Sulzer Pumps Are Helping Farmers Keep Yields up and Power Bills down
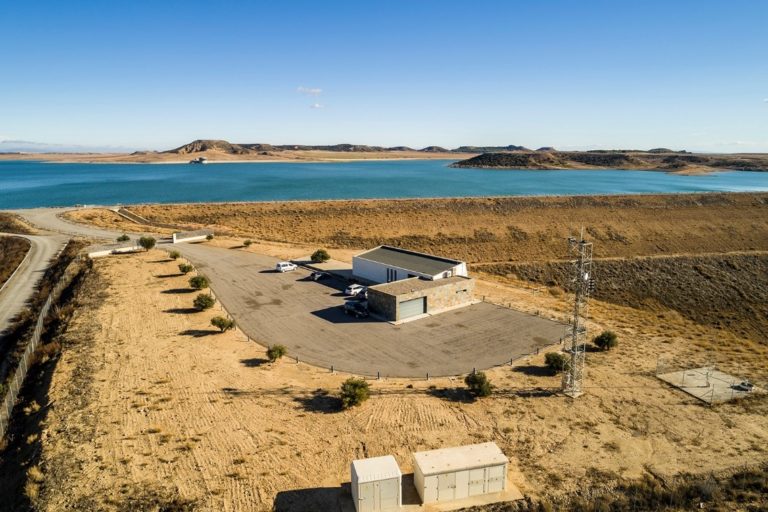
For the owners of the San Salavador reservoir project, operational efficiency was the top priority to ensure that annual running costs were kept to a minimum. (Image source: Sulzer Ltd.)
However, large irrigation schemes often require big pumps, driving up energy costs and increasing agriculture-related carbon emissions. Both new and existing installations can benefit from engineering expertise to ensure pumping systems deliver optimum performance and minimized running costs.
Water is fundamental to farm yields. In Australia, for example, farmers applied 7.8 million megaliters of water to crops and pasture during the 2020 to 2021 financial year, a 37% percent increase on the previous year1. That jump was the result of increased availability of irrigation water, as the country enjoyed high levels of rainfall following three exceptionally dry years.
Understanding the costs
It is easy to underestimate the cost of ownership when designing an irrigation scheme, especially when energy costs rise more quickly than expected. The upfront investment in capital equipment needs to be carefully calculated, and some owners may be tempted to push for savings at this point. This can lead to increased operational costs down the line, however, in the form of frequent breakdowns and high energy costs.
Today, the agriculture sector is becoming more aware of the through-life implications of its equipment choices. That awareness is being driven by multiple factors, including higher energy costs, challenges in the recruitment and retention of staff, and pressure to reduce the environmental impact of farming operations.
Increasingly, irrigation projects are being designed and installed by dedicated engineering firms that understand lifecycle costs, commissioned by farming businesses that appreciate the impact of operating expenses on their margins. That has led to a move within the market to high quality products that offer greater reliability and energy efficiency. The increase in initial investment needed to purchase such products is quickly recovered through operating cost savings.
Savings on the grapevine
This is exemplified by a major irrigation company based in New South Wales, Australia, which was approached by a customer in the wine sector wanting to improve the efficiency and reliability of its irrigation systems. The company and its engineering consultants analyzed the pump stations, pipes, filtration, mainlines and valves, looking for the most efficient, reliable way to deliver the approximated 256 liters per second that the vineyards required.
That analysis revealed that combining two pumping stations, reducing the number of pumps from three to one and connecting the farms with new mainlines was the optimal approach. However, this relied on sourcing a highly efficient pump that could meet the duty requirement.
After assessing the available options, the company selected a Sulzer axial split case pump, which could meet the site’s requirements with 87.1% overall efficiency - a 3-5% improvement over competitors. The robust construction of the Sulzer pump was another key factor. Irrigation water often contains abrasive particles, which can cause premature wear to key components such as the impeller. To ensure that efficiency was matched by reliability, a duplex stainless steel impeller was specified to ensure long-term durability. Combined with additional filtration systems this would reduce downtime so that the vineyards could properly capitalize on the energy savings.
Plain savings in Spain
In Northeast Spain, the designers of a very large irrigation scheme also called on Sulzer’s expertise to maximize efficiency. From the outset, the owners of the San Salavador reservoir project were very clear that operational efficiency was the top priority to ensure that annual running costs were kept to a minimum. Sulzer entered a competitive tender for the project with a proposal that would later be shown to offer between 15% and 50% improvement, depending on the conditions, on the running costs of a rival bid.
This benefit was supplemented by the proposal from Sulzer to work in partnership with the customer and offer its considerable expertise in pumping solutions. Rather than just delivering pumps that could deliver the necessary water flows, Sulzer prepared a comprehensive solution that included all the control infrastructure as well as all the maintenance equipment.
Sulzer proposed some of its latest pumps equipped with premium efficiency, IE3, PE7 motors that would make an excellent starting point for an energy efficient installation, together with a design for siphon-effect discharge pipework that would improve the performance of the pumps by reducing the static head.
Integration matters
In the examples above, and in any other large scale irrigation project, an integrated, engineering-led approach to equipment specification is key. Optimal efficiency and reliability depend upon pumps, pipework and other system elements that are designed to work together. For new projects, pump manufacturers are always willing to share performance curves and other data, allowing designers to make appropriate decisions about the design of the sump and pipework. If new pumps are required to replace worn out equipment in existing installations, pump specialists like Sulzer can tailor a pump to the existing infrastructure to deliver the most efficient solution.
1www.abs.gov.au/statistics/industry/agriculture/water-use-australian-farms/latest-release
Source: Sulzer Ltd.