New WMFTS Webinar Advances in Low Maintenance Chemical Dosing
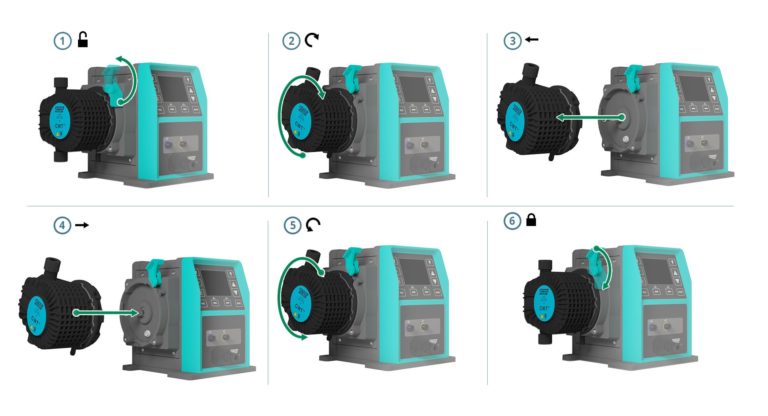
Safe and simple pump head replacement with a Qdos pump. (Image source: Watson Marlow Fluid Technology Solutions)
What is the dream scenario for a water treatment plant operator? There can be little doubt that it is a facility running reliably, with no disruptions and without requiring any attention.
As was explored in a new WMFTS webinar on advances in low maintenance chemical dosing, time is an asset, and constrained budgets mean there are fewer people available to respond to breakdowns and maintenance issues. Some water and wastewater treatment plants run without any permanent staff on site at all.
These challenges are exacerbated by an ageing workforce and the loss of skilled technical personnel leaving a huge gap for utilities and industry to fill. This means that when equipment is not working properly, it can cause a major headache and expense, with staff pulled away from other responsibilities or having to travel to remote sites.
Tightening regulations
Meanwhile, expectations are rising, with regulatory standards tightening and the risk of fines and reputational damage if public health or environmental stewardship is compromised. The ultimate risk to original equipment manufacturers is that they lose out on future business.
This was confirmed during the webinar, with Cory Sonner, sales engineer at US specialist water and wastewater manufacturing firm Vessco saying, “When an operator is no longer able to feed the chemicals, they are not feeding their system properly, which may put them out of regulatory requirements, or having to pull staff from regular responsibility to service these pumps.”
The most common causes of chemical dosing pump failure, requiring technical intervention, include poor suction conditions and loss of prime. Lack of turndown and chemical compatibility also plays its part.
When such vital equipment is not working properly, it can mean impurities that can damage components enter the system, potentially degrading the whole process and adding extra cost. Mitigating equipment failure should be non-negotiable at any site, and disruptions can be minimised at the point investment decisions are being made and pump equipment selected.
Reliable equipment
The operator’s dream is for equipment with reliability designed in, where less maintenance is required day-on-day, month-on-month and year-on-year. Watson-Marlow has identified pumphead tube replacement as a major weakness in dosing pump design, which is also a major consumer of operator time.
Most chemical dosing pumps need regular maintenance to remain operational. This can take a pump out of service for hours, often necessitating the need for a back-up pump to provide process continuity. It also takes the full attention of at least one skilled onsite technician.
Pumpheads across the company’s entire Qdos range do not need to be taken apart. Instead, the pumphead is simply removed as a single unit and a new one clicked in place. It takes one operative less than a minute, offering substantial benefits in terms of time-saving and onsite health and safety.
As Cory Sonner told the webinar audience, “If you can run an smartphone, you can operate a Qdos. The pumphead life, ease of installation, operation, and maintenance tip the scales in our favour.”
Pump design
Qdos CWT goes further still and is the world’s first peristaltic pump with no tube, which represents a step-change in the mechanics of peristaltic pump design.
While a conventional peristaltic tube is compressed flat via plastic deformation, the Qdos CWT pumphead incorporates an EPDM element, which is elastically compressed against a PEEK track. This reduces material stress and fatigue, providing significantly longer service life, reduced maintenance and less plant disruption.
Successful trials
Multiple onsite trials have already been carried out at water treatment plants in Europe and the US and show that CWT pumpheads can be expected to last two to four times longer than other tube-based dosing pumps. Reflecting on trials carried out by Vessco with municipalities in Iowa, Sonner explained how they had to overcome initial resistance to peristaltic pumps, which are new to many clients, but that the outcomes were very positive.
“The expected pumphead life, ease of installation and operation tipped the scales,” he said.
Case study 1: Regulatory change in Huxley, Iowa
Tightening regulations affecting Huxley water treatment plant in the US state of Iowa meant that an ion exchange softening system, requiring just a couple of chemical metering pumps, had to switch to reverse osmosis, which needed over 11 different chemicals. The superintendent required an autonomous system that required minimal interventions for maintenance.
The longer lifespan offered by Qdos CWT, over standard diaphragm and peristaltic pumps, made it a “no brainer” to switch, according to Sonner, who manages capital project equipment sales for Vessco. He said, “With the CWT pump we were able to offer a complete solution with safe accurate operation and maintenance.”
Case study 2: Streamlining operations in Grinnell, Iowa
Vessco worked on another ion exchange softening system with the superintendent at the water treatment plant serving the city of Grinnell, Iowa, which had multiple pumps with widely differing flows. The superintendent had no feedback on pump operation and leakage and an audit of pressures and chemical feed rates showed that they fluctuated measurably.
Describing the project, Sonner explained how Qdos CWT gave the operator more control over chemical metering. “The turndown is a great feature with the Qdos, not to mention limiting the spare parts he needs. He’s very happy with the head life and is looking forward to changing out other installations around the plant and distribution system.”