Water Flinger Adopted by Pump Manufacturer
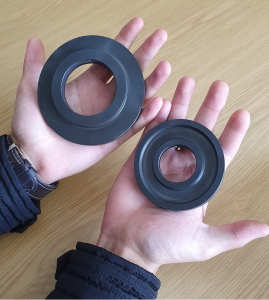
Two of the different water flingers that have been produced (Image source: Vesconite Bearings)
The manufacturer found that its horizontal centrifugal pumps, as a result of high pressure, had a problem of water escaping from the gland packing - the material that should form a watertight seal around the shaft.
This resulted in dirty water being sprayed on to the non-drive-end bearing assembly and, in turn, resulted in seizure, failure, and a high maintenance and down-time cost to replace the bearing assembly. “The manufacturer designed a water flinger (deflector) solution that would attach to the release collar on the shaft,” describes Vesconite Bearings technical sales consultant Phillip de Villiers. “This would mean that excess water from the gland packing would be deflected with the rotation of the shaft,” he says.
However, the initial solution employed a phenolic laminated material, which was found to absorb water and delaminate. To eliminate these problems the company then called on De Villiers, who suggested Vesconite as an alternative material that would not swell or delaminate and had the added advantage of being suitable in dirty environments because of its excellent wear-resistant properties. “Samples were produced and tested and, proving successful, the manufacturer ordered water flingers of various designs for its different pump sizes,” reports De Villiers. “The whole process from sample production to first order took three months,” he says.
The pump manufacturer intends to use Vesconite water flingers in all of its pumps, which are used in a variety of applications. It is active in a multitude of African countries, including South Africa, Zimbabwe and in the DRC, in which some of the first Vesconite water flingers will be installed in a dewatering pump in a mine.
Source: Vesconite Bearings