Pump Solution Trends Evolving to Meet Challenging Times
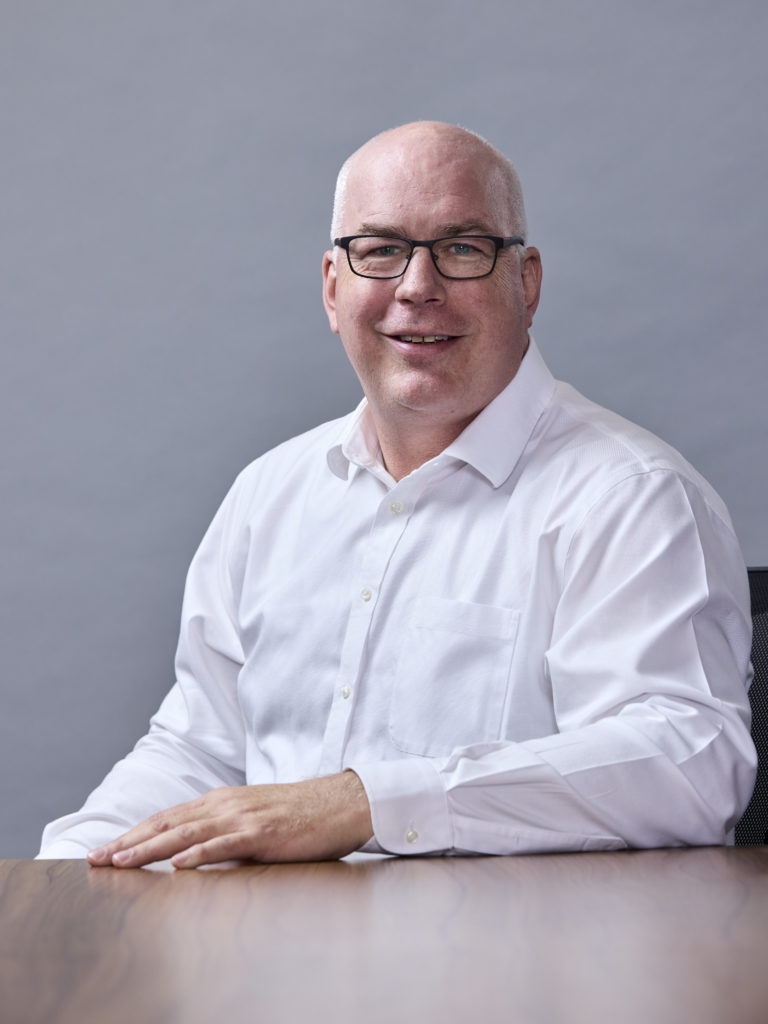
Joe Keenan - Global Managing Director Industrial Fluid Flow Solutions at RMI Pressure Systems (Image source: RMI Pressure Systems)
“In most parts of the world, the economic mood is uncertain, and project champions are less tolerant of delays and budget over-runs,” said Keenan. “Pump solutions partners are expected to sharpen their pencils and offer solid value-adds with their offerings.”
Building secure supply chains
Severe supply chain disruption, which began with the Covid-19 pandemic, has continued with the conflict in Russia and Ukraine, and more recently in the Red Sea region. In many cases, this is leading original equipment manufacturers (OEMs) to draw non-traditional suppliers into their supply chains.
“While this can add to supply chain complexity, it is among a range of strategies to keep production and delivery timelines stable, and to reduce turn-around times,” he explained. “Certainly, in the high-pressure pump segment, customers look to us to help iron out supply chain fluctuations as far as possible.”
Localisation, predictability and size
He added that the geopolitical instability, with its resulting supply chain and cost management challenges, has driven OEM manufacturers towards localisation to mitigate the potential of disruption for long lead items.
“Customers are prioritising predictability of fulfilment as a value driver during the procurement process,” he said, “as delays drive up their costs and impact their project delivery.”
Given the lower margins that have generally resulted from current global economic conditions, pump markets are looking for high levels of system quality to underpin operational performance and reliability. This procurement foundation must ideally stretch into the future, giving users an asset that pays its way through optimal uptime and long-life.
Keenan also noted that pump technology and engineering development have resulted in larger pumps with increased outputs – as larger pumps reduce the number of units required to meet customers’ fluid needs.
“This reduces the overall maintenance cost and improves the efficiency of the systems,” he said. “The pressing need for end-users to manage lifecycle costs drives OEMs to invest in continuous improvement.”
System solutions
This links to another key trend: a growing preference for system solutions rather than ‘loose pumps’.
“In recent years, we have tended to receive very few requests for stand-alone pumps,” he said. “Rather, customers prefer to procure a system that delivers a certain pressure and flow for their specific industrial or mining application.”
Indeed, the expectation is increasingly that the OEM’s functional system will be quickly commissioned and regularly maintained by the OEM – at least for the first year or two. Thereafter, there is growing interest in longer term service contracts to ensure that the solution continues to operate optimally.
Sustainability from quality
“When you combine the high pressure pump equipment longevity requirement with the growing focus on sustainability, it translates into demand for efficiency in the short term, and minimised waste in the longer term,” he said. “Where mechanical solutions can be refurbished instead of replaced, for instance, this contributes positively to customers’ triple bottom line accounting.”
Quality assets last longer and save on capex, he noted, while there is less needed to dispose early of large equipment components which are resource-heavy and energy-intensive to manufacture. As an indicator of this quality, customers are looking more closely at the standard and extended warranties that OEMs offer – as they work towards a more sustainable supply chain.
Customers are also paying more attention to the sustainability performance of OEMs themselves – not just their offerings. Companies like RMI have installed solar energy facilities on their manufacturing sites, for instance, and the carbon impact of these initiatives is being well documented so that customers can record and benefit from these carbon reductions in their own supply chain reporting.
Skills gap
Another important factor behind pump system reliability is the global skills landscape. Keenan pointed out that a significant portion of a workplace generation had their retirement hastened by the Covid-19 pandemic, leaving gaps in many companies’ trade skills and in-house maintenance and repair expertise.
“This has occurred at a time when digital and other technologies are increasingly being incorporated into high pressure pumping solutions – creating demand for both new and cross-disciplinary skill-sets,” he said. “More of the highly technical aspects of equipment customisation and maintenance are therefore falling to the OEM, allowing the customer the benefit of outsourcing these requirements.”
Responding proactively to these conditions, leading companies in the pump sector have positioned themselves as employers of choice, to retain and nurture skilled employees for decades rather than years. Skills development through in-house mentorship and training in technical or trade skills is also being embraced as a vital strategy for success.
Optimisation
“Customers will come to us for the expertise required to optimise their systems after installation, and to work with them to ensure that our solution continues to serve their needs as their own technology evolves,” Keenan explained.
In the steel sector, for example, this interaction drives the trend towards ‘blue’ and ‘green’ steel, as part of corporate decarbonisation strategies. Shifts such as the move away from coking coal and towards electric arc furnaces require considerable changes in process. These shifts are driven by the end-user, but pump solutions OEMs like RMI are actively supporting progress in this direction.
“As technologies optimise over time, aspects such as control systems are constantly innovating,” he said. “OEMs are focused on attracting and retaining controls engineers – still a scarce skill – so that they can offer leading-edge improvements as customers adopt or engineer new methodologies.”
Variable speed
Controls have become central to the sustainability drive in the pump solutions field, not just for energy conservation but also to prevent the wastage of water. Variable speed drives have been revolutionary in their control of pumps’ energy consumption and prevent the traditional over-pumping that leads to water leaks and wastage. This helps companies save on the costs of power and maintenance while striving to meet environmental goals; there can even be reductions in noise emissions.
“A packaged descaling solution in a steel plant can therefore be implemented as a system, complete with the latest controls that optimise performance while improving energy and water efficiency,” he said.
In closing, he noted that OEMs like RMI also value the opportunity of working with engineering, procurement and construction contractors in forging innovative solutions for end-customers.
“Especially when we work together early on in the project life-cycle, we can positively influence their designs by demonstrating the technology opportunities we have developed,” he said. “They will often have a requirement or solution that we can take a step further, to the benefit of all the project’s stakeholders.”
Source: RMI Pressure Systems Ltd