Vesconite Deflector Protects Pump Value
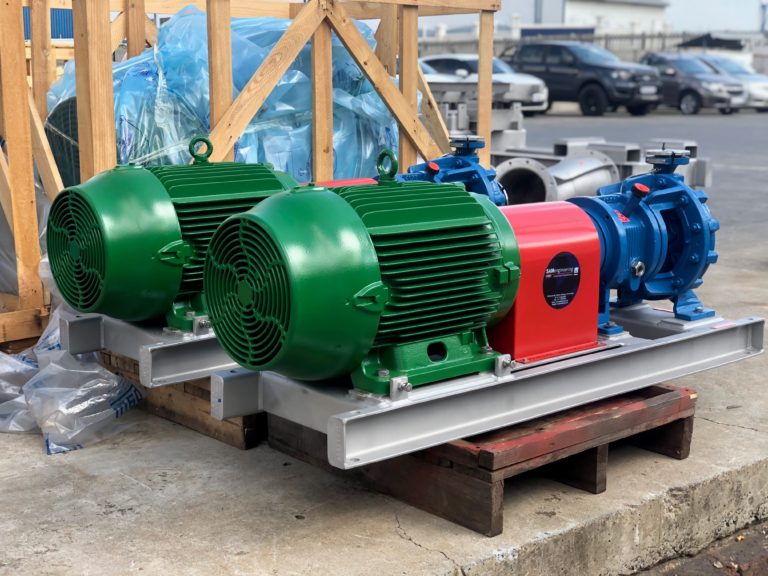
The type of pump used by the starch and glucose producer, which experienced substantial maintenance, component and capital-cost savings when it fitted Vesconite wear-resistant deflectors to its centrifugal pumps. (Image source: Vesconite Bearings)
Deflectors are cylindrical rings placed at either end of the bearing assembly around the shaft. In this application, they fit at the end of oil lip seals to prevent the ingress of water and dust.
The producer had previously not used deflectors but in the food environment, in which the pumps are hosed down as part of hygiene practises, it was noted that the life of bearings could be improved with deflectors being installed.
Pump solutions provider SAM Engineering proposed deflectors and a cost-effective material that would protect the bearing assembly against dust and water was sought for. On most (sites/ process plants), fitting of deflectors are generally overlooked, as lip seals serve the purpose of retaining lubricant in the bearing housing and prevent water and dust ingress; however, installing deflectors provided added protection.
SAM Engineering reports that the Vesconite deflector is likely to improve the life of bearings and decrease the likelihood of mechanical seal replacement and, most importantly, protect the bearing assembly, the cost of which can be considerable.
The bearing assembly totals 30% of the cost of this chemical-process pump, so the Vesconite deflectors could be said to protect 30% of pump value, the pump solution company states.
Source: Vesconite Bearings