Valve Island for the New Siemens Peripheral System
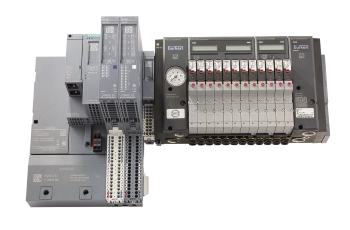
The latest generation of the valve island Type 8647 AirLINE SP from Bürkert is compatible with the distributed peripheral system SIMATIC ET 200SP HA from Siemens. (Image source: Bürkert Fluid Control Systems)
The latest generation of the valve island Type 8647 AirLINE SP is now also seamlessly integrated into the new distributed peripheral system SIMATIC ET 200SP HA (High Availability) from Siemens, i.e. combined in a compact, high-performance automation system. The new integration stage further increases plant availability. Now, for the first time, valve islands in highly available and up to R1 redundant PROFINET environments can be operated directly in a distributed peripheral system.
Process reliability in the plant
The flexible valve island was developed for plants that need to run 24 hours a day, 7 days a week and 365 days a year with the highest demands on availability and reliability. Together with the Siemens modules, it can be mounted as a space-saving solution in a control cabinet. The highly scalable design makes it possible to adapt the control cabinet layout exactly to the actual requirements. The direct connection to the Siemens peripheral system guarantees not only fast and seamless integration during start-up, but also correct monitoring during subsequent plant operation. Thanks to complete software integration in the Siemens process control system PCS 7, all diagnostic information and process parameters of the valve island can be monitored. This allows preventive and wear-oriented plant maintenance to be initiated and downtime to be minimised.
Redundant PROFINET interfaces ensure the plant continues to operate even if a communication participant fails. The up to 64 hot-swap capable valves per island, which can be exchanged during operation without system downtime or influencing the adjacent valves, also contribute to the high availability of the entire plant. Check valves in the vent duct are an additional safety function. They prevent valves from being accidentally enabled by pressure peaks in the vent duct, thus eliminating media mixing. The new Type 8647 AirLINE SP meets all the requirements of modern, safe and highly available automation systems thanks to its ability to also integrate fail-safe pneumatic signals quickly and easily into the valve islands.
Source: Bürkert GmbH & Co. KG