Testing of Process Pumps Also In Compliance with API 675
The investment of around € 500,000 in a new pump test bench enables ProMinent to ensure product quality and undertake further development - even in the highest performance ranges - and test performance profiles adapted to specific applications and customer specifications according to the state of the art.
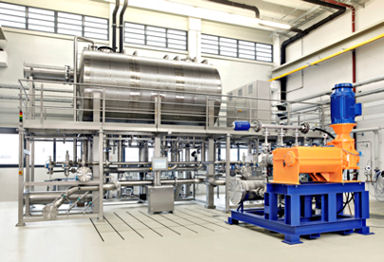
The process metering pump TriPower MF is tested on the new pump test bench to comply with API 675 guidelines (Image: ProMinent)
ProMinent can now also test pumps to meet API 675 guidelines (American Petrol Institute guidelines for oscillating displacement pumps for use in the crude oil, chemical and gas industries), thereby ensuring that process safety is guaranteed when metering and handling flammable, toxic, solids-laden or highly viscous fluids.
The new test bench for process pumps became operational in Heidelberg at the start of 2011. Manufactured throughout from stainless steel 1.4301, the test bench comprises two independently operated test stations, each of which is equipped with a centralised power supply, monitoring equipment and a supply to the test bay. A computer integrated in a console controls and parametrises the individual components of the test bench, enabling the test bench to be operated centrally. All of the requisite parameters inputted are monitored, analysed and documented by an operating data collection system.
Process pump performance ranges
All process pumps with a motor capacity of 0.37 to 90 kW with 400V and 5.5 to 160 kW with 690V can undergo variable performance tests. A hydraulic line is supplied to the test pieces for this purpose and, depending on the type of pump and any customer-specific requirements, the pumps transport a certain volume of water against a back pressure that can be set by the operator. The measuring range for the flow ranges from 20 l/h to 90,000 l/h and the measured value has an accuracy of 0.1% right across the given range. This is guaranteed by the use of high-precision Coriolis flow meters.
Metering medium: water of the highest quality
An exceptional feature of the new test bench is the metering medium used: ultra-high quality water, treated in an environmentally-friendly way according to the state of the art and permanently monitored. A made-to-measure water treatment plant, designed and manufactured in ProMaqua s in-house plant engineering department, guarantees that the pumps to be tested are fed with a medium with a high degree of purity.
Water treatment
The top-up water is treated by reverse osmosis and is post-treated with ultra-low conductivity to generate permeate (demineralised water), thereby complying with the limit values for chloride and eliminating contamination by deposits of lime.
During operation, the water in the test circuit is continuously filtered during the test and the differential pressure is monitored to ensure that contamination can be identified at an early stage, allowing any contamination that occurs to be reliably removed. The water is then disinfected and cleaned using ozone, thereby helping to protect the test bench against possible contamination. The water quality is continuously monitored by measuring the conductivity, pH value, redox potential and turbidity and the pH value is automatically regulated. The water quality and all relevant operating parameters are documented throughout the entire test procedure.
The water is stored in a 30,000 litre stainless steel tank positioned above the test bays and is cooled externally with pillow plates to ensure a constant water temperature.
Summary
The new process pump test bench from ProMinent is designed to comply with the state of the art. Data is automatically generated for each pump being tested and specific test documents are produced.
Complex water treatment processes developed by ProMaqua ensure a constant quality of water - the basis for reliable test results.
The test bench means that pumps can undergo performance testing with high-precision accuracy at maximum volume and maximum operating pressure. Additional tests, such as pressure testing, performance characteristic lines and tests to comply with API 675 can be offered to customers, depending on their requirements, and a high level of flexibility can be ensured, thanks to the option of parallel testing.
Source: ProMinent GmbH