New Submersible Pumps in Discharge Tube for a Wide Range of Applications
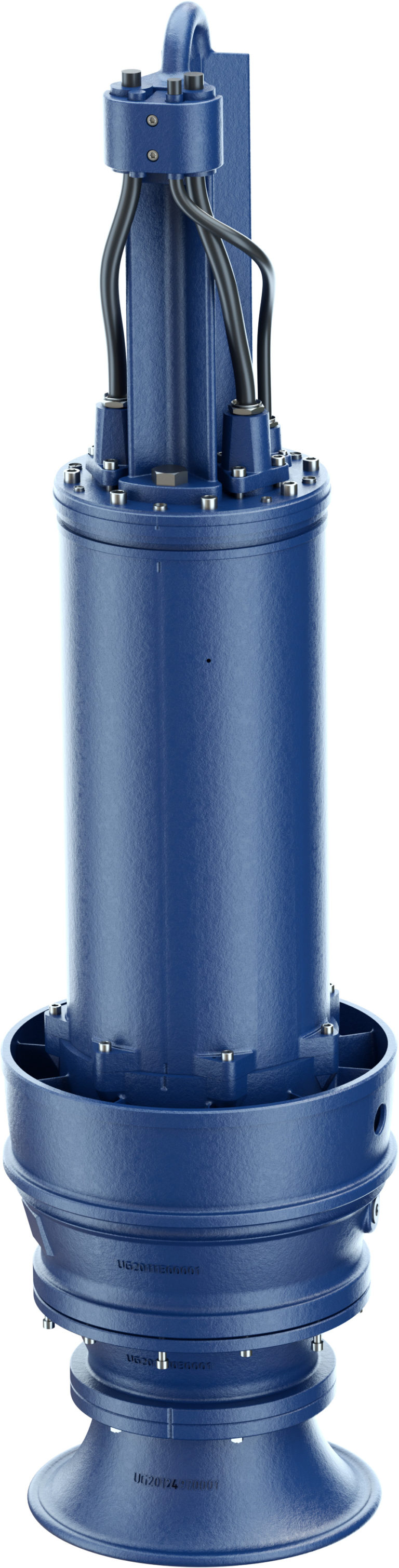
The new AmaCan D submersible pumps in discharge tube are designed for low life cycle costs. (Image source: KSB SE & Co. KGaA)
When selected with optional corrosion-resistant and abrasion-resistant materials the type series can also be used in water pollution and flood control or in seawater aquaculture systems. The pump generates a maximum flow rate of 8000 m3 per hour and a maximum discharge head of about 30 m. The highest motor rating available as standard is 340 kW. Priorities set by the developers were to achieve a high operating reliability of the waste water hydraulic systems as well as high hydraulic efficiencies. Here, they were focusing on the typical operating ranges of submersible pumps in discharge tube. The outer design of the pump sets has been shaped by the pump manufacturer's decades of experience with specifically this type of pump. The pump's self-centring, non-positive seating in the discharge tube, sealed by an O-ring, makes it easy to install and remove. No anchoring or anti-rotation elements are needed.
Integrated, intelligent sensor monitoring detects any vibrations or leakages and measures the temperature of bearings and motor. It provides continuous supervision of operation and early detection of malfunctions as well as the option of predictive maintenance. With regard to low electricity consumption, the drives of submersible pumps in discharge tube also play a key role. This is why all electric motors are of an efficiency corresponding to class IE3 for standardised motors to IEC 60034-30. This is particularly important for powerful pumps with a high frequency of starts. Two bi-directional mechanical seals reliably prevent water ingress into the motor space. A chamber filled with environmentally friendly oil ensures cooling and lubrication of the mechanical seals even when gas-laden fluids have to be pumped. Generously dimensioned ball bearings sealed for life support the stainless steel shaft.
Special focus was further placed on the design of the cable gland. Individual conductors stripped, tinned and sealed in resin ensure that the cable gland is absolutely watertight. Even in the event of damage to the cable sheath or the insulation, thanks to this design the pump is protected against short circuits. To ensure that the pumps can be easily dismantled even after years of operation under tough conditions, all wetted screwed connections are made of high-grade stainless steel.
Source: KSB SE & Co. KGaA