Ceramic Axial Bearings with Sealing Function
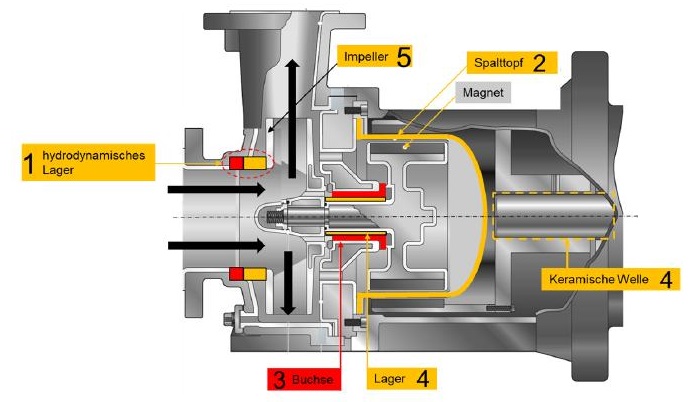
Ceramic bearings. (Image source: FCT Ingenieurkeramik GmbH)
In order to further expand the value chain, they not only deal with the design, but also with the advanced manufacturing processes. The focus for 2020 is on expanding the mechanical seal production, which is mainly in the area of axial bearings (hydraulic / pneumatic).
Where does the motivation come from?
FCT Ingenieurkeramik is permanently in cooperation with customers, but also on their own initiative to analyze and optimize tribological systems. Potentials can be generated, particularly in the field of pump technology. The combination of the sealing function in the suction mouth area to reduce internal leakages and the mapping of an axial bearing in an assembly increases the hydraulic efficiency on the one hand and can absorb the axial forces on the other. For purely mechanical pumps, the axial force results from the hydraulic axial thrust, with electric pumps it is a combination of hydraulic axial thrust and the axial force from the electric drive. This arrangement increases the overall efficiency, reduces the friction and reduces the number of parts, since any additional axial bearing systems are unnecessary.
How is this realised?
This is possible through the continuous development of the molding processes.
The combination of in-house material development, in direct interaction with the process landscape, enables them to reproduce high accuracies already in the master molding process. It is therefore no longer necessary to follow up on complex hard machining processes. Only the areas subject to selective stress are hard-machined.
How is buoyancy provided?
In such systems, it is necessary to set application-specific boundary conditions. On the one hand, the system should be able to run in hydrodynamics even at low speeds. The dry or mixed friction proportions must be reduced to a minimum. After the system has floated up, it is of fundamental importance that the gap pressure between the slide rings is designed accordingly to absorb the axial forces and to ensure the sealing function between the suction side and the pressure side. This is achieved through specially structured surfaces. FCTI basically differentiate between micro and macro structures that provide the necessary tribology. Microstructures are usually introduced using laser processing, while macrostructures can be mapped directly using the shaping process. The correspondingly developed granules (feedstock) make this possible. Such structures are designed in close cooperation with customers and development partners.
The medium-term goal is to improve existing systems by substitution and to use them in new developments right from the start. FCTI can implement this for very small quantities as well as for large series.
Source: FCT Ingenieurkeramik GmbH