Celeros Flow Technology Solves Pump Performance Issues for Major Water Customer
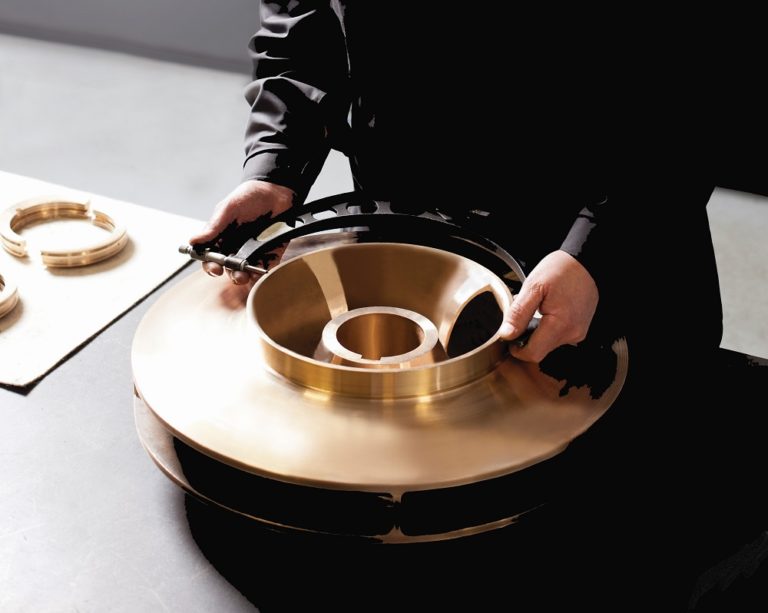
Replacing cast iron impellers with ones of aluminium bronze more than doubled MTBF for one Celeros FT water industry customer. 8Image source: Celeros Flow Technology)
The site investigation and subsequent materials upgrade carried out by the Celeros FT team achieved a 50% increase in pump operational life and delivered major cost savings by dramatically reducing Mean Time Between Failures (MTBF).
Seven-year glitch
The four Uniglide pumps in question had been in operation for approximately seven years but had not been subject to any serious maintenance in that time. The first indication that there were any issues with the pumps was a drop in performance. As the original pump manufacturer, ClydeUnion Pumps (a Celeros Flow Technology brand) was invited to conduct a comprehensive health check of the pumps to determine the reason for their reduced performance. A qualified team of engineers attended the site to investigate the customer’s concerns.
“There are numerous reasons why pumps may run less efficiently than they should,” explains Mike Golds, Global Upgrade and Rerate Programme Manager at Celeros FT. “These might include a change in process parameters or operational conditions; alterations in the operational environment, such as a change in temperature or humidity; general wear and tear caused by variants in the duty cycle, contaminant levels and so on; or a change in the properties of the fluid being pumped.
“Our pump aftermarket service combines the vast engineering expertise inherent in our team with access to sophisticated analysis tools. This means we can not only pinpoint the root cause of any performance issues, but also model a number of potential solutions to identify which will deliver the best outcome for our customer, prior to any investment being made.”
Finding a solution
Initial testing confirmed that the performance of the Uniglide pumps was significantly down on original design parameters. When the top half casing was removed, the Celeros FT team discovered that the impellers on all four pumps were badly damaged and the wear rings were severely worn.
“Upon investigating the root cause of the damage, we determined that the water supply tank often dropped to a low level, which resulted in cavitation occurring,” explains Mike Golds. Over time, this cavitation had caused holes to develop in the impeller inlet vanes on all four Uniglide pumps. Further discussion with the customer made it clear that the low tank levels could not be prevented, which meant that the impellers as originally specified would have to be replaced every six years.
Maintenance of this order would be costly, so Celeros FT proposed a materials upgrade as a more cost-effective and long-term solution. Their proposal was to replace the existing cast iron impellers with ones of aluminium bronze (material BS 1400 AB2), which is more resistant to cavitation damage. The customer accepted this recommendation.
Celeros FT manufactured the new impellers at the ClydeUnion Pumps site, complete with new wear rings for the four pumps. The upgraded units were then reassembled and tested again to ensure they met performance requirements.
Outcomes
Replacing the impellers and fitting new wear rings on the Uniglide pumps achieved an immediate 6% increase in performance. Despite their exposure to cavitation, the new aluminium bronze impellers have a design life in excess of 15 years - more than doubling the Mean Time Between Failures (MTBF). Return on investment for this project was calculated to be within two years.
Source: Celeros Flow Technology