New Generation of Hydraulic Jet Pumps from JJ Tech
Recent developments have made a new generation of hydraulic jet pumps a viable solution for a wider range of wells while requiring much less maintenance for the end user.
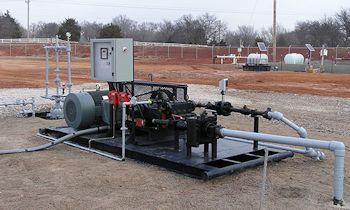
JJ Tech
The benefits of the jet pump are: “no moving parts” down-hole, ability to produce sands and solids, no gas locking, the power fluid can be treated with corrosion and scale inhibitors, ease of optimization with software, production rates can be changed by adjusting injection pressure and rate, capability of producing high volumes of fluid and ease of serviceability because nozzle and throat can be hydraulically retrieved with no rig or wire line.
However, over the years jet pumps have acquired a negative reputation due to the maintenance issues that come from powering them with conventional plunger pumps, as well as not being a good solution for low bottom-hole pressure wells. Recent developments in jet pump design combined with a virtually maintenance-free triplex diaphragm pump have set jet pumps on a new and improved path, changing their reputation for the future.
Low Bottom Hole Pressure N. Oklahoma Hunton Limestone wells. JJ Tech has replaced numerous ESP’s in Hunton horizontal oil and gas wells. ESP’s have not proven to be an economical form of lift due to pump off conditions, high GLR, fluid compatibility issues and produced solids. These 7000’ TVD wells require artificial lift production rates ranging from 120 – 480 mcf/day and 30 – 160 bpd with oil cuts ranging from 2% – 60%, while producing bottom-hole pressures range from 95 – 227 psi. The jet pumps are configured in concentric strings by running integral joint tubing inside of production tubing (either 1.9” inside of 3.5” or 1.66” inside of 2.875”). The concentric string configuration (Fig. 1) allows the jet pump to be placed in the lowest spot in the wellbore, being either below a window or out in a horizontal lateral (Fig. 2). This gives the jet pump the highest pump intake pressure possible while maintaining optimum efficiency by allowing the gas to travel up the casing rather than through the pump. Power fluid (produced water) is injected down the integral joint tubing while power fluid and produced fluid return up the inner annulus. This down-hole configuration results in low HP requirements, typically ranging between 30 – 75 hydraulic HP in this case.
An ideal alternative to triplex plunger pumps. The required maintenance of plunger pumps was, until now, the jet pump’s biggest downfall. The necessary continuous duty running conditions, high pressure requirements, and leaking of produced fluid and plunger lubricating oil onto the location result in constant packing or valve changing. Wanner Engineering’s T8045 diaphragm pump (Fig. 3) has proven to be a virtually trouble-free alternative to conventional plunger pumps. The 80 HP diaphragm pump eliminates VOC emissions, packing maintenance and plunger wear with its seal-less design. It also requires less routine maintenance and has the ability to handle corrosive and abrasive fluids. The diaphragm pump can operate with a closed or blocked suction line and run dry indefinitely without damage, avoiding downtime and repair costs. Low NPSH requirements allow it to operate continuously with a vacuum inlet condition, so positive suction pressure is not necessary. The T8045 comes with a 1 year manufacturer’s warranty and is designed to run up to 3000 psi at 1543 bpd. Its design benefits and horsepower make it the ideal alternative for powering most hydraulic jet pumps in the oil field industry.
Source: JJ Tech