Pump Solutions for Mine Water Management
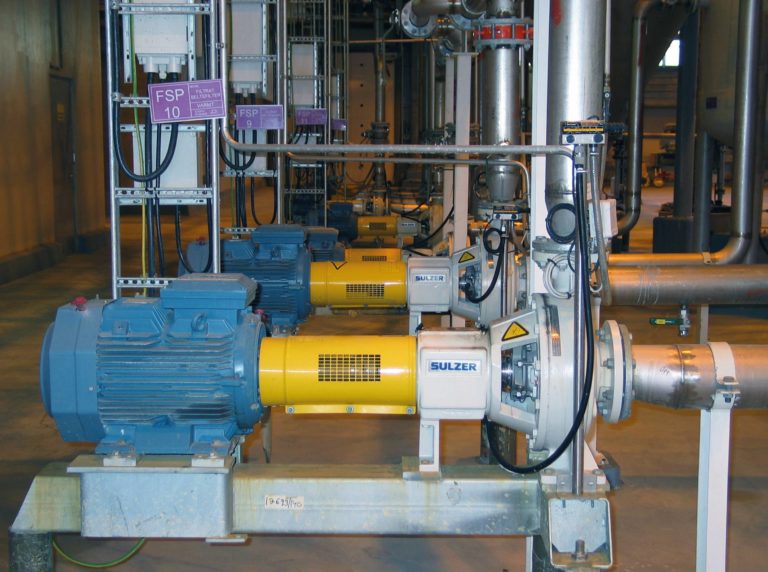
Pump solutions for mine water management. (Image source: Sulzer)
Pumps are, therefore, one of the most used machines in mines today. ln this article we will review the concepts of mine water and mine water management as well as the most common pumping applications.
Mine water and mine water management
The definition of mine water is that it is not a slurry, i.e. generally it is considered to contain <50 g/1 of solids. Mine water can be categorized in two different streams:
- Removal of water from the mine area (mine dewatering) and removal of water from the process (process dewatering). Mine water originates from several sources. Precipitation from rainwater and subsequent floodwater or melting snow generally affects above-ground mining, whereas underground mines are affected by subterranean waterways, ore bodies containing pockets of water, or long-term rise of the water table from precipitation. Water that is removed from a mine to gain or facilitate access to an ore body is known as mine water.
- Conversely, minerals processing requires the addition of water at various stages, and this can either be reclaimed water from within the mine area or, where not sufficiently available, brought in from external sources such as town water, river or sea water.
The management of water around the mine site is referred to as mine water management. Managing the water resources is a critical task and a major challenge in mining. lt is a never ending process, and dewatering operations would normally continue even when a mine is operating at reduced capacity or temporarily shut down.
Keeping the outflow of mine water higher than the inflow is imperative to enable the mining of the mineral deposit. Consequently, large quantities of water may have to be pumped continuously during the operation and maintenance of the mine working areas.
Mining companies are facing increasing pressure to control depleting resources and manage the environmental impact of operations in compliance with stringent legislation. The importance of well-designed and well-maintained mine water management cannot be stressed enough. lt plays a critical role in the mining industry today.
Challenges in mine dewatering
Mine operations are harsh environments. Mine water can range from dirty water to water containing mud, clay, grit, stones, etc., creating the need to handle an abrasive and sometimes corrosive product.
lt is important for the mine planning department to have an accurate estimate of the groundwater inflow so that the most technologies used are multi-stage deep well pumping or well suitable method for dewatering the mine can be designed. Whilst the mine area requires water removal, this may be scarce commodity in other parts of the site. The overall water management design criteria may therefore include the installation of a water treatment plant to enable the recycling of water for reuse
To determine the most suitable dewatering method for a specific type of mine, the following challenges and conditions need to be considered:
- Mine type: This generally determines the best dewatering method but may be overruled by end user preferences.
- Location: Mines in remote locations may have reduced access to adequate electrical power. Therefore, alternate technologies need to be considered.
- lncoming volume of water: lt is of critical importance to have an accurate estimate of the inflow from all possible sources.
- Mine depth: Whether an open pit or underground, the mine depth will determine whether single-lift drainage or a stage pumping system needs to be employed.
- Water properties: These will determine the dewatering system, pump technologies and construction materials. The type of pumps utilized depends on various factors, including water quality, chemical composition and solids content.
- Life of mine: lf the expected mine life is long, a more permanent system needs to be considered. ln a mine with a shorter life span, portable products or a less costly dewatering system can be used.
- Cost budget: The budget available for the dewatering system defines which methods can be considered
Water streams
Mine dewatering
There are two main types of mine dewatering, i.e. active and reactive (or passive). Active dewatering is a process used mainly around open-pit mines with the purpose of lowering the water table. This method reduces ingress and seepage of water into the mine areas, allowing safe and uninterrupted work. The technologies used are multi-stage deep well pumping or well pointing.
Reactive dewatering is used to remove water from working areas and is applicable to both open-pit and underground mines. Typical reactive applications in open-pit mines are pit dewatering, seepage water removal and flood water relief, while typical applications in underground mines are face dewatering, stage pumping, drainage of shaft bottom sump, ramp and stope pumping and main mine dewatering. Multiple pump tech- nologies can be used in these applications, including submersible, vertical, end-suction, multistage or volumetric pumps. The pump type and construction materials depend on various factors, such as water properties, the presence of abrasive solids, the concentration of solids and the location of the installation.
Process dewatering
Process dewatering generally refers to the separation of water from solids towards the later part of minerals processing. Slurry pumps are normally utilized for pumping the process water to various types of filters or into thickening and settlement tanks.
Process water and treatment
Large quantities of water may be required in minerals processing. The quality of the water is highly important and therefore some level of treatment is needed before it enters the process. A combination of vertical, horizontal and submersible pumps may be used in the treatment process. The materials of construction will depend on the water source, e.g. sea water, reclaimed water, etc. The treated water is then added to the process at various stages.
lntake water
Because intake water stations may transport water into the mine from various types of sources, the technology requirements will vary accordingly. Vertical turbines and horizontal end-suction pumps are most commonly used, depending on the pump station design and configuration.
Reclaimed water
The scarcity and cost of water means that reclaiming and reuse are on the increase. Water is reclaimed from tailings ponds, lagoons and the downstream of minerals processing by vertical, horizontal and submersible pumps. lt is then treated prior to use.
Whilst water may be a nuisance, it is also essential for the mining process. The management of this precious resource is of critical importance.
Sulzer in mine water management
Sulzer offers a comprehensive portfolio of innovative pumps and agitators for mining applications, from lightweight and robust submersible dewatering pumps to wear-resistant high-lift centrifugal pumps for the removal of sludge, mud, silt, and water in abrasive and corrosive environments. With thousands of installations around the world, Sulzer's products and services have stood the test of time.
Source: Sulzer Ltd.