond: "Trop." Cependant, compte tenu des demandes de plus en plus individuelles des consommateurs, c'est la seule bonne façon de faire les choses, poursuit-elle.
Durable à tous égards
Outre les niveaux de rendement et d'efficacité du CCEP, l'embouteilleur fait également une tentative record d'être plus durable, établissant des normes en matière de recyclage, de prévention des déchets et de consommation d'énergie et d'autres ressources. Comme tous les sites de fabrication en Grande-Bretagne, Wakefield adopte également la devise «zéro déchet», aucun déchet n'étant acheminé vers les sites d'élimination des déchets. Tous les emballages sont 100% recyclables. «Je pense que nulle part ailleurs en Europe le débat sur les plastiques n'est aussi passionné qu’en Angleterre», soupçonne Andy Carter, responsable des ventes de KHS pour la Grande-Bretagne et l’Irlande. «La pollution de l'environnement et notamment de nos mers par les déchets plastiques est omniprésente dans nos médias. Cela signifie que les consommateurs trouvent ce sujet extrêmement important. »
La canette de boisson jouit d'une popularité supérieure à la moyenne au Royaume-Uni. Alors qu'en Allemagne, les bouteilles en PET représentent 81% du mélange d'emballage CCEP et les canettes à peine 5%, le ratio chez les Britanniques est de 46% à 35%. Cela en fait les meilleurs utilisateurs de canettes en Europe. Néanmoins, l’embouteilleur réagit à la prise de conscience croissante des consommateurs face au problème du plastique. «Depuis octobre, nous utilisons 50% de matières recyclées dans nos bouteilles en PET», souligne Morgan-Smith. «C'est l'équivalent de 21 000 tonnes métriques par an. Et nous travaillons à augmenter encore ce montant. " Les habitudes d'achat ont également changé en ce qui concerne les emballages secondaires. «Nous constatons que la part des emballages en carton entièrement fermés est en augmentation, au détriment des emballages rétractables emballés dans un film.»
Priorité aux économies sur les ressources
En ce qui concerne son approvisionnement en énergie, Wakefield est en passe de devenir autosuffisant. «Nous avons investi un million de livres dans la construction d’une centrale combinée de chaleur et d’électricité», rapporte Morgan-Smith. «Cela signifie que nous pouvons produire de l'énergie renouvelable sur place et contribuer à économiser 1 500 tonnes de CO2 par an. Non loin de là, nous exploitons également un parc photovoltaïque de la taille de douze terrains de football qui alimente l'usine en énergie solaire. Cela couvre environ 15% de notre consommation totale d'électricité, ce qui nous permet de réduire considérablement notre empreinte carbone. » L'usine d'embouteillage répond désormais à 100% de ses besoins énergétiques grâce à des sources renouvelables. CCEP est également un acteur de premier plan lorsqu'il s'agit de réduire progressivement la quantité d'eau consommée lors de la production. Environ 1,3 litre d'eau est utilisé pour chaque litre de produit fini - un chiffre qui a diminué de moitié au cours des 15 dernières années.
L'embouteilleur britannique de boissons non alcoolisées attache également une grande importance à la durabilité en ce qui concerne l'utilisation des matériaux. «Par le passé, nous avons mis en œuvre un certain nombre de programmes efficaces pour réduire le poids de nos canettes et de nos bouteilles», explique Morgan-Smith. «En 1994, notre bouteille en PET de 500 millilitres pesait par exemple 36 grammes; il ne pèse plus que 19,9. »
Client régulier
Comme pour chaque projet du système Coca-Cola, KHS a dû participer à la procédure d'appel d'offres habituelle. Le groupe dispose d'une plate-forme d'appel d'offres extrêmement sophistiquée qui comprend un tableau de bord détaillé des paramètres techniques commerciaux, quantitatifs et qualitatifs. KHS a obtenu le meilleur résultat sur ce tableau de bord, prouvant ainsi que ses machines atteignent également les objectifs de productivité fixés dans le cadre des conditions techniques et financières données pour la ligne 5.
Une fois le contrat attribué, les entreprises se sont heurtées à un obstacle que personne n'aurait pu prévoir, comme se souvient Skarpathiotakis. «Nous étions encore au stade de la préparation lorsque nous avons été soudainement confrontés à Covid-19. Ce fut naturellement une période extrêmement difficile pour nous tous. Andy Carter nous dit: «Le secteur des aliments et des boissons a été classé comme une industrie clé. Il nous restait cependant à surmonter de nombreux obstacles bureaucratiques pour prouver la nécessité du projet et permettre à nos collègues de traverser des frontières à travers l'Europe qui s'étaient soudainement fermées. En ces temps difficiles, nous avons dû créer un environnement protégé, mettre en place une distanciation sociale et organiser l'hébergement et les repas de nos employés. Nous nous sommes donc tous rassemblés et avons très rapidement trouvé une solution pragmatique. Cela impliquait également de se lever au milieu de la nuit. «Les douaniers britanniques à Calais en France m'ont téléphoné une fois à deux heures du matin pour vérifier si les gens qu'ils attendaient là-bas étaient vraiment autorisés à entrer dans le pays.
Cependant, avant que le projet ne puisse démarrer, il a fallu trouver un compromis entre l’usine de Wakefield et le siège du CCEP. Certains collègues locaux étaient au départ sceptiques quant au fait que des ingénieurs de l'extérieur du Royaume-Uni passent du temps à l'usine pendant la pandémie. Le siège, quant à lui, souhaitait que l'installation se déroule comme prévu. «En tant que l'un des très rares partenaires contractuels à avoir accès aux locaux de l'usine pendant le verrouillage, KHS a dû agir comme une sorte de modèle», explique Skarpathiotakis. «Cela a vraiment très bien fonctionné.»
Installation pendant le verrouillage
L'installation a commencé une semaine après que l'Angleterre soit entrée dans le verrouillage total. Dans ces circonstances difficiles, le projet s'est également révélé être un énorme défi technique. «Avec KHS, nous avons réussi à installer deux lignes en l'espace de douze mois seulement», sourit Morgan-Smith. «Nous n'avions jamais fait cela auparavant - au moins trois à quatre ans s'écoulent généralement entre des projets comme ceux-ci. Nous sommes passés de zéro à soixante - et en pleine pandémie aussi! Ce fut un véritable coup de chance de travailler avec une équipe aussi engagée et exceptionnelle où chaque membre se concentrait sur nos exigences en tant que client. Au cours de sa carrière, elle a travaillé avec diverses autres équipes de projet et est bien consciente des difficultés que les différentes mentalités et barrières linguistiques peuvent causer. La coopération avec KHS, cependant - et ici elle a même déroulé toute une liste de noms de personnes dans l'équipe - était exceptionnellement harmonieuse, très agréable et s'est déroulée sans heurts.
En fin de compte, la décision de la direction s’est avérée correcte: il n’ya pas eu d’infections car toutes les personnes impliquées ont exercé une énorme discipline dans le respect des règles extrêmement strictes d’hygiène et de distanciation sociale. La ligne a été installée et mise en service sans aucun problème ni délai. Dès le premier jour, la nouvelle ligne s'est avérée extrêmement efficace et a dépassé les attentes les plus élevées. Tout le monde est très satisfait de l'heureux résultat du projet. «Nous pouvons tous être vraiment fiers de ce que nous avons accompli ici ensemble», estiment Skarpathiotakis et Morgan-Smith, légèrement incrédule, «Je ne sais toujours pas comment nous y sommes parvenus!»
Source: KHS GmbH