LEWA: No environmental impact – Plasticizer production requires hermetically tight process diaphragm pumps
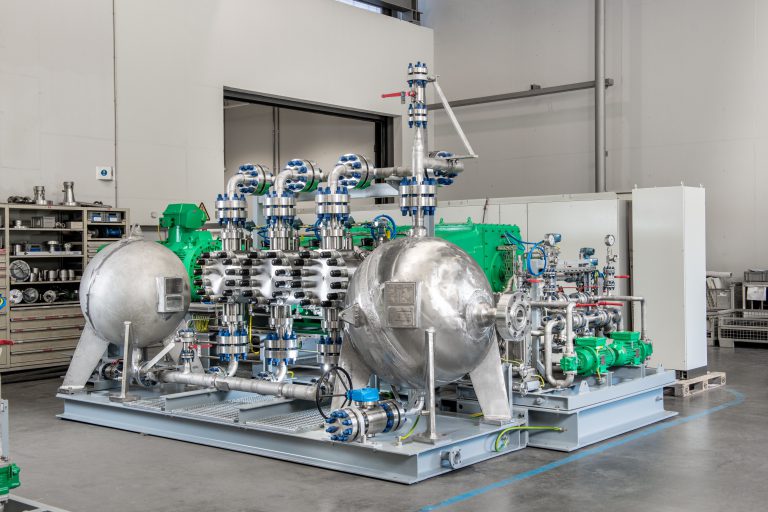
In supercritical applications like plasticizer production, hermetically tight process diaphragm technology is required. (Image source: LEWA GmbH)
For 2026, researchers anticipate a total volume of 10.5 million metric tons. However, special care is required in the production of these colorless, odorless fluids that are used to make plastic products more flexible and stretchy and in other applications. Some plasticizers are considered highly toxic and can have a severely negative impact on health and the environment if mixed with other media such as water or grease. Since this has to be taken into account as early as the chemical manufacturing stage, rugged process diaphragm pumps are usually used. These pumps are designed without dynamic seals, thereby guaranteeing absolutely safe handling of carcinogenic and toxic fluids. A comprehensive approach, which includes the design of hermetically tight pumps, planning, sales, commissioning and services, ensures that the project is handled efficiently and successfully.
In total, 87 percent of all plasticizers were used for plastic products in 2018, according to data from the market research institute Ceresena Research. At 2.33 million metric tons, various film products based on the commodity plastic polyvinyl chloride (PVC), such as many floor coverings, cables and hoses, accounted for most of the demand. They all get their special performance characteristics from the addition of colorless and largely odorless plasticizers. The additive allows naturally hard, brittle materials to become flexible and stretchy without losing their dimensional stability, and sometimes make them useful in the first place. Plasticizers used for this purpose are also called softeners. Most of them are phthalates, an ester that can exist in many variations.
Robust, low-wear technology required
Therefore, particularly high safety measures must be taken in the production of plasticizers when non-toxic, long-chain plasticizers are being manufactured from the gasoline-like preliminary product naphtha using a multi-stage process. This especially applies to the use of pumps, since they are responsible for conveying the often toxic fluid mixtures without problems and are used during the production process as reactor filling units or pressure boosting units. They also have to function properly in extreme operating states using installed safety mechanisms, or prevent operating damage after operating errors. For safety reasons it is preferable to use hermetically tight process diaphragm pumps. Thanks to their safe and robust technology, such pumps guarantee that the naphtha mixture is conveyed without leaks, thereby preventing hazardous liquids from leaking into the environment. This is primarily because the pump technology functions without dynamic seals. The PTFE diaphragm is the transporting component and simultaneously, the static seal of the pump's working area: a basic requirement for safely pumping hazardous fluids. Thanks to this principle, it is possible to achieve low life cycle costs and low maintenance costs at the same time. This cost reduction is based on the patented LEWA DPS diaphragm protection system. A spring supports the diaphragm's suction movement and reliably ensures that the diaphragm is always in the correct position. The monitoring system immediately indicates any damage to the diaphragm. The pump remains hermetically tight and can be shut down in a controlled manner if the diaphragm needs to be changed. In addition to the DPS, each LEWA process diaphragm pump has an internal overpressure safeguard. These protection systems ensure that the machine can be reliably controlled even in critical operating states, and that leaks can be avoided.
Integration of the pump unit into the overall concept is crucial
However, production process efficiency depends on more than just selecting and commissioning suitable pump technology. For this reason, a comprehensive approach that includes development, production, and service offers clear advantages. Pump/system manufacturers are only able to offer users a complete, individually tailored solution for the respective project when all factors come from a single source. The pumps should be integrated into an overall concept covering the complete service spectrum from planning support to active system and from tool consultation to a warehousing strategy. This kind of "everything from a single source" approach ensures more efficient communication and focuses the required expertise at the interfaces of individual task areas.
This is why experienced system manufacturers like LEWA create piping design studies and feasibility analyses ahead of time, before the design plans of the responsible engineers go into production. This approach enables customer-specific requirements to be integrated into the planning stage and design components to be adapted to whatever situation is at hand. Thanks to their space-saving mono-block design, LEWA process pumps are suitable even for the smallest installation spaces. After the system is commissioned by a service engineer, a service expert is also assigned to the customer for the entire life cycle of the requested pumps. The expert provides advice in case of application difficulties and carries out any maintenance work that arises. Solutions with a comprehensive approach like this enable faster handling without problems, since challenges and difficulties can be simplified and communicated more easily within a company. An "all-in-one" solution guarantees the necessary process quality in risky applications such as plasticizer production.
Conclusion
Global production volumes of plasticizers for use in plastic products are constantly increasing. Leak-proof metering is critical here, since plasticizers are produced from a fluid mixture based on naphtha, which is toxic to humans and the environment. That is why the process diaphragm pumps that are used must satisfy highest safety requirements to ensure that the fluid is pumped without any problems. Integrating the pure production and delivery of the pump into an overall concept that also includes planning, consultation, commissioning and maintenance service is helpful here. Thanks to its hermetically tight diaphragm pump technology, LEWA can provide a safe solution in this area and is able to offer a comprehensive concept consisting of planning, commissioning support and warehousing strategies. At the same time, efficient communication and concentrated expertise accelerate the overall solution being implemented.
Source: LEWA GmbH