Non-Seal Pumps with E-Monitor Enable Advanced Bearing Condition Monitoring
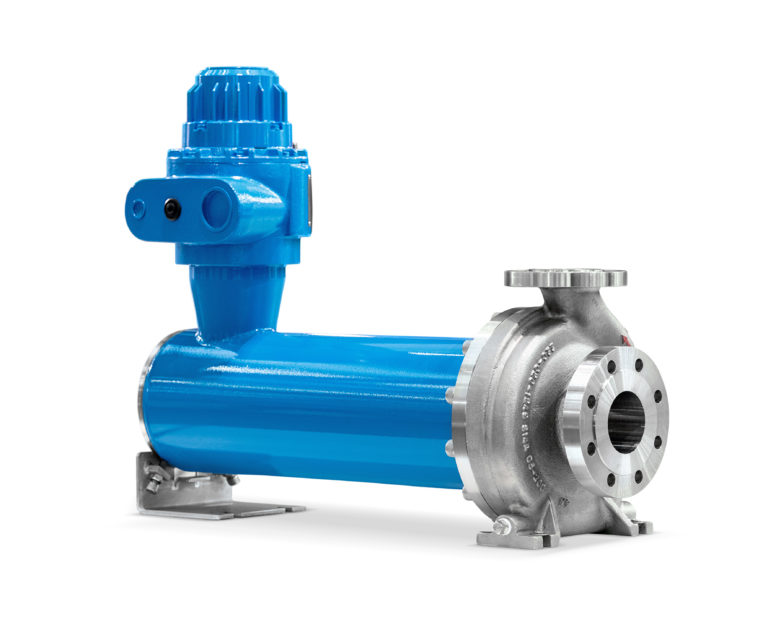
NIKKISO Non-Seal Iso. (Image source: LEWA)
To further improve their operational safety and reliability while carrying out these demanding tasks, all Non-Seal models are equipped with an E-monitor that indicates the wear condition of the slide bearings during pump operation, thus enabling predictive maintenance. The control unit is the most advanced monitoring system of its kind for pumps in high pressure and high temperature service.
Since the centrifugal canned motor pumps' rotor may move out of its original, operationally safe position due to bearing wear, sensors have been integrated into the stator to monitor the assembly's actual radial and axial positions in real time. As soon as the rotor is no longer correctly aligned, the sensors detect the deviations and indicate the condition of the bearing via a display with a traffic light system. A green LED indicates to the personnel that the pump is in good condition, while a yellow light signals that the pump should be continuously observed. If the LED lights up red, the pump must be shut down immediately. With the E-monitor, bearing wear can be detected at an early stage and the necessary maintenance can be better planned. To further optimize monitoring, the E-monitor can also be equipped with a remote function that includes a remote display of the bearing condition, including alerting and emergency shutdown. A further indicator on the display enables the pump's direction of rotation to be determined and corrected if necessary. This makes measurement of the phase rotation direction during commissioning superfluous.
Source: LEWA GmbH