Atlas Copco WEDA Submersible Pumps Enable Critical Operations in Underground Swedish Mine
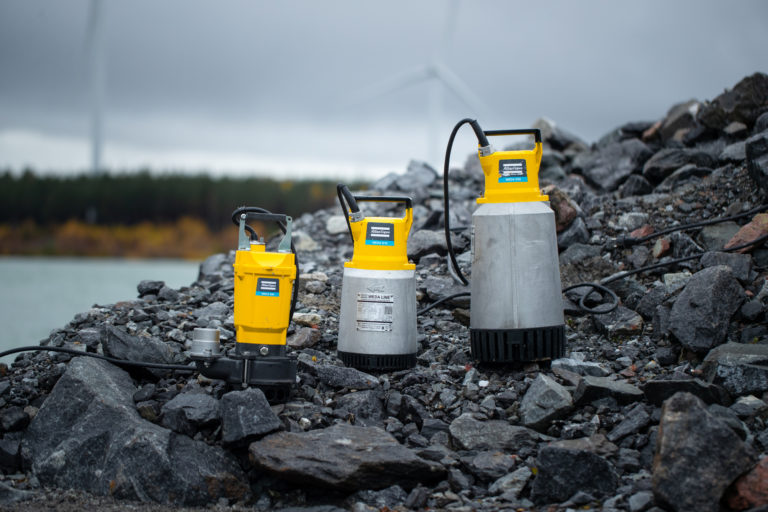
Zinkgruvan comprises a well-organised underground structure of tunnels and a processing plant, producing zinc, lead and copper concentrates. To ensure efficient and safe extraction of the ore, Atlas Copco WEDA submersible pumps deliver under extreme conditions to avoid flooding.
The mine operates all year round, 24 hours a day and seven days a week, which means three different shifts during a working day for its 460 employees. A halt on site would have a significant impact on its overall efficiency, resulting in significant costs for operators. The role of the dewatering pumps working underground is therefore critical to ensure the correct development of the extraction and to meet productivity targets. Zinkgruvan Mining has chosen Atlas Copco’s WEDA D line of electrical submersible pumps to conduct some of the most demanding dewatering operations.
Jan-Erik Mogren, who has been working at Zinkgruvan Mining for over 40 years and has been the Dewatering Pumps Service Supervisor for the last 10, explains: “We have different models of the WEDA D line working underground, up to 1,400 metres deep, because the pumps have proven to be very reliable in handling both clean and dirty water with small solids and particles. In harsh applications, common in the mining sector, these suspended solids can cause excessive abrasion and wear to the internal workings of the pump,” However, Mogren goes on to say that “WEDA pumps show good efficiency over time, which is of primary importance to ensure smooth operation at the Swedish mine.”
“It excites us to hear that our users value the effort we put into making the pumps more reliable and durable,” says Bart Duijvelaar, Product Marketing Manager, Submersible Pumps at Atlas Copco. “When we add new features, such as the patented Wear Deflector Technology, we must not lose sight of what makes these pumps manoeuvrable and practical at the job site. Also, having the pump controls and protection built right into the pumps, instead of in a separate control panel, simplifies transportation and handling, and prevents undue manipulation of the motor protection.”
Underground dewatering operations
At Zinkgruvan Mining, operators mine underground from several orebodies, and all extraction activities take place between 350 and 1,400 metres below the surface. The main level – where the offices, workshops and dining room are located – is found at a depth of 800 metres. The workforce has access to the different levels via elevator, which connects the underground workings with the surface. There is also a ramp system to grant complementary access to vehicles. In this labyrinth of tunnels, several Atlas Copco WEDA D pumps can be found working in a variety of situations.
Water is pumped down into the mine for use during drilling and for dust control during the extraction processes. Groundwater leaks through the walls, and it’s collected and pumped into water retainment ponds. To control the water level and avoid flooding, Zinkgruvan Mining has different WEDA D models – D10, D40, D50 and D60 – that are used depending on the volume of the pool.
When asked about underground dewatering operations, Jan-Erik Mogren said: “It is essential that the pumps are easy to work with and easy to service, and that they have maintained performance over time, so activity underground flows well and safely.” At Zinkgruvan Mining, productivity and the wellbeing of its people go hand in hand. “WEDA pumps have sustained efficiency, even in tough applications, and they are very light. That translates into better ergonomics for our people handling the pumps, which is something we value a lot.” concludes the Dewatering Pumps Service Supervisor.
“WEDA pumps offer a very good flow in relation to their low weight and power ratio,” explains Johan Magnusson, Sales Engineer at Atlas Copco. “This is one of the most appreciated features among our customers. For certain applications, it is essential that pumps are easy to transport and use. That, together with our support on-site, are two of the main reasons why the WEDA D line was chosen.”
Water is key in the extraction process
During the mining and extraction of the ores – copper ore and zinc-lead ore – and the subsequent treatment processes, water plays a major role. Ore is secondary crushed and ground in an autogenous grinding circuit. A bulk concentrate is initially produced from the ore before it is separated using a flotation process that involves water. The foam containing the mineral is collected, and then the water is removed using filters and returned to the process. What remains is three different fine-grained concentrates – zinc, lead and copper. Tailings are pumped approximately four kilometres to a dedicated impoundment, from which water is returned for reuse.
At Enemossen, Zingruvan Mining’s tailings storage facility (TSF), there is an area of sediment at the surface with water that has been used in the enrichment process – although most of the water involved in the process is pumped back into it or discharged. Due to the constant flow of water and sand to Enemossen, a WEDA D100 was installed with a floating raft to manage the water level of this large water volume. This particular model has been recently upgraded for improved performance and less power consumption in such applications, where the pump has to deal with sand-laden water.
Operations at Zinkgruvan Mining are supported by excellent logistics, where again, water is essential. In addition to the nearby highway access that connects the mine with Stockholm and Oslo, Lake Vänern, the largest in Sweden, provides access to coastal shipping via a series of inland canals and the port of Gothenburg.
Rising to the challenge
“It is never one factor alone that determines success. Good pumps need to be matched with good people,” says Duijvelaar. “We are very impressed with Zinkgruvan Mining and its expertise. With our support, they were able to deliver a sustainable solution for their dewatering needs. Our conviction that serviceability and repairability should be designed into the pump is reinforced by our customers recognizing our products for exactly that.”
Atlas Copco and Zinkgruvan Mining have worked together to address the increasingly complex dewatering operations of the mining industry. WEDA D pumps have been shown to be robust, reliably delivering in harsh environments such as tunnelling, construction and mining.
Source: Atlas Copco AB