Sulzer completa la reparación de la bomba de agua de refrigeración en solo siete semanas
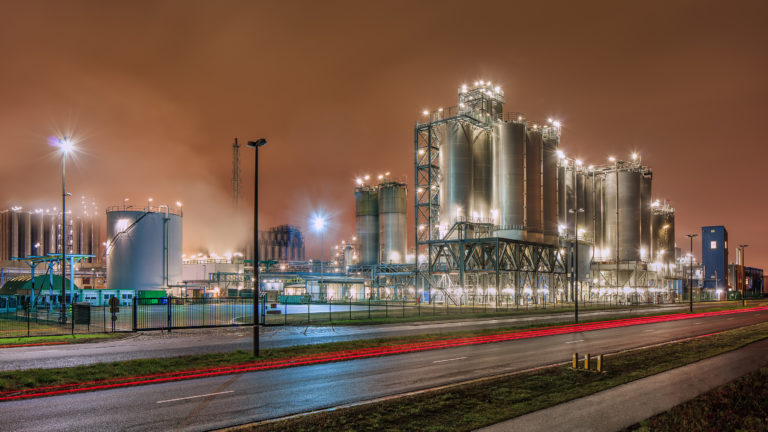
El proyecto se completó en solo siete semanas, evitando pérdidas de producción (Fuente de la imagen: Shutterstock - TonyV3112)
Los equipos de generación de energía son esenciales para reducir los costos operativos de una planta química, que es responsable de crear muchos productos cotidianos, como combustibles, aceites y plásticos. Seguir un programa de mantenimiento planificado mejora la confiabilidad y reduce el tiempo de inactividad, todo lo cual ayuda a reducir los gastos generales de operación y entregar productos rentables al consumidor.
Circunstancias desafiantes
La falla de un activo de bombeo puede tener implicaciones importantes para las grandes operaciones industriales integradas. Para los propietarios de una planta química belga, los problemas con una bomba significaban que la planta corría el riesgo de perder su principal fuente de energía eléctrica y vapor.
Los problemas afectaron a la planta de energía en el sitio de la planta química, administrada como una empresa conjunta entre el propietario y un importante proveedor de energía europeo. La planta integrada suministra a la planta química tanto electricidad como vapor de proceso en una disposición que es a la vez eficiente y rentable.
Recientemente, sin embargo, los operadores de la central eléctrica enfrentaron una situación preocupante causada por la falla de una bomba en el sistema de agua de enfriamiento de la planta. Dos bombas de entrada verticales que suministran agua de refrigeración a la planta habían estado en funcionamiento durante muchos años, y el diseño redundante significaba que una sola falla normalmente permitiría que la operación continuara ininterrumpida hasta el próximo cierre programado. Cuando la segunda bomba comenzó a mostrar altos niveles de vibración, y aún faltaban meses para la próxima parada de mantenimiento planificada, los operadores supieron que era hora de llamar a la experiencia de Sulzer.
Primera solución
Los ingenieros de la planta de energía en el lugar retiraron la bomba rota de 8 metros de largo y la enviaron al centro de servicio local de Sulzer en la cercana Kapellen. Una vez allí, los expertos en servicio de Sulzer desmantelaron la unidad para evaluar su estado. La inspección inicial reveló rápidamente que el eje de la bomba estaba doblado e inutilizable. Peor aún, la curva había provocado que el impulsor abierto hiciera contacto con la carcasa de la bomba, dañando ambos.
Para evaluar completamente la tarea de reparar la unidad, el equipo de Sulzer necesitaba comparar los componentes dañados con una plantilla original. Debido a su antigüedad, la única información de diseño disponible para las bombas eran dibujos en 2D. Para actualizar esa información, el equipo utilizó la información bidimensional para construir modelos de diseño asistido por computadora (CAD) en 3D de los componentes originales. Luego, compararon esos modelos con escaneos láser creados a partir de la bomba rota.
El análisis fue una noticia mixta para el equipo. Demostró que ambas partes requerían reemplazo, pero si bien el impulsor estaba inutilizable, la carcasa podría proporcionar un período de servicio adicional.
En estrecho diálogo con el cliente, el equipo acordó un enfoque de dos etapas para solucionar el problema. Con carácter de urgencia, fabricarían un eje y un impulsor nuevos, luego instalarían esos componentes en la carcasa original para permitir que la bomba reanudara sus funciones de respaldo en la planta. Posteriormente, fabricarían una nueva carcasa que podría instalarse durante el próximo cierre programado.
Velocidad y calidad
Utilizando el nuevo modelo CAD, los expertos en fabricación de Sulzer en Bruchsal, Alemania, mecanizaron con CNC un patrón para el impulsor de 650 mm de diámetro, lo que les permitió fundir y luego mecanizar la compleja geometría de la nueva pieza. En situaciones en las que la velocidad es tan importante, los especialistas de Sulzer se benefician de la estrecha red interna de expertos de la empresa en toda Europa para encontrar la mejor solución posible.
El nuevo impulsor se envió a Bélgica, donde el equipo de Kapellen lo montó y lo equilibró en un nuevo eje. Las piezas de repuesto se instalaron en la carcasa original y, después de la prueba, la bomba reparada se devolvió a la planta y se colocó en su lugar.
“Para un trabajo de esta escala y complejidad, el tiempo de entrega normal es de alrededor de seis meses”, explica Ben Lauwerijssen, gerente regional de ventas de Sulzer. “En este caso, sabíamos que nuestro cliente estaba extremadamente preocupado por la posibilidad de pérdida de producción. Gracias a la estrecha colaboración entre diferentes equipos dentro de Sulzer y con los ingenieros de mantenimiento de nuestros clientes, pudimos completar todo el proyecto en siete semanas, sin pérdida de producción ".
Con la nueva solución instalada, el personal de operaciones y mantenimiento de la planta pudo centrar su atención en asegurar la confiabilidad a largo plazo del sistema de agua de enfriamiento. La instalación de la nueva carcasa ya está planificada para la próxima parada programada, al igual que una revisión de la segunda bomba. Los especialistas de Sulzer también están trabajando con el cliente para implementar una nueva tecnología de monitoreo de condición, así como una estrategia de mantenimiento mejorada para las bombas.
Fuente: Sulzer Pumpen (Deutschland) GmbH