Avoid Heat Input Into The Gas Vessel: Diaphragm Metering Pump Regulates Liquid Propane Injection Via Remote Pump Head
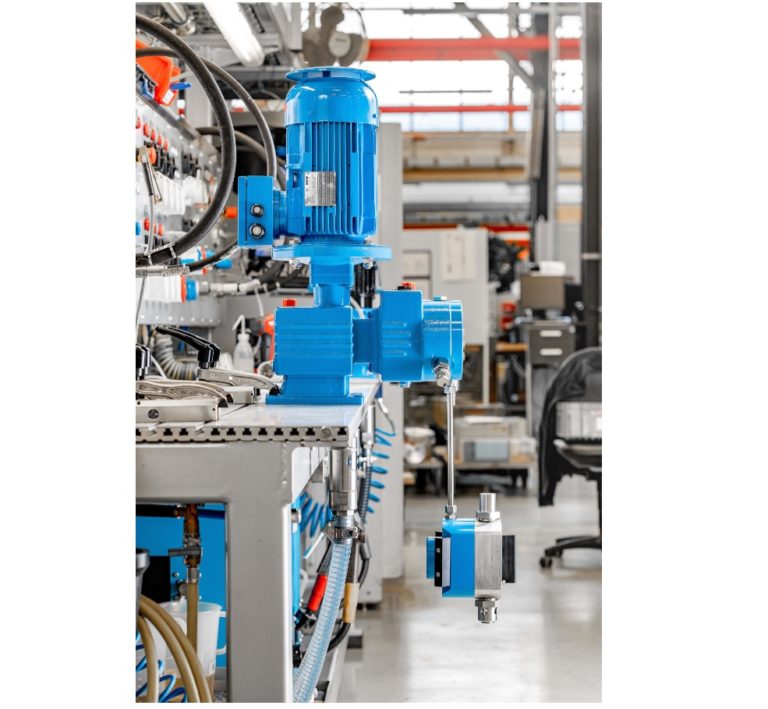
The Ecoflow variant used here is designed for 40 bar and can therefore deliver the propane to biomethane at sufficient pressure via the injection nozzles so that the gas mixture can be fed into long-distance networks. (Image source: LEWA GmbH)
For example, the Prolimix mixer system from Scharr Tec GmbH & Co. KG is used to do this. It can inject propane through several nozzles in liquid form and without energy-intensive evaporation. In the past, however, when the gas was fed in, there was backflow into the vessel. This was because common pump models were oversized, thus causing significant heat input in the tank due to the power loss of the motor. The rise in temperature in turn resulted in an increase in pressure, so that sometimes safety valves came on and interrupted the conditioning process. For this reason, Scharr Tec developed a concept which has now been successfully implemented in the industry for several years. Ecoflow diaphragm metering pumps from LEWA GmbH are used and mounted as remote solution. These custom-made products from the Leonberg pump experts make it possible to avoid the problem of heat input despite the increase in pressure caused by a driving head installed in the manhole shaft. At the same time, the pump is precisely matched to the required flow rate, so that there is neither backflow into the tank nor any power loss – all in the interest of energy efficiency. Since the pump is designed for 40 bar operating pressure, biomethane conditioning can also be carried out for long-distance networks without any problems.
"For conditioning biomethane, two things are usually necessary: propane gas to increase the calorific value and an evaporator with a mixer that enables the gas to be mixed with the methane," explained Christian Steger, engineer and owner of the engineering firm csplan. "At some point, however, we came up with the idea that the propane could also be injected in liquid form if the nozzle orifices were sufficiently small, as this would produce enough aerosols to ensure that the gases would mix." In cooperation with Scharr Tec GmbH & Co. KG, for which Steger was the managing director for over 32 years, the Prolimix was developed – a mixing plant for biomethane that uses a multi-nozzle technology to flexibly inject propane without needing to vaporize the gas first.
"Most pumps are oversized for injecting propane, since only a quantity of about 100 to 150 liters is required per hour and they often pump 50 liters per minute," said Steger. "The excess propane goes back through the circuit and into the vessel unused." The pump's power loss causes the temperature in the propane tank to rise because the pumps are designed as submersible pumps and the motor is located directly in the tank. To remedy the situation, Scharr Tec and csplan decided to cooperate with LEWA GmbH from Leonberg near Stuttgart. The pump expert can draw on extensive experience in the use of remote solutions and has successfully developed custom pump systems for OEMs for a long time, so that a solution could be found quickly.
Mass flow meter and control valve not required
After consulting the experts at LEWA, csplan decided to use the Ecoflow diaphragm metering pump with the M900 pump head. "This variant has the advantage of being protected against cracks by the double diaphragm on the one hand. On the other hand, the injection quantity can be corrected by an optional calorific value measurement in case of fluctuating biomethane qualities," explained Björn Pfizenmayer, Area Sales Manager at LEWA. "Because the pump installed in the vessel sluice regulates the inflow of propane itself, the mass flow meter and the control valve are no longer required either." The entire conditioning plant is more clearly arranged and less susceptible to faults. However, to solve the main problem of heat input into the propane vessel, the drive unit must be installed outside the tank.
Welded reciprocating line between pump head and drive unit
"The biggest challenge was to ensure a tight connection between the pump head and the drive unit," explained Pfizenmayer. "We wanted to install the propellant head in the manhole shaft and not in the propane vessel itself as part of a remote solution, in order to avoid heat input from the motor and thus the pressure increase." Initially, a connection via detachable hoses with a quick release coupling was considered. However, tests showed that gas bubbles from the tank migrated upwards through the reciprocating line, causing an interruption in propane production. Since a screwed reciprocating line also turned out to be leaky in the end, the company finally switched to a completely welded solution. The hydraulic line as a connecting piece between the pump head and the drive head only remained leak-proof with this variant, ensuring the reliable drive of the pump head in the tank. As a result, the problem of heat input was successfully circumvented and the pressure in the propane vessel remained permanently constant.
No power loss due to exact flow rate
Regardless of the remote solution, the integrated Ecoflow variant was precisely matched to the required propane quantity of 150 liters per hour. "Theoretically, this pump head can deliver up to 6,000 liters per hour," said Pfizenmayer. "However, as the special solution for Scharr Tec required a significantly lower quantity, we configured the pump with a low frequency of 20 to 140 strokes per minute." This prevented too much propane from being metered and power loss from occurring. The result was a reduction in the energy required and improvements in conditioning plant efficiency.
Injection with 40 bar possible
At the same time, this Ecoflow variant is designed for 40 bar and can therefore deliver the propane to the biomethane at sufficient pressure via the injection nozzles so that the gas mixture can be fed into long-distance networks as well. "This is particularly important because the high pressure means that it can also be fed directly into high-pressure natural gas networks," explained Steger. "And industrial consumers in particular, who are essential for biomethane producers due to their constant consumption, are usually connected to such higher-level high-pressure networks."
Since the Prolimix was installed in the biomethane plant with the LEWA pump as a central component, there have been no malfunctions: the mixer systems work without interruption. "The Ecoflow offers all the properties required for conditioning. It is precisely matched to the flow rate, provides the required gas pressure and, thanks to the remote design, does not transfer any heat to the propane tank," Steger said to sum it up. The experience gained from the project with Scharr Tec and csplan also benefited LEWA when the Ecoflow was used in other areas of application. "Propane is used as a refrigerant in the production of refrigeration appliances, for example, and must also be quickly introduced into the appliances in a precisely predefined quantity at a fixed pressure," explained Pfizenmayer. "Thanks to similar process specifications and conditions, we were able to draw on our know-how from the cooperation with Scharr Tec and csplan and offer the company a solution."
Source: LEWA GmbH