Maag: Successful Relationship in Malaysia
Upgrading and modernizing existing equipment is essential to not only keep the machine performance at the highest level but also to decrease operating costs or debottleneck systems. The ever increasing price pressure that most companies will face at some stage forces pellet producers to keep an eye on their equipment.
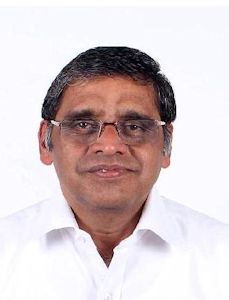
Mr. Balasubramanian (Image: Maag)
This is of importance due to the fact that polymer pumps and pelletizing equipment are key elements in polymer production. It is particularly the wear of the moving elements in the pelletizer (rotors incl. counter knives and infeed rollers) that has a considerable influence on the operating costs since choosing the wrong profile or material for the rotor and the wrong adjustments for the pelletizer will impact the end product quality as well as the waste rate of the material. Therefore an intensive cooperation and information exchange with the machine supplier will help in most cases to reduce costs and extend the equipment life time.
A very good example of the above is illustrated in the relationship between Recron Malaysia, Automatik Malaysia and Maag Singapore.
Using Maag’s new bearing material featuring an improved clearance for existing polymer pumps, during debottlenecking projects at Recron, a higher production capacity of approx. 15% was achieved. The latter was made possible without changing other auxiliary equipment such as universal drive shafts and drive units. The solution was devised jointly by the machine user (Recron) and the gear pump supplier (Maag). Thanks to Maag Singapore, and the professional consulting it provided, we discovered together the best way to increase production. With the changes implemented, our plant is now producing more than before with less problems. ”Of particular notice is the fact that the positive results yielded have been achieved with little investment; Mr Balasubramanian, Technology Manager, explains”.
Further down the process, in addition to Maag’s pumps, Automatik Plastics Machinery‘s under water strand pelletizer also played an important role, with a view to further increase the pellet quality and to reduce the consumable costs. Potential improvements were identified during initial discussions and a subsequent inspection of machines and production processes. New start up devices were put in place to reduce waste during start up periods. A number of old devices were also replaced to both avoid twin pellets and optimize the existing tools such as rotors and bedknives in relation to the actual product needs. The changes implemented on the machines combined with the necessary training of the operator and the maintenance staff helped us to increase productivity with the added resulting benefits of lower maintenance time and costs.
“We were particularly impressed by the high quality and competence of the support provided by Maag and Automatik’s team in this region. As a result, we are very pleased as this is very important for us”, said Mr. Balasubramanian. “Beside the technical competence of the local employees and also the superb grinding service for the cutting rotors including the bedknives, we are now able to achieve lifetimes which could not have been obtained if working with other grinding service suppliers for such tools”, Mr. Balasubramanian continues.
“The close cooperation with our customers and the level of technical support provided make Maag and Automatik a truly unique supplier of services in this industry for this region”, Chew Phenghuat and Seah Poh Siang explain.
Maag Singapore was established in 2000 whereas Automatik Plastics Machinery opened its service centre in Malaysia in 2009.
Source: Maag Pump Systems AG