Sulzer water injection pump brought back to life to maintain productivity after seven years lying dormant
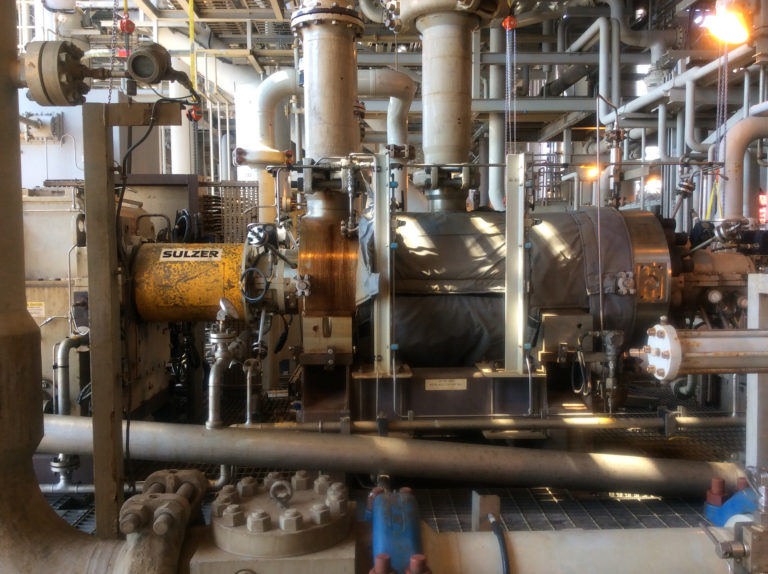
The water injection pump rejuvenated by experts from Sulzer. (Image source: Sulzer Ltd.)
For one offshore platform in the Gulf of Mexico, calling the original equipment manufacturer (OEM) was the deciding factor in getting a water injection pump in this situation back up and running in time to start operating when it was needed.
We all feel the effects of fluctuating global oil prices; it is, however, still a highly competitive market and profitability for the producers is dependent on the efficiency with which oil is extracted. By optimizing process and maintenance schedules, oil companies aim to prolong the viability of wells by operating cost efficiently, but this gets harder out at sea.
Offshore drilling rigs aim to maintain peak performance throughout their production life cycle. One of the crucial pieces of equipment in this process is the water injection pump, which is used to pressurize the well and maximize production rates. It is therefore important to carry out periodic maintenance of these key assets to ensure they continue to perform reliably. All is not lost if the maintenance schedule is somewhat overlooked, as shown in a recent project that involved Sulzer revitalizing one of its injection pumps that had remained dormant for seven years.
Borrowed parts
The history of what exactly happened prior to the need for recommissioning this standby water injection pump had been lost during various changes in personnel working on the platform. From what information could be gathered, it appeared that of the two water injection pumps on the rig, #2, developed a leak in a Graylock fitting in a piping spool, downstream of the pump itself.
To resolve this issue, pump #1 was shut down and the necessary parts removed to keep #2 operational. Since that time, pump #1 had remained out of service, without any preservation actions - while pump #2 operated continuously. However, after seven years use, it had begun to drop in efficiency, to the point that the platform operator needed to overhaul the pump to ensure continued productivity.
To achieve the overhaul of pump #2 it was necessary to assess the condition of pump #1, resolve any issues and return it to normal operation. This would enable pump #2 to be shut down and overhauled, without an interruption to the productivity of the platform.
Call the experts
Both of the pumps were designed and manufactured by Sulzer who, as the OEM, was the first port of call for the platform operator. Realizing the importance of delivering a rapid response, an offshore-qualified pump engineer was dispatched to the Gulf of Mexico, where he completed the initial inspection of pump #1.
Working in the tight confines of an oil platform takes experience and close cooperation with the other personnel. Mark Lindsley, Field Service Engineer for Sulzer, explains: “We work closely with the platform staff to ensure that every project is completed safely and to the highest standards.”
Considering the harsh marine atmosphere that surrounds the injection pump equipment, most of the components looked to be in excellent condition. The comprehensive inspection process highlighted all the areas needing attention, much of which could be completed during the initial visit.
Following the inspection, Mark rebuilt the pump thrust bearing and the non-drive end (NDE) radial bearing was replaced using stock that was held on the platform. The gearbox had been cleaned out previously and the lube system flushed in preparation for reassembly when the alignment of the drive train was checked and adjusted.
The most obvious issue was the missing piping spool, which would have to be manufactured before the drive train could be recommissioned. In addition, the inspection found that the motor to gearbox coupling would need to be rebuilt, the almost 6’000 kW (7’500 hp) electric motor would need to be tested and an additional shim would be needed for the gearbox to pump coupling.
Back to life
Following a very successful initial visit, Sulzer engineers set out to assemble a new pipe spool and the parts required to rebuild the coupling. When all the necessary parts were available, Sulzer returned to the platform to complete the installation work.
The charge pump was cleaned, aligned and coupled, allowing the water injection pump to be started. Once online, the pump performed with very low vibration levels and the operator agreed that it should continue to operate while being monitored.
Mark Lindsley continues: “The whole process has involved close collaboration with the customer, providing onsite support as well as on-shore engineering expertise. Sulzer has OEM engineering capabilities to manufacture high-quality new parts while its worldwide service center network delivers local onsite expertise.”
Reducing costs
The successful start-up of pump #1 has enabled the platform to start planning the refurbishment of pump #2. Continued operation will prove the reliability of the repaired pump and ensure optimum production levels of the well are maintained. As the OEM, Sulzer has discussed the future needs of the platform and together with the customer, it is making plans for the refurbishment of pump #2.
Sulzer’s combination of expertise in the oil and gas sector, professional pump engineering and global service center network is helping to keep oil platforms efficient.
Source: Sulzer Ltd.