New Dry Screw Vacuum Pump for Harsh Industrial Processes from Leybold
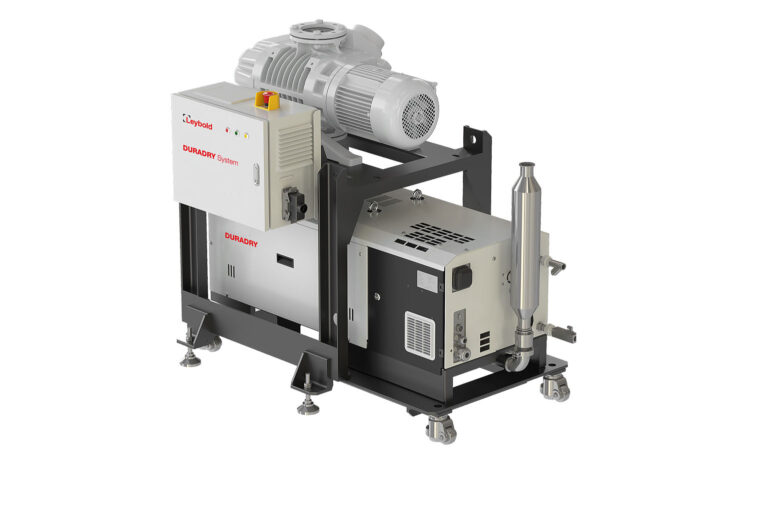
DURADRY System – Industrial Style: The vacuum supplier rounds out its new series with a powerful DURADRY that’s available as an option with a full or partial housing unit. (Image source: Leybold GmbH)
"The pump’s main advantages are its ease of operation and low maintenance requirements," observes Leybold Product Manager Darong Li, highlighting the strengths of the two models in the160 and 250 m³/h pump speed classes (a 450 size is also coming soon). The vacuum supplier rounds out its new series with a powerful DURADRY that’s available as an option with a full or partial housing unit.
Low power consumption and superior durability
“User friendliness, reliability and outstanding vacuum performance are all high on the list of requirements for targeted industrial sectors," explains Product Manager Darong Li. To achieve this, the new DURADRY models have a slim external design. The developers have also focused on an advanced rotor design and variable speed control (VSD). The speed control prevents wasted energy and ensures a high level of durability to withstand even the most demanding processes. Through the use of a Smart Drive, users can monitor critical parameters such as rotor speeds and temperatures, allowing for continuous operation.
Quiet, ergonomic operation
"The DURADRY’s superior efficiency is due to an improved heat regulation and dust absorption capacity of the screw pump," continues Product Manager Darong Li. However, its robust design has proven to be particularly advantageous in relevant processes. Equipped with sensors and a dynamic seal, the hermetically-tight system prevents the introduction of oil particles and contamination. Additionally the DURADRY impresses customers with its quiet, ergonomic operation. Noise and vibration levels in the vicinity of the vacuum pump are less than 64 dB. Thanks to its plug-and-play design, both models also offer various setup options and are intuitive and easy to operate.
Powerful, cost-effective DURADRY system
In addition to its DURADRY models, Leybold also offers a high-performance system with intelligent control options for maximum operational reliability in the applications mentioned. This innovative solution combines efficiency with superior dust particle tolerance. "Through these attributes, this package offers an attractively-priced option for demanding applications where optimized thermal management is also required. In addition to its robust design and long runtimes, customers benefit from a system with intelligent control options and real-time preventive maintenance functions – including filter and oil change warnings as well as temperature alarms," observes Product Manager Stephen Liu, explaining the features in more detail. Various optional fieldbus controls and HMI-PLC integration make the connectivity and control of the DURADRY system intuitively simple. The package is available in a paired-down industrial version or in an electronic housing. For comparison, the industrial version requires approximately 30 % less floor space than the electronic version with an integrated HMI interface that's specially designed to meet the stringent environmental requirements of the electrical industry.
Important features of the DURADRY system at a glance
- Intelligent communication with C4.0 control system
- Adjustable pump speed (250 - 4.100 m³/h)
- Temperature and flow sensors for greater safety
- Longer operating times through preventive maintenance
- Lower resource requirements
- Available in ‘industrial’ and ‘electronic’ versions.
Source: Leybold GmbH