Sulzer Uses Laser Metal Deposition to Repair Lean Amine Pump Impeller for Equinor
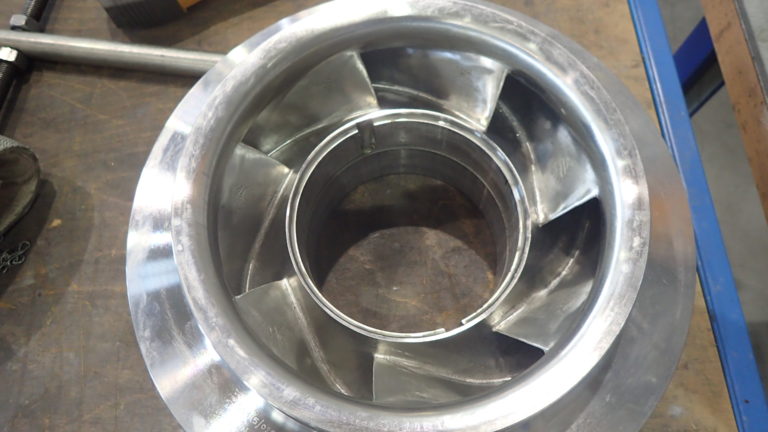
The completed impeller ready to be shipped back to Norway. (Image source: Sulzer Pumpen (Deutschland) GmbH )
A planned repair project saw Sulzer deliver two refurbished pumps with hand-crafted impellers to ensure as-new performance and reliability.
Modern life is surrounded by products that are derived from oil and gas, but the raw materials need to be refined and purified to make them suitable for energy and manufacturing processes. Lean amine is used to absorb hydrogen sulfide (H2S) and carbon dioxide (CO2) constituents from sour natural gas, creating rich amine, which is circulated to a regeneration unit where it returns to lean amine. The whole process is driven by a high-pressure pump, an important asset on the platform.
Improving performance
For the leading international energy company, Equinor, the goal is to ensure continued efficiency and reliability of its offshore platforms through planned maintenance and engineering improvement. The amine process uses four API 610 - BB5 pumps that produce 1’120 m3/hr (4’930 gal/min) flowrate at 978 m (3’200 ft) head and a pressure of 150 barg (2’175 psi), all of which requires 3.85 MW (5’160 hp) of power.
As part of a routine maintenance project, one cartridge was removed and sent to Sulzer’s service center in Norway for inspection of internal components and renewal of wearing parts. Due to the nature of the application, the lean amine contains gas in saturation, entrained gases and with limited suction pressure to the pump, it wasn’t a surprise to discover cavitation damage on the suction impeller.
Weighing up the alternatives
The options for the impeller were to either repair it or to replace it with a new component, but the latter option would have a longer lead time. In parallel, Equinor and Sulzer had been in discussion about additive manufacturing (AM) technologies and this naturally lead on to a request to repair the impeller using AM, rather than waiting for a replacement to be manufactured.
In this case, the impeller was sent to Sulzer’s Leeds Service Center in the UK where specialist facilities would deliver the most cost-effective repair. The damaged vanes could have been re-profiled, but this would mean removing material from the impeller, rather than replacing it, and since the cavitation was expected to continue, the durability of the impeller would be compromised.
The impeller was manufactured from Super Duplex stainless steel, which has two phases, austenite and ferrite, and the balance of these two needs to be maintained to ensure the continued performance of the material. However, it is not very tolerant of heat and welding can cause this balance to shift from 50:50 to 30:70 in favor of ferrite, which will seriously affect the corrosion resistance.
In addition, excessive heat can cause distortion of the metal, so this eliminated tungsten inert gas (TIG) welding from the list of options. Sulzer suggested laser metal deposition (LMD) as the most suitable solution to return the impeller to its original dimensions.
Keeping cool
During the original manufacturing process, the inlets and vane profiles of the impeller were detailed by hand using templates. Sulzer has fully-automated LMD equipment, but in this case the most appropriate solution was to replicate the original manufacturing process.
Dr. Yogiraj Pardhi, Additive Manufacturing and Materials Specialist for Sulzer comments: “Careful selection of consumable, control parameters and technique enables the best method to be established. In this case, for greater flexibility and access, a semi-automated process was selected using a manual wire feed and automated control of the laser head across the area being repaired. In between each pass of the LMD head, a cooling period was required to ensure the temperature of the repair site did not exceed 100 °C (212 °F).”
Once the damaged areas had been built up, a process of manual blending using abrasive hand tools and templates was employed to establish the final dimensions of the vanes. Again, using the same methods as the original manufacturing process and minimizing any heat build-up ensured the original properties of the impeller were retained. The finished impeller was checked for any flaws using dye penetrant inspection (DPI) before being balanced and prepared for shipment back to Norway in time for the cartridge rebuild.
Long-term reliability
The impeller repair was completed in Leeds within two weeks, while repairs to the rest of the cartridge were completed in Norway. The two-week schedule coincided with the rest of the repair project and ensured the whole pump was returned to the customer on time.
Having completed the repair to the first pump, a sister unit was also removed, found to have very similar cavitation damage and was also sent to the service center in Norway for the same repairs. In Leeds, where the process had already been detailed, the repair time for the impeller was shortened to just one week.
A representative at Equinor comments: “Having established that cavitation is a feature of this application, we have decided to take a proactive approach to maintenance to ensure continued performance and reliability in the assets on our offshore platforms. Working with Sulzer has ensured a timely repair that returns the amine pumps to their original specifications, improving durability without the expense of downtime.”
Source: Sulzer Pumpen (Deutschland) GmbH