Innovative Gear Pump Ideal for Sensitive Solids Available Through Michael Smith Engineers
The simple design, reliability and ease-of-maintenance of internal gear pumps makes them a popular choice across a wide range of industry applications such as general processing, chemicals, oil & gas, food & beverage, refining, plastics and resins.
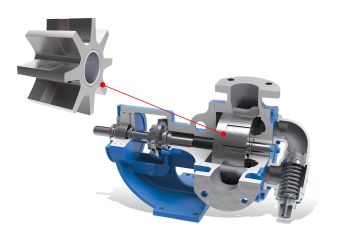
Michael Smith Engineers
The Viking Universal Seal range available through Michael Smith Engineers is one of the most established and widely used positive displacement internal gear pumps and is underpinned by Viking’s extensive practical and technical experience in fluids handling.
A good example of Viking’s innovative approach is a recent addition to their Universal Seal Range which features a modified ribbed / stepped idler gear design. This pump has been specifically developed for sugar processing but is also ideal for other applications where there are crystals in the pumped fluid. By removing 0.9mm (or 900 microns) of material from 80% of the flank of each idler gear tooth on both sides results in reduced gear-to-gear contact that could damage tiny sugar crystals or other solids in the pumped fluid.
Available in either hardened iron or hardened steel, the ribbed idler alternates position on each tooth to minimise wear on the rotor teeth in any given spot and since the idler turns at a different speed than the rotor, the contact point changes with each revolution of the rotor gear. The most significant impact of this is the creation of additional ‘slip paths’ that allow liquids to slip back from the high pressure (discharge) side of the pump to the low pressure (inlet side), the amount of which depends on the viscosity of the pumped liquid.
The pumps capacity on high viscosity liquids using ribbed idlers is virtually identical to the performance of pumps which have standard (non-ribbed) idler gears. For example, on liquids with a viscosity of 10,000 cSt operating at 50 RPM, the capacity is reduced by only about 1% compared to the standard pump performance at 3.5 Bar G, 7 Bar G and 10 Bar G.
By simply changing the idler gear from a standard to a ribbed idler and slowing it to appropriate speeds, users have the flexibility and convenience of using the same pump for liquids containing sensitive solids or for pumping other liquids such as syrups and molasses by switching back to a standard idler gear. This provides manufacturing plants with the potential to cover all of their positive displacement pumping needs with one or two sizes of the same pump which helps simplify plant operations and maintenance, while increasing reliability and uptime.
Viking Universal Seal Pumps also provide the benefit of being able to accommodate virtually all types of seal. These can be packing, component or cartridge mechanical seals which can be easily fitted, usually without bracket modifications. This means that operators have the flexibility
to benefit from the latest sealing technology to both maximise performance and to meet the ever-changing fugitive emissions standards.
Source: Michael Smith Engineers