Editorial: How to Eliminate the Risk and Mess of Polymer Spills
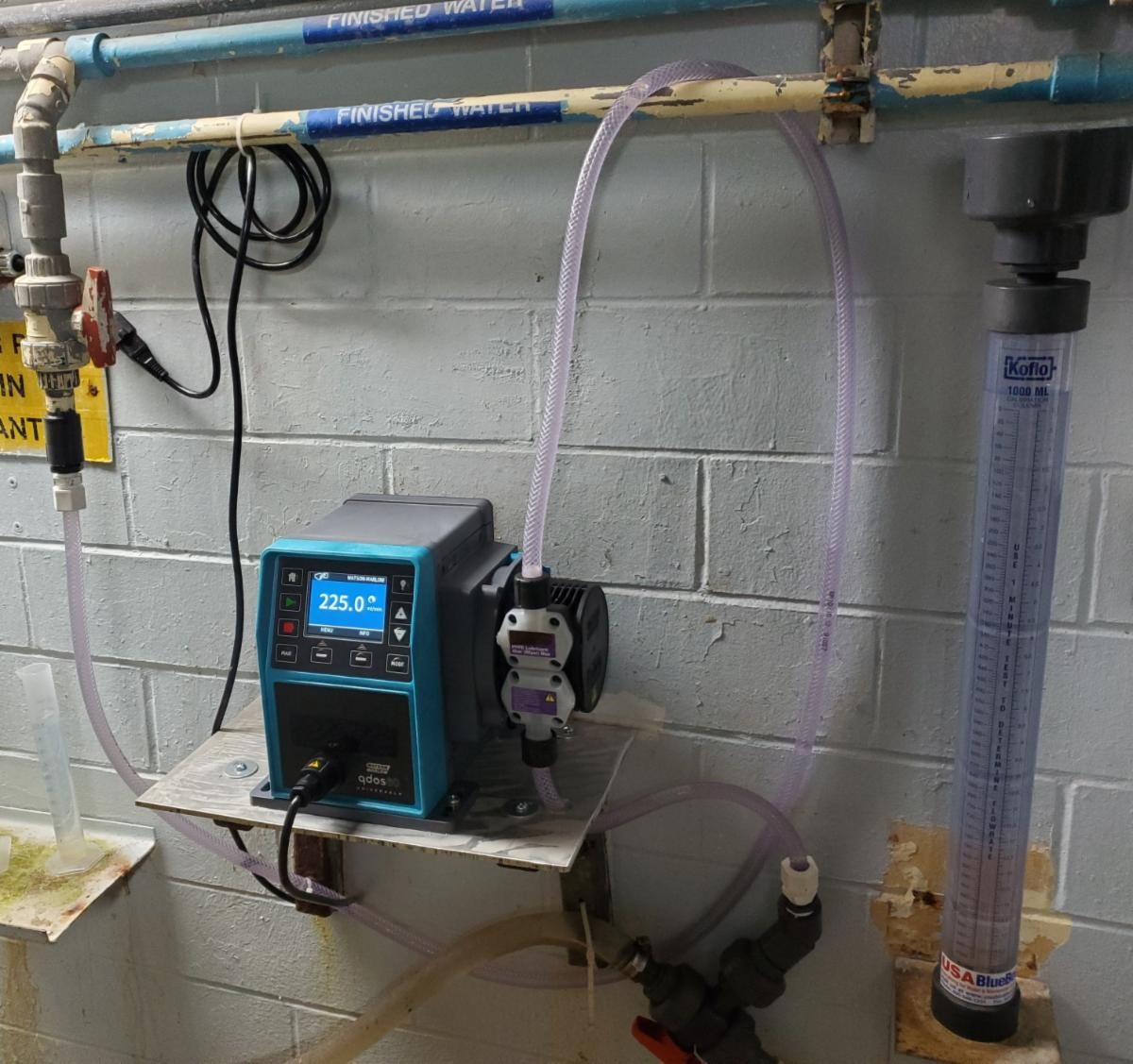
Image source: Watson-Marlow Fluid Technology Solutions (WMFTS)
Precision Chemical, LLC, supplies advanced water treatment technology, including customized water chemistry programs, to industries ranging from power plants, pharmaceutical plants, automotive, plastics, rubber, food and dairy, to commercial and institutional HVAC systems. The Indiana-based OEM maximizes system efficiency for its customers which would be extremely inconvenienced by a polymer spill.
Fred Shurtz, President of Precision Chemical, LLC, said: “It’s a pain cleaning up polymer because the product basically multiplies by magnitudes when water hits it. So, when we have to clean up a mess, we have to get lots of oil dry compound and then soak up the polymer and shovel it into a dumpster. It’s really no fun at all. But the big picture is we are not delivering the product [polymer] to the system which causes an disruption in operations. It sometimes takes days to get back to ‘normal’ operations following a spill.”
Water treatment operators therefore need to consider prioritizing the adoption of dosing solutions that avoid messy polymer leaks because of the following:
- Cost: Wasting polymers is expensive. Major producers of specialty chemicals recently announced price increases in products like polyacrylamide (PAM). Then there is the cost of cleaning products in the event of a polymer leak.
- Sustainability: To ensure a sustainable use of polymers is achieved by minimizing polymer use with accurate dosing pumps; eliminating chemical waste through leaks, and avoiding the need for cleaning chemicals in the event of a spillage.
- Safety: Spilled polymer is extremely slippery and difficult to clean, with the possibility of some residue left behind causing a safety risk of slipping for operators if it gets wet.
- Maintenance: Water treatment operators are under increasing pressure to produce more clean water so cannot afford downtime. Some rural plants also have a small workforce where regular, unplanned maintenance is a challenge.
ReNu PU (polyurethane) pumpheads for Qdos peristaltic pumps, from Watson-Marlow Fluid Technology Solutions (WMFTS), are designed to avoid messy situations by safely containing polymer spills in the event of tube failure.
ReNu PU pumpheads are available in two sizes:
- ReNu 20 PU - up to 28 l/hr (7.7 GPH) at pressures up to 4 bar (58 psi)
- ReNu 60 PU - up to 60 l/hr (15.8 GPH) at pressures up to 5 bar (73 psi)
Specifically designed for polymers, the polyurethane (PU) tubing element is aliphatic hydrocarbon resistant, therefore, the chemical cannot damage the tubing.
The recently released Qdos 60 PU offers accurate and repeatable flow for a broad range of chemicals including polyacrylamide (PAM) based emulsions and other viscous fluids and aliphatic hydrocarbons.
A Qdos 60 PU is dosing polyaluminum chloride (a polymer used in water purification which enhances flocculation and coagulation of pollutants) at the Oak Ridge City water treatment plant in Tennessee. The plant began a trial using the prototype ReNu 60 PU pumphead in May 2020. Three years later Oak Ridge City water treatment plant had not replaced the pumphead after continuous, maintenance-free operation without any polymer leaks.
Removing the impact of a potential polymer spill is one of the key benefits to using the Qdos 60 PU pump for Mark Terry, plant manager at the Oak Ridge City.
“The two most obvious benefits that the Qdos pump has provided to my water treatment plant is that we’ve basically experienced no polymer leaks since the Qdos pump was put into service and the fact that, aside from occasional calibrations, the pump has maintained a very consistent and accurate feed rate of the coagulant that we add to our raw water,” Terry said.
The specialized tubing sits within the sealed housing of the pumphead if a leak occurred, the pumphead would contain all the polymer spillage, minimizing chemical waste and stopping a potential safety risk.
Pam Simmons, OEM Sales Manager Process Industries at Watson-Marlow (US), said: “Even when you do clean up a polymer spill, there’s still the chance some will be left behind and it’s very slippery, so dangerous from a fall perspective. A polymer chain takes years and years to break down, so for safety reasons alone the Qdos 60 PU pump would be preferred over other types because of the containment in the pumphead. If the tubing breaks inside the Qdos 60 PU pumphead the optical leak detector senses that disruption and shuts the pump down, so your polymer spill is contained within the pumphead.”
Importance of chemical compatibility
As well as containment, water treatment operators must consider chemical compatibility for successful handling of polymers at their plant.
Water-soluble polymers are commonly used in wastewater treatment to remove suspended solids and contaminants. Oppositely charged sites on polymer chains attract the suspended fine particles to form larger groups; they settle at the bottom as a sludge to be removed, leaving clear water.
Polymers in liquid (emulsion) and dry form are employed for coagulation, flocculation, clarification, thickening and dewatering at water at wastewater treatment plants.
When polymer molecules are uncoiled and extended, they become fragile and can fracture by high-shear pumps such as diaphragm pumps. If agitated and mixed prior to use, the polymer chains will be fragmented and will not work as intended.
But it is not just polymers which can get damaged. Complex polymers such as PAM present challenges for some pump types and tubing, such as a diaphragm metering pump, and can lead to equipment failure, with clogging and spillage requiring regular maintenance.
A pump that meets chemical compatibility of polymers
The ReNu PU pumphead is a tube technology that increases the chemical compatibility range of Qdos pumps. Qdos 20 PU and Qdos 60 PU transfer polymers accurately (±1%) in a low-shear, gentle pumping movement that do not damage the chemical, which is critical with polymers.
Precision Chemical, LLC, switched from another pump type to Qdos 20 PU for handling polymers at a power plant in southern Indiana over 18 months ago. It is being used to deliver an emulsion polymer to both a thickener and to some tanks prior to a vacuum filter operation.
Fred Shurtz, President of Precision Chemical, LLC, said: “I was previously using a Qdos competitor’s product and was having issues with reliability, plugging, and tubes bursting. I switched to Qdos 20 PU because it was explained to me in detail why this pump would work when the other did not.
“Pam Simmons [OEM Sales Manager Process Industries at Watson-Marlow] explained that the emulsion polymer chemical I was using needed a more robust material like the PU or the tubes would continue to burst. She was correct as the Qdos 20 PU has worked very efficiently and reliably since my purchase. I used to have big emulsion polymer clean ups with the other systems due to breakage and I have not had any since switching.
“My previous polymer pumps would burst the tubes every two months. This meant clean ups and messes that the customer does not like to see. Plus, during this downtime, I’m not clarifying the water as I am supposed to be which causes other issues. With the Qdos 20, I went a full year before I switched out the head and when I switched out the head, it was not because it failed, but instead I felt like it may fail so I changed it out. Twelve months is a long time to go without changing out a tube with an emulsion polymer.”
The only part of Qdos pumps which needs to be replaced is the patented ReNu pumphead. Maintenance, when required, is quick and simple with no-tools pumphead replacement. The polyurethane tubing pumphead is designed for simple one-minute maintenance, providing a safe solution and enhanced productivity in PAM metering, and other flocculants and coagulants used in water treatment.
“Additionally, changing out the head was much easier than any other pump I’ve ever worked on. It literally took me two minutes to complete the entire process,” Shurtz added.
“Prior to using to using this system, the filter cake was thin and wet which at one point caused a shutdown of the generating unit. This is very costly to the customer to literally shutdown the entire unit. However, we have been very reliable since delivering the polymer accurately and consistently to the system.”
Summary
A polymer spill is an incident that is worth taking steps to avoid and a leak-free high-precision chemical dosing pump such as the Qdos 20 PU and Qdos 60 PU are specifically designed to eliminate those concerns while also providing high-precision accuracy, repeatability and minimal maintenance.