HERMETIC Refrigerant Pumps for the Largest Bobsleigh, Luge and Skeleton Track in the World
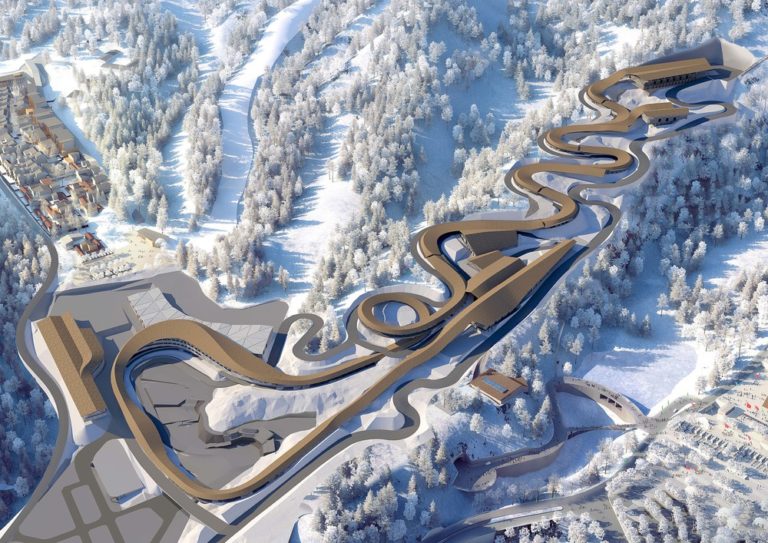
Planning office Deyle and Johnson Controls relied on HERMETIC canned motor pumps for the design and construction of the Olympic ice canal in Beijing. (Image source: HERMETIC-Pumpen GmbH)
For the athletes, the artificial ice canal holds high technical difficulties with innovative passages. In the background, sophisticated technology ensures perfect and constant competition conditions as well as safety according to high European standards. Responsible for the planning was the Stuttgart planning office Deyle (PBD) that won the state tender for the Olympic facility. The contract for the foreign share in the implementation of the entire refrigeration concept was awarded to air conditioning refrigeration specialist Johnson Controls. Hermetically sealed canned motor pumps from HERMETIC-Pumpen GmbH ensure a safe and reliable supply of ice. The pump types used include standard refrigerant pumps and custom-made products specially developed for the application
Track and refrigeration design
One of the most complex operations in the artificial ice business is designing and building a bobsleigh and luge track. When planning an ice channel, the track is designed first. After the "Refrigeration Design" follows the planning/design/construction of the refrigeration system including all refrigerant lines along the track and the heart of the entire system, the refrigerant pumps. Track design and refrigeration design from a single source are what the new sports facility needed. This had the enormous advantage that all concepts were perfectly coordinated and no compromises were necessary.
Demanding requirements for refrigeration technology
The challenge in refrigeration design: The cooling system must produce a consistent, flawless ice surface over the entire length of the track. The ice surface must withstand the weight of the bobsleighs, but also compensate for changing weather conditions and temperature fluctuations to ensure that all athletes find the same competition conditions. Also, the enormous differences in elevation and the course of the sun result in different climatic conditions along the bobsleigh track that affect the ice differently in the various sections of the track.
The planners must have a high level of knowledge and experience that few in this industry have. In addition to the planning, the components used – especially the refrigerant (canned motor) pumps – are of great importance. "Bobsleigh tracks with their constantly changing loads and numerous segments to be cooled with elevation differences of up to 130 metres place extreme demands on the refrigerant pumps", says PBD Managing Director Uwe Deyle, who is considered one of the leading experts in this sector having planned twelve artificial-ice bobsleigh tracks including six Olympic tracks. Deyle and Johnson Controls decided to use canned motor pumps from HERMETIC-Pumpen GmbH to pump the refrigerant.
Varying pressure requirements due to different pumping heads
An ammonia (NH3) refrigeration system is used to produce the ice. The NH3 is pumped at –18 degrees Celsius. The toxic effect of ammonia requires the highest level of safety and leak-tightness of the system and the individual components. The pumps are located in the engine house, from where they transport the refrigerant through seemingly endless pipes in the concrete structure to the furthest point on the track. The pumping head at this point is 249 metres. The best possible icing requires the optimal supply of ammonia to all points of the track. Therefore, the track was divided into four zones. Four HERMETIC canned motor pumps ensure a safe and efficient refrigerant flow. The pumps are ideally suited to the different elevations of the various track sections and the associated pressure requirements. Each zone uses one pump. A second one was provided as a backup as in almost all chemical plants. Although a technical failure of the pumps can virtually be ruled out, continuous operation cannot be guaranteed due to any incorrect operation of the system.
Completely leak-free, low-wear and low-maintenance pump technology
In contrast to magnetic-coupling or centrifugal pumps with mechanical seals, canned motor pumps do not have any vulnerable dynamic seals. Instead, canned motor pumps have a second hermetic safety containment that prevents any leakage of pumped media and emissions. The design-based omission of wear-prone components such as shaft seals, couplings and roller bearings ensures a high degree of operational safety, almost negligible wear and the best MTBF (Mean Time Between Failure) values compared to other pump technologies. "Every canned motor pump from HERMETIC features sophisticated technologies. These include, for example, the unique ZART principle by HERMETIC. If the pump is running at the duty point, there is no contact between rotating parts. The complete compensation of the axial forces in conjunction with hydrodynamic slide bearings guarantee extremely high reliability in the operator's processes. This drastically reduces the life-cycle and operating costs of a canned motor pump,” explains Alexander Frank, Area Sales Manager who oversaw the project at HERMETIC.
Widest range of canned motor pumps, fast delivery and worldwide service
With the three product lines S-Line (24 standard types), V-Line (more than 400 variant pumps) and E-Line (engineered-to-order) geared towards the requirements of the refrigeration industry, HERMETIC offers the largest portfolio of canned motor pumps for industrial refrigeration technology on the market. Pumps from all three product lines are installed in the Olympic ice channel in Beijing. Uwe Deyle has already trusted the technology and quality of HERMETIC canned motor pumps several times. “With its pump portfolio, HERMETIC covers all – sometimes even the most extreme – requirements that no other manufacturer can meet. The advice is excellent and the pumps have a problem-free service life of several decades in practice,” says Uwe Deyle with conviction. HERMETIC pumps now ensure perfect ice in four World Cup and ten Olympic facilities with the highest level of safety for people and the environment.
Zone I: Custom designed canned motor pump for a pumping head of 249 metres
A multi-stage canned motor pump of the type CAM 42/6, N74rm-2 is used to supply Zone I that includes the highest point of the bobsleigh, luge and skeleton track. With its extremely favourable NPSH values, the CAM series - depending on the pump type - enables the operation of the pump with very little inflow of the pumped medium. This also results in a relatively low space requirement. The required suction head in the engine house, where the pump is located, is only 2.8 metres. As an individually developed pump of the HERMETIC E-Line, the compact unit is designed for a delivery rate of 44m³/h at a pumping head of 249 metres. Six impellers in a row provide the necessary pressure increase.
Zones II, III and IV: Fast delivery thanks to preconfigured canned motor pumps
In zones II and III, a canned motor pump type CAM32/3, N34L-2 each from the HERMETIC V-Line ensures safe and controlled refrigerant flow. The pump has an inducer to reduce the required suction head. The delivery rate is 18.0m³/h at a pumping head of 139 metres.
In Zone IV, the pump with the smallest hydraulics is used. The five-stage CAM 2/5, AGX4.5 pump designed for a delivery rate of 3.9m³/h and a pumping head of 97 meters comes from the HERMETIC S-Line. All pumps meet the high HERMETIC quality standards including the ZART principle for contact-free and wear-free operation. Alexander Frank explains: "With our HERMETIC V-Line and S-Line we draw upon standardised assemblies and prefabricated components. In conjunction with our realigned value stream-oriented production and the automated design process, this enables lean processing of projects. This offers building owners and plant manufacturers reduced development costs and valuable time advantage. The planning office completed the final clarification of the delivery content in September 2018 only four months after initial contact. Johnson Controls placed the order in February 2019. The S- and V-Line pumps were installed as planned in July 2019. The E-Line pumps were delivered also according to plan in December 2019."
Excellent cooperation, high service competence
Johnson Controls, one of the leading providers of industrial refrigeration technology and the world's leading company in the use of natural refrigerants, is also satisfied. Lambert Köppen service engineer at the refrigeration system manufacturer says: “Our systems are characterised by their environmental friendliness, high performance and cost-efficiency. The quality and reliability of the individual components are very important. We have had a good business relationship with HERMETIC for many years and are convinced of the quality of the pumps used. We have had an excellent experience, especially when it comes to reliability and long-term stability of the pumps. We also appreciate the good communication between the companies including the coordination with the planning office." Uwe Deyle adds: “In such time-critical projects of international importance observed by the public, not only the product quality but also the reliability and, particularly, the service competence of the partners involved play an immensely important role. Even when unexpected issues arise, the experts from HERMETIC's headquarter are on site within a few hours and show that they not only know their products but are also competent to technically evaluate the application due to their extensive experience. Planners and system builders cannot have better experiences with a manufacturer." Alexander Frank is pleased about the confidence and says: "Open, timely and success-oriented communication is enormously important for such a project, and this is exactly what has once again worked extremely well between all three parties in this case."
Source: Hermetic-Pumpen GmbH