Sulzer: Twelve Pumps for Chinese Refinery
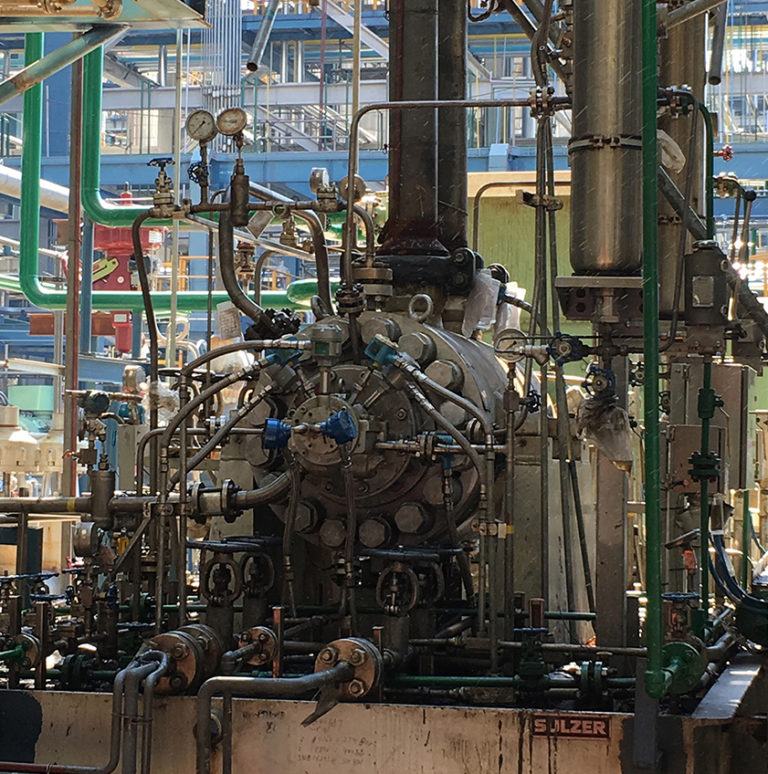
CP feed pump for the ebullated bed residue hydrocracking application (Image source: Sulzer, Ltd.)
Sulzer’s ability to bring the new models into production quickly allowed its customer to meet tight project timelines, as well as demanding technical and commercial goals.
Market demand for fuel and products derived from oil and gas is being met by expanded exploration and the use of new technologies to maximize the potential of existing wells. The introduction of new technology is improving efficiency for the petrochemical sector, which in turn helps to reduce the cost of everyday items, from recycling bins to toothbrushes and the tires on your car.
China’s hydrocarbon processing industry is the largest, and fastest growing, in the world. To meet demand and maintain competitiveness, companies across the sector are continually investing in new capacity and advanced technologies. For one refinery, that included a major project to upgrade and optimize its facilities.
Challenging start
In 2016, the refinery took the decision to introduce new equipment across its plant, including a new ebullated bed hydroprocessing system using H-OilRC technology from a French process licensor. This system is designed to add value in the refining process by extracting valuable hydrocarbon products from heavy feedstock residues, which may contain high levels of solids and other contaminants.
When it came to the selection of pumps for the new system, the refinery was aware that the nature of the various feedstocks created demanding operating conditions. The internal components can be exposed to high levels of wear and there is a significant potential for flow to be disrupted by large solid particles.
The refinery knew that it was possible to obtain pumps designed specifically to perform well in these conditions, but it was unable to find a local source of supply. Using equipment manufactured in China wherever possible is an important part of the refinery’s procurement strategy, as it seeks to localize supply chain and ensure ease of maintenance and support.
Global expertise, local presence
That’s where Sulzer was able to help. As a global pump specialist, Sulzer already had a significant presence in China, producing pumps in the Dalian factory since 1999, and at a second plant in Suzhou since 2010. Sulzer also has a long-standing relationship with the parent company of the refinery, supplying and supporting pumps at many of its facilities in the country. After discussing the requirements, oil and gas industry experts at Sulzer recommended two proven technologies from the company’s extensive portfolio. Just as importantly, they also agreed to manufacture the critical pumps in China.
Like any major facility upgrade project, the ebullated bed system was planned to a tight schedule. So once the agreement was in place, Sulzer moved quickly to bring the new products to life in its China plants.
Maximum performance, maximum durability
The first of those products was the CP multistage barrel pump designed to API 610 type BB5 specifications. The Sulzer CP design incorporates an axial-split volute casing, which is less susceptible to wear than alternative designs when a high level of abrasive solids are present.
Sulzer’s design and manufacturing specialists in China worked closely with their colleagues from the USA, who hold the design responsibility for the CP, to allow for some important design modifications. This particular application required a low flow, high head, high speed solution, so Sulzer had to pay special attention to the surface characteristics of the fluid channels within the pump in order to minimize losses and achieve the target performance.
Problems crushed
The second key technology was a solution to the problem of pump performance impairment by large solid particles. For applications like these, Sulzer has developed a range of pumps with a special “coke crusher” unit at the pump inlet stage. This technology uses a rugged, bladed rotor that will break up solids to ensure they pass smoothly through the rest of the pump. Sulzer in China worked with colleagues in Germany and the US to integrate the coke crusher technology into two pump types for the project: the BBT, an API 610 type BB2 centrifugal pump, and the ZF, an API 610 type OH2 centrifugal pump.
Delivering under pressure
In addition to building up the necessary in-house manufacturing processes, Sulzer in China also had to qualify suitable local suppliers for key components of the new pumps. The company’s expert sourcing teams conducted detailed supplier audits to ensure that each one met Sulzer’s exacting global quality standards, especially when it came to critical parts such as the inner casing of the CP pump and the coke crusher components for the BBT and ZF units.
During the development and manufacturing process, representatives from the refinery made regular visits to Sulzer’s plants, giving them the confidence that work was proceeding on schedule and to the highest quality level. They were also present to see all the new pumps successfully meet their performance specifications in testing. In total, 12 of the newly localized pump models were delivered to the customer: three CP units, six BBT units with the coke crusher installed, and three coke crusher-equipped ZF units.
“This project was an important next step for our partnership with the refinery and for our support of China’s petrochemical sector as a whole,” says Zhang Jianfeng, Managing Director of Sulzer’s Suzhou manufacturing facility. “We have demonstrated that we can provide our customers with all the benefits of local manufacturing combined with Sulzer’s excellence in technology, quality and reliability.”
Source: Sulzer Ltd.