New PMAC Motors are Often the Best Solution for Processing Applications
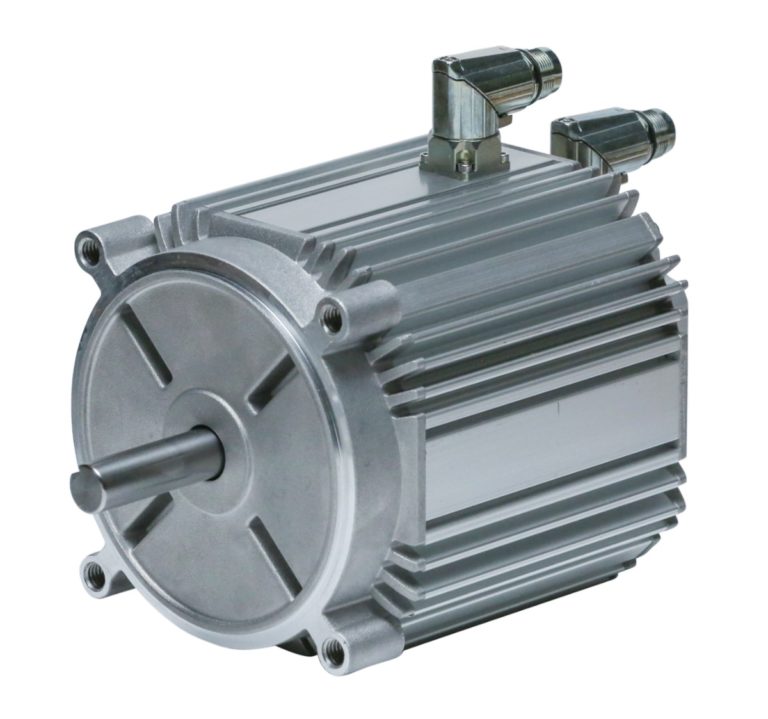
A high-performance and low-cost alternative to servo motors and induction motors. (Image source: Bison Gear & Engineering Corp.)
Up until now, engineers that needed to control an axis on a machine would typically specify a costly servo system. Other options included motors and drives that could not reliably deliver a specified speed without a feedback system and labor-intensive commissioning. Bison’s new product line provides the intermediate solution between servos and induction motors, delivering velocity control using recently introduced variable frequency drives.
What is a PMAC Motor?
A PMAC motor is a relatively new product in the marketplace. PMAC stands for permanent magnet, alternating current. This family of motors uses a stator wound to operate on three phase windings coupled with a rotor that includes permanent magnets. These motors rotate synchronously with the rotating magnetic field generated in the phase windings.
From a machine builder's point of view, PMAC motors operate at the exact speed you specify using a VFD (variable frequency drive) instead of a servo drive. That is a huge advantage when working on multiple axis machines that require more accuracy than traditional induction motors. Induction motors operating speed is driven by the supplied frequency; but slight changes in operating voltage or operating temperature can lead to speed variations that are not desirable.
Why have PMAC Motors Emerged Only Recently?
The many benefits of PMAC technology have been known for many years:
- Motors operate synchronously with input frequency
- Ability to operate at specified speed even with normal line voltage variation
- Improved efficiency compared induction motors
However, commercially available PMAC products have only recently begun to emerge. Bison Gear & Engineering has led this trend offering a broad range of full system PMAC solutions, with a broad power range, mounting, enclosure and voltage configuration options. The emergence of improved variable frequency drives has created a product ecosystem ripe for PMAC technology. Multiple manufacturers now produce VFDs capable of driving permanent magnet style AC motors, with applications in most market segments previously only optimized with servo motors.
Many of the VFDs already installed for induction motors can also support PMAC motors. The higher performance PMAC motors can often replace the existing induction motors without the need to change or upgrade any other components.
An encoder is not required
Today’s VFDs that run PMAC motors do so without sensors, eliminating the need for encoders. The majority of velocity control applications do not need the feedback in order to operate at a designated speed. Running without an encoder eliminates the effort required to commission the encoder as well. Bison has enclosed encoders (as a standard option) available if your application uses a PLC and needs to operate at low input motor speeds.
PMAC as an Alternative to Servo Motors
PMAC motors offer a no-compromise solution for many applications where servo motors are used today—but at less cost.
Velocity control is critical for manufacturing and other applications involving the coordination of multiple actions performed in conjunction with each other. For example, the motors driving a packaging machine need to operate in sync with one another to ensure proper machine operation. Another example of velocity control is constantly maintaining the specified speed of fans in convection ovens even while the line voltage varies considerably depending on installation location.
Most machine builders use servo manufacturers PLCs and drives to run their machines. Many of these servo manufacturers have VFDs that can run new PMAC style motors and operate within the PLC programming, saving cost compared to the servo drive.
PMAC as an Alternative to Induction Motors
Not only is there a compelling case for considering PMAC motors as a less expensive and simpler alternative to servo motors, but PMAC motors are also replacing induction motors in many applications. For an incremental cost compared to a comparable induction motor, the existing investment in an VFD can be leveraged to easily upgrade to take advantage of the performance improvements and velocity and motion control previously only available with servo/encoder systems.
PMAC motors have several important advantages.
- Ability to synchronize multiple axes at the same speed
- Efficiency: lower heating watts generated means a cooler running motor, increasing life
- Power density: Higher efficiency allows overall motor size to be reduced. A 1Hp VFsync motor consumes 176 in3 compared to a conventional 3 phase motor at 398 in3.
- Reduced weight: Improved use of magnetic materials helps to reduce weight. With the same 1 Hp example, the weight is reduced from 38 pounds to 14 pounds.
- Wider speed range: PMAC motors can provide nameplate torque, without a feedback encoder, as low as 500 RPM, synchronously.
- Improved starting torque, typically 30% better than induction motors.
In Conclusion:
Velocity control applications are prime candidates for Bison’s new VFsync product offering. The platform of motors operate well with most manufacturers' drives, including leading PLC/servo panel setups, as these manufacturers have VFD’s that integrate within the PLC system architecture. In most applications encoders are not required, reducing the costs associated with feedback, shielding and cables. Commissioning the new motors are straightforward and typically require 7-10 attributes from the motor to be up and running, significantly less intensive than compatible servo motors. The motors are manufactured at Bison’s motor facility in St. Charles, Illinois and are readily available.
Source: Bison Gear & Engineering Corp.