Sulzer: New pumps paid off in two years
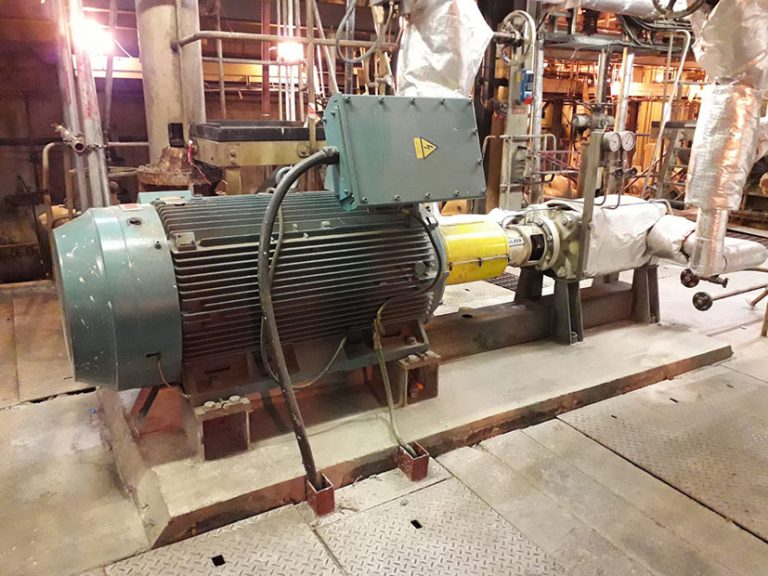
The new boiler feed pumps were installed with minimal disruption to plant operations. (Image source: Sulzer Ltd.)
Power generation plants rely on boiler feed pumps to deliver a reliable and consistent flow of water to the boilers, which create the steam that powers the turbine, which creates electricity. After 45 years in service the boiler feed pumps needed to be replaced and Sulzer managed to achieve an impressive return on investment of just over two years.
Reducing the amount of waste that goes into landfill is an important environmental consideration and one that is being supported by waste-to-energy plants, which use the material to create electricity. These plants help to increase sustainable energy production and they are supported by Sulzer, which offers many products and services that can improve efficiency and reliability.
Rising maintenance costs
A major UK waste-to-energy plant was experiencing considerable reliability issues with its six boiler feed pumps. Routine maintenance involved a complete refurbishment every two years and the costs for this work were increasing. Sulzer only became involved after one of its turbine specialists was discussing current issues with the maintenance manager.
Dale Jarvis, Business Development Engineer with Sulzer, explains: “I had been working with this plant for some time, providing support for the steam turbine, and during one visit the discussion turned to the boiler feed pumps. Knowing that Sulzer has considerable expertise in boiler feed pumps, I invited one of my colleagues to visit the plant and see what we could offer.”
The plant has six boiler feed pumps that have been operating since the site was commissioned over 45 years ago. Over the years, the pumps have been regularly maintained, but more recently, they have required major refurbishments to keep them operational.
Turnkey solution
As a pump manufacturer and independent service provider, Sulzer was well-placed to deliver a turnkey solution that would include the removal of the legacy equipment and the installation and commissioning of new pumps. Having established the specifications of the old pumps, it was possible to source new pumps that would exactly match the original performance characteristics of the old pumps but with improved efficiency.
Sulzer’s proposal was to replace two pumps each year, allowing the plant to spread the cost of the project and also appreciate the benefits of the new pumps before committing to the next stage of the installation. The financial benefits were obvious from the outset. The cost of each new pump was only marginally more than the refurbishment costs of the equipment it replaced, giving a return on investment of just over two years.
Dale continues: “Our site services team only needed ten days on site to remove the old pump, modify the pipework slightly and install the new equipment. This ensured that the plant always had sufficient capacity and no downtime was associated with the project. After the first two pumps were installed, the plant manager decided to continue with the project and four pumps have now been replaced. The installation of the remaining two will take place next year.”
Tailored performance
Sulzer has so far installed four of its MBN50 high pressure 9-stage pumps, which are primarily designed for power generation applications and provide efficient and reliable service in this demanding environment. The performance of each pump has been tailored to the application to ensure optimum efficiency and reliability.
Dales concludes: “The plant manager has immediately seen the benefits of the new pumps. The annual running costs have dropped dramatically, and the maintenance team is now able to spend more time looking after other important equipment. The whole project has been completed on time without any disruption to the operation of the plant and is on target for completion next year.”
Source: Sulzer Ltd.