Repair of decommissioned turbine saves time and money for pulp manufacturer
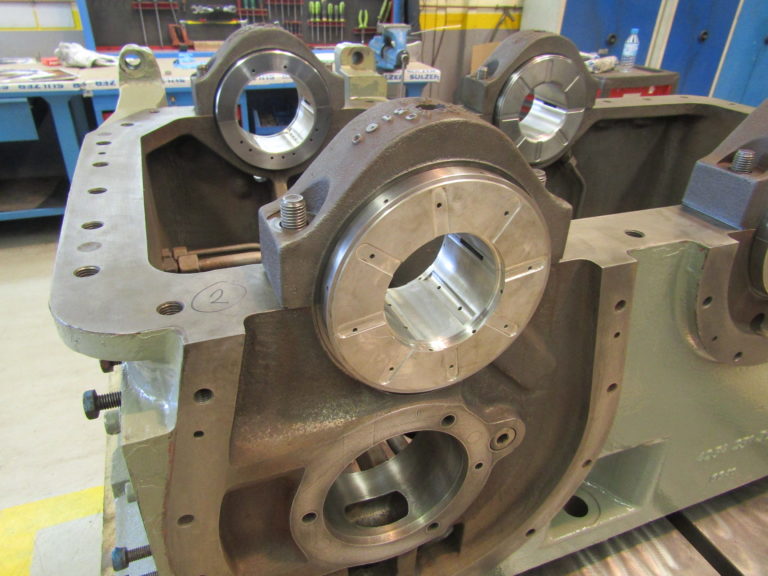
New white metal bearings were reverse engineered for an exact fit (Image Source: Sulzer)
Replacing broken equipment can be a more cost-effective solution where the cost of a new product is cheaper than repairing the original, providing the component is available on a short lead time. However, in heavy industry, when important assets may need replacing, the time to manufacture and deliver the new product may be months or even years. Specialist repairs can often breathe new life into damaged equipment and minimize downtime as well.
Steam power
In the pulp and paper industry it is common for steam turbines to be used to power electrical generators that supply large parts of the production process. To generate the steam, pumps supply water to the boilers continuously, ensuring the plant continues to operate efficiently. In many cases these plants operate emergency back-up systems where a smaller turbine can be used to power the main boiler feed pumps allowing the boiler to cool down without damage if the main turbine suffers a failure.
For one pulp plant in Spain, the failure of the emergency steam turbine required a quick repair to get it back online as soon as possible. The first call was to the OEM, which reported the unit as being beyond repair, so the second call was to Sulzer, the independent maintenance specialist, and the phoenix project was initiated.
Álvaro Ayuso Barrios, Head of Rotating Equipment Services in Spain for Sulzer, explains: “The pulp manufacturer had a close relationship with Sulzer; several pumps on the site were maintained by the local Sulzer service center. In addition, Sulzer had previously delivered another steam turbine repair for this customer so there was already confidence in Sulzer’s ability to complete a turbine repair.”
Damage assessment
The damage to the steam turbine was so extensive that the OEM saw the only option as replacement with a new turbine, a project that would have a lead time in excess of 12 months. Both the price and the timeframe exceeded the expectations of the management at the pulp factory.
Sulzer was invited to inspect the damage and concluded that using its expertise and extensive facilities, a repair could be achieved, saving the customer both time and money. Sulzer made a competitive tender for the repair and was successful in winning the contract.
The assessment of the turbine showed extensive damage, which appeared to have been initiated by water getting into the lubrication oil. This had led to a breakdown of the white metal bearings and the failure of the labyrinth seals. This in turn caused a significant axial displacement of the primary and secondary shafts, which led the turbine blades to contact the casing.
Repair solutions
In fact, further investigation showed a deep crack in the casing, but the manufacture of a new casing would have added considerable time to the project. Sulzer’s solution was to repair the cracked section and machine it to match the internal dimensions of the casing. Non-destructive testing (NDT) was carried out on the repaired section to prove the quality of the repair.
The white metal bearings were reverse engineered to create 3D drawings and manufactured for an exact fit without the need for OEM assistance. Scoring on the shaft was resolved by adding material using a metal spraying process before machining the shaft back to the original OEM specifications.
The most challenging part of the project was manufacturing more than 500 new turbine blades. Once again, reverse engineering techniques were used to establish the precise dimensions and create a set of 3D drawings for the manufacture of the turbine blades. The new parts were created using a combination of electro-discharge machining (EDM) and conventional machining. Throughout the repair, the customer was regularly updated on the progress of the repairs.
Commissioning support
The service center staff reassembled the steam turbine and assisted with the installation and commissioning at the pulp manufacturer. In fact, the hydraulic control circuit required several alterations to achieve the correct settings, after which the turbine started successfully.
Álvaro concludes: “This project was both complex and rewarding. We have managed to breathe new life into a steam turbine that had been written off by the manufacturer and surpass the expectations of our customer. All the resources for this repair have been managed by the Algete Service Center, which has exemplified its capabilities in delivering a challenging project.”
Source: Sulzer Ltd.