Better Pump Control Improves Polymer Dosing Accuracy
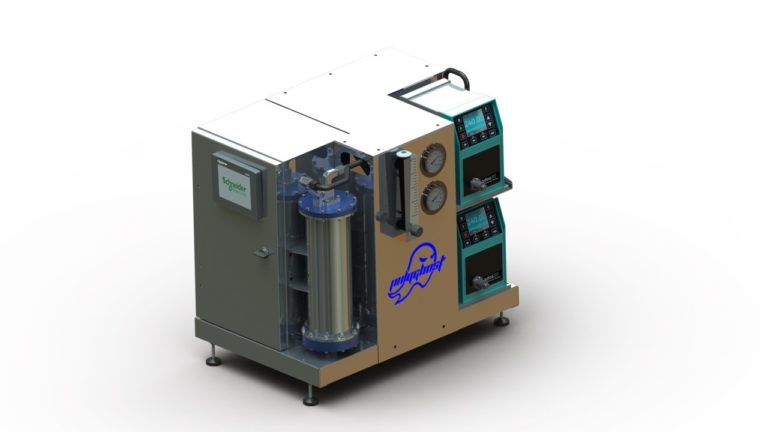
Qdos pump (Image source: Watson-Marlow Fluid Technology Group)
The need to build skids is commonplace in applications such as polymer dosing, a process employed to eliminate unwanted solid particles from liquid streams in sectors that include water and wastewater, mining, pharmaceutical, pulp and paper, and beverage. Skid builders serving these industries are finding that the enhanced process control offered by Qdos peristaltic metering pumps from Watson-Marlow Fluid Technology Group (WMFTG) is paying significant dividends.
The right blend
A case in point is PolyGhost. Based in Puerto Rico, the company has applied its name to their recently 2020 patented technology that continuously blends multiple chemicals, additives and liquid polymers inside a mechanical mixing chamber.
PolyGhost offers its skids using Qdos peristaltic pumps, as they do not require regular and expensive maintenance, and deliver high levels of process control. When clients need full control of polymer blending for applications such as the optimisation of sludge dewatering or separation processes, PolyGhost solutions meet these requirements by integrating the company’s PolySurf+ software with Qdos Universal pumps.
This level of control helps reduce polymer consumption, increase cake dryness, improve solids recovery, lower energy consumption and reduce maintenance costs.
In control
As part of a typical sequence for a PolyGhost skid, once the operator verifies that the water control valve is open and the pump dose rate has been set, the start button is pushed. Here, the dilution water solenoid valve receives a PLC signal to open. This dilution water starts flowing through the system, with flow meter readings sent back to the PLC. If water flow is passing through the system correctly, after 20 seconds the PLC sends a signal to start the polymer blending system. A further 15 seconds later, the PLC sends a signal to the Qdos Universal pump to begin dosing at the specified rate.
PolyGhost uses the input/output connections on the interface of the Qdos Universal+ to control the pump from the panel of the polymer blending system, allowing run/stop commands and flow rate adjustment.
Qdos users can determine the level of control as the pumps come in five variants: from manual (manual control via keypad and display for basic tasks), to the Universal+ (ultimate flexibility for automatic and manual control with five configurable outputs) chosen by PolyGhost.
The Universal+ is proving increasingly popular as it offers remote feedback capability, informing users of its speed via a 4-20 mA output.
Rapid return-on-investment potential
Typically, the required accuracy of PolyGhost applications is between 98 and 100%, a suitably high level that helps customers to save money. According to the company, in liquid polymer blending tasks, a client that uses diaphragm pumps is needlessly losing money. Every time PolyGhost visits a plant, it first determines the type of pump in use. If the customer is deploying diaphragm pumps, PolyGhost says it can optimise the user’s process with Qdos units, guaranteeing savings of at least 30% in polymer consumption, and sometimes up to 65%.
A major advantage of the control capability provided by Qdos pumps is a reduction in chemical use through higher accuracy metering. Qdos provides accurate and linear flow even when process conditions vary. Users can achieve accuracy of ±1%, alongside repeatability (precision) of ±0.5% and turndown up to 20,000:1.
Fully automatic
Taking advantage of fully automatic control via a pump such as the Qdos Universal+ helps companies like PolyGhost to ensure the reliability and repeatability of dosing accuracy. In turn, while chemical savings accrue thanks to the avoidance of overdosing, it is also possible to avert any potential for under-dosing, which is hugely significant in sectors such as water and wastewater treatment.
Of course, both peristaltic and diaphragm pump types can offer 100% dosing accuracy, but if a pump needs additional components in order to operate correctly, such as the required by a diaphragm pump, dosing accuracy will start to decrease because of operational and mechanical variables.
PolyGhost recommends Qdos as its design does not require additional components to operate correctly. In combination with the polymer savings driven by enhanced process control, some of PolyGhost’s clients achieve payback in a matter of months.