Qdos Pumps Used Extensively for Polymer Dosing in Wastewater Treatment
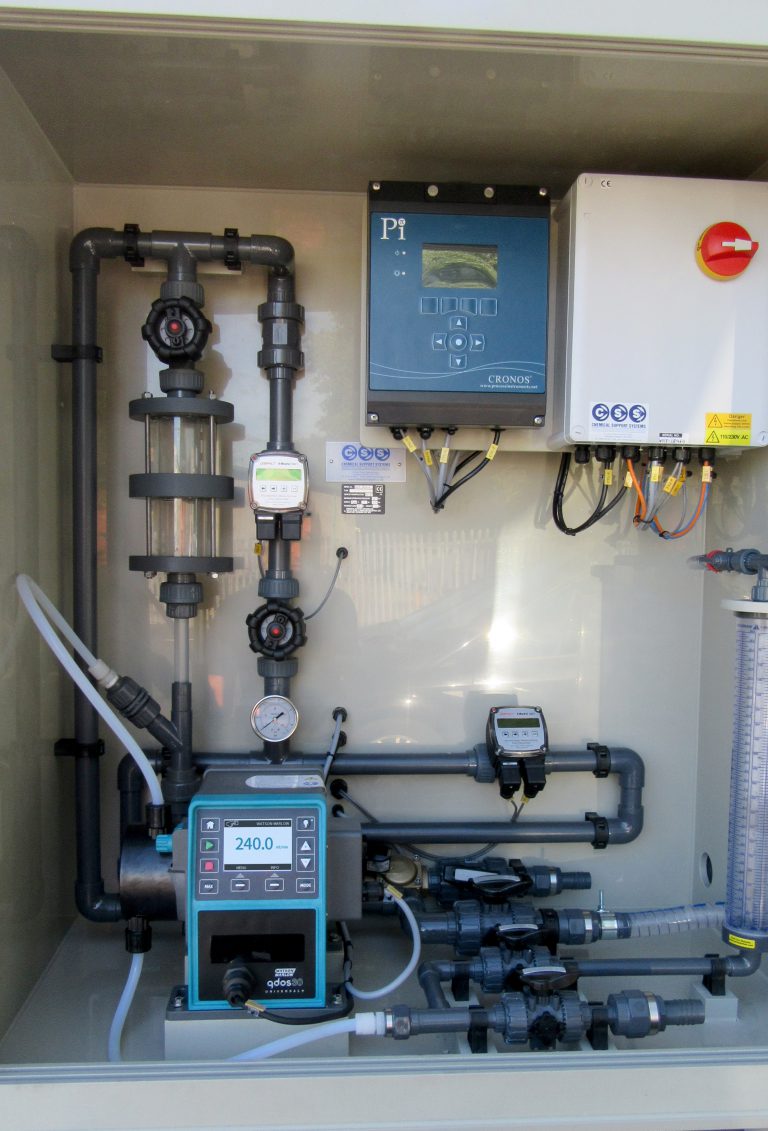
Image source: Watson-Marlow Fluid Technology Group
Moving forward, this usage looks likely to increase as more effort is made to reduce the presence of phosphorus wastewater, which remains the most common cause of Water Framework Directive (WFD) quality failure in the UK.
CSS has been established for 30 years as a Cheshire, UK-based electrical and mechanical engineering company. Although the company undertakes work in most areas of engineering, its specialist knowledge and expertise is as a major supplier of chemical dosing equipment across a variety of industries, including water treatment.
The phosphorus issue
The UK water industry has a major issue: over half of its river water bodies and three quarters of its lakes exceed the phosphorus discharge consent level of 0.1 mgP/l for “good environmental status”. To help combat phosphorus levels, a chemical coagulant or polymer is typically dosed into wastewater. The amount of dosing depends on the amount of phosphorus present, with potential fines for those found guilty of discharges outside of limits.
In the USA and Canada, for example, fines can be up to $500,000. With this thought in mind, paying a little more for a pump that can provide the necessary accuracy and confidence to do the job correctly, seems small hardship.
Ian Bishop, one of the three co-owners at CSS, says: “Companies with wastewater streams are trying to achieve increasingly stringent discharge consent limits, but also want to reduce operational wastewater treatment costs. Our chemical dosing systems, many of which rely on Qdos pumps, help companies achieve both these things.”
Qdos pumps cut chemical costs through higher accuracy metering. In addition, these innovative pumps offer linear and repeatable low-pulse flow rates from 0.1 to 2,000 ml/min (up to 7 bar) under varying process conditions. Further benefits include simple drop-in installation that reduces the need for ancillary equipment, while maintenance is limited to single, no-tools component replacement.
Influential factors
“When supplying a chemical dosing system to a customer, there are certain qualities we look for in a dosing pump,” says Mr Bishop. “We use Qdos pumps predominantly for their reliability, intuitive operation, accurate dosing and ease of maintenance. If chemicals are particularly viscous, such as polymers, we find Qdos pumps even more useful. In our experience, using conventional diaphragm pumps for dosing high-viscosity polymers can be problematic due to blockages within the suction and discharge valves. The benefit for customers of specifying Qdos pumps is a reduction in the level of maintenance required by not having to clean and flush the associated pump head and valves on a periodic basis.”
In terms of control, for most of the water treatment systems supplied by CSS, signals are provided by the end user/site, which are generally from a key part of the process, to turn the Qdos pump on or off in conjunction with the process or vary the chemical demand accordingly.
Petroleum-based polymers
With certain water treatment tasks demanding the use of petroleum-based polymers, WMFTG has recently introduced its Qdos ReNu PU pumphead and tubing material. The use of polyurethane makes it resistant to petroleum distillates and other aliphatic hydrocarbons.
“This tubing material has proved very reliable for specific polymer solutions containing petroleum distillates,” confirms Mr Bishop.
Chemical containment upon pumphead failure is also assured with Qdos pumps; an important point as cleaning up polymer spillages can be very time-consuming.