Editorial: Diaphragm Metering Pumps for Critical Mixing Tasks in Industrial Oligonucleotide Production
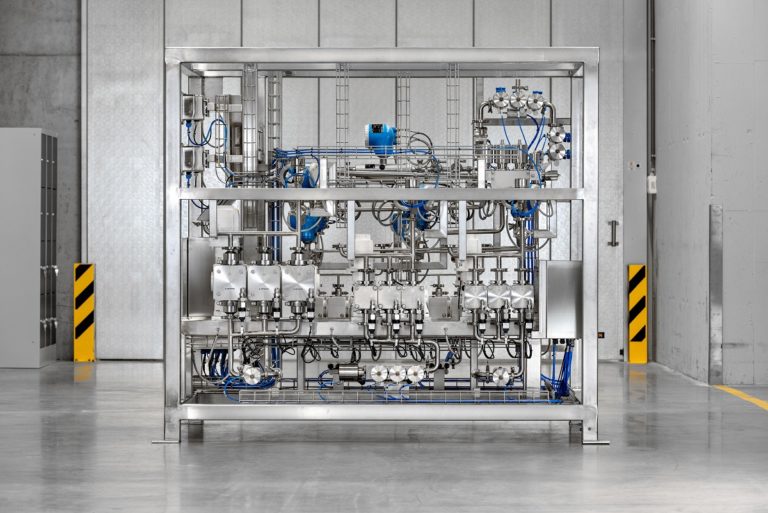
Production facilities for the manufacture of oligonucleotides must be able to handle flammable, toxic compounds as well as meet hygienic standards to ensure biological integrity.(Image source: LEWA GmbH)
The size of oligonucleotides lies between that of small, low-molecular-weight active pharmaceutical ingredients (APIs) and high-molecular-weight active pharmaceutical ingredients such as mAbs (monoclonal antibodies). Production facilities for the manufacture of oligonucleotides must be able to handle flammable, toxic compounds as well as meet hygienic standards to ensure biological integrity. Above all, however, they must be flexible and able to be scaled up from pilot plants so that they can ideally synthesize and purify a wide variety of drugs. In addition to standardized platform technologies, customer-specific GMP-compliant systems are also needed. Diaphragm metering pumps in these systems can meet the challenges of extreme chemical syntheses in the upstream process and also be used in contamination-free downstream processes. The flexible production of toxic and flammable fluid mixtures with widely varying flow rate requirements is particularly important here.
From rare diseases to chronic indications, the demand for oligonucleotide-based drugs is steadily increasing. Oligonucleotides are short, small (= oligo) sections of genetic sequences (RNA and DNA). Nucleotides are the building blocks of nucleic acids occurring in DNA and RNA chains. Oligonucleotides are therefore among the most important components of modern molecular biology. One of the most important ways of producing oligonucleotides with modified nucleotides for therapeutic purposes is industrial DNA and RNA synthesis.
In contrast to the frequently used, biopharmaceutically produced drugs that target proteins, oligonucleotides target disorders in the genetic code that are the cause of specific diseases. This makes them predestined for the treatment of previously incurable rare diseases, including neuronal diseases. The first antisense oligonucleotide drug was approved in 1998 as Fomivirsen, under the trade name Vitravene, for the treatment of CMV virus in AIDS patients.1 Several others followed, including Partisiran, approved in 2018 under the trade name Onpattro, a lipid nanoparticle-formulated drug that is one of the newer oligonucleotide therapies for polyneuropathy. Although various oligonucleotide drugs have already been approved by the authorities, they have not yet been established on an industrial commercial scale. Many other drugs are currently in the clinical phase prior to industrial production and are therefore the focus of ongoing research efforts, which increasingly include economic and quantitative aspects.
Challenge: Economical production of oligonucleotides
As a result, many specialized companies are focusing on efficient and safe GMP production of oligonucleotides using suitable production facilities. The aim is to maximize yield while maintaining high purity. This means that manufacturers of active pharmaceutical ingredients are faced with the task of making their own production processes more and more economical and robust so that they can be scaled up from laboratory or pilot scale to industrial GMP production with the highest possible yield in synthesis and downstream steps, without sacrificing quality or neglecting economic aspects.
An important step for oligonucleotide processes is known as media dilution, where the concentrations of a synthesized solution are adjusted. More concentrated storage solutions are continuously diluted to achieve the desired working concentration. The choice of solution depends on the subsequent steps in the downstream process. After the actual chemical synthesis, in which the nucleotides are added one after the other to a growing chain, the synthesized products undergo what is known as deprotection and purification steps to remove unwanted by-products. Accompanying process and quality control, e.g. in the form of mass spectrometry, ensures that the end product is within the defined specification window.
Continuous flow regulation
In order to meet increased demand by expanding production capacities, precise and continuously operating inline dilution systems must be provided. One of the biggest challenges here is maintaining a consistently reproducible quality of the required buffer within the narrow window for permissible concentration deviations. Among other things, continuous monitoring of the flow rates and the resulting dilution ratios is essential for this. Therefore, inline dilution systems typically consist of several channels with valves, where each channel is equipped with a multi-head diaphragm pump and a Coriolis flow meter. They measure the mass flow and keep the fluid quantity constant by controlling the speed of the metering pumps precisely. Pressure control valves with integrated electronically controlled pneumatic damping installed in the output-side manifold maintain low fluctuation and keep the mixing flow almost constant. This also applies to the pressure: Fluctuations are undesirable for the built-in measuring chains and interfere with the separation processes in the chromatography columns. Gas phase components and any temperature increase also have to be prevented.
After the mixing result is combined in the manifold, the ratio is analyzed using appropriate measurement technology, e.g. via the pH value and electrical conductivity. After programming the stored target values in the higher-level control system, these are available as different methods for system control. The recorded measured values are determined at a high sampling rate and continuously evaluated centrally. The pumps used must be corrosion-resistant, hygienic and have a robust design for continuous use. LEWA has detailed knowledge and many years of experience in high-precision metering and mixing thanks to its decades in the field of pump supply for the process chromatography of major OEMs. And this has also benefited the design of corresponding mixing and metering systems for oligo synthesis customers for some years now.
Package units for individual dilution tasks
The dilution systems designed and described are not standard systems, but customized inline metering and dilution systems that are designed and constructed as package units (PU) for the respective downstream process. A system of this type can have up to five process inlets and outlets – sometimes more – as well as various other connections, for example for flushing or waste water, to ensure flexible and continuous fluid transport. A cycle of chemical reactions is initiated by feeding in the respective synthesis fluids. Individual nucleotides are coupled and the desired modified chain sequence is formed by repeating the reactions. Due to the highly flammable fluids required, including solvents such as ethanol, isopropanol, toluene and acetonitrile, the systems often have to be designed for use in Ex zone 2 IIB T3. Inert gas (nitrogen) further protects the process. The inline dilution system for aqueous fluid mixtures in the downstream area provides high-accuracy buffer solutions for semi-continuous chromatography after synthesis. HPLC, ion pairing reversed phase (IP-RP) and ion exchange (IEX) chromatography columns are used for chromatographic purification.²
Individual dilution tasks can thus be implemented precisely and flexibly. Several 1,000 liters of solvent and aqueous fluids are required per kilogram of active ingredient. In order to be able to implement large adjustment ranges from a few liters per hour up to 6,000 l/h, it must be possible to call up an automated and continuous supply of changing mixtures for the downstream purification process via the system control. Several multi-head diaphragm metering pumps specially designed for pharmaceutical applications are used here. Their phase-shifted drive characteristics, typically with three to five pump heads, enable a low-pulsation overall flow rate. Thanks to the back pressure-independent characteristic curve, the entire metering and mixing process for oligonucleotide production is reliably continuous and absolutely reproducible at all times. No other type of pump can achieve stable linear and step gradients as well as reliable gradient characteristics more consistently. These hermetically tight pumps rule out backflow or plunger packing problems.
Large adjustment ranges and high production reliability
Because the production of dilution solutions sometimes requires very different flow rates, the systems must be designed to be flexible. One practical example required flow rates of a minimum of 40 l/h and a maximum of 2,500 l/h. A total of five LEWA ecodos hygienic diaphragm metering pumps were integrated into this system in order to be able to cover this large adjustment range flexibly. The pump heads are equipped with mechanically actuated, four-layer sandwich safety diaphragms. Since the area behind the diaphragm is subject to strictly regulated clean room environmental conditions, contamination with operating materials or process fluids cannot occur. Due to the GMP environment, which strives for high integrity with regard to contamination of any kind, hygienic versions of the pumps must also be used in this area of downstream processing. This goes hand in hand with acceptance test certificates 3.1 and consistently certified construction materials, such as FDA, USP or AOF certificates of conformity. All metal parts in contact with the fluid are mechanically and additionally electropolished and have a surface roughness of Ra ≤ 0.5 µm. Thanks to the hygienic design of the diaphragm body, which almost completely eliminates dead spaces, the pumps can be cleaned in the CIP process very easily and without prior dismantling.
The EHEDG EL Class 1 certificate for the ecodos pump type used is a decisive proof of quality with regard to the excellent inline cleanability of the fluid-side pump head. The materials used are 1.4435 stainless steel with a low delta ferrite content and steels with a higher alloy content, such as the more corrosion-resistant 1.4529 stainless steel or Hastelloy for fluids with a high chloride content. This makes the pumps suitable for metering highly corrosive and flammable fluids in oligonucleotide production over the long term. The patented four-layer PTFE sandwich diaphragm also helps here: It is extremely stable and ensures that operation can be continued safely even in the event of a diaphragm rupture, thus providing a high level of process safety. In an emergency, the integrated diaphragm rupture signaling system immediately reports a corresponding fault during operation without contaminating the rest of the process line. Only hermetic plunger diaphragm pumps offer such a high level of production reliability.
Precise control and continuous monitoring
In terms of control, the use of a servomotor and an intelligent control system enable different customer-side requirement profiles to be implemented and the adjustment range to be extended up to 1:200. The flow rate is traditionally adjusted via the stroke length and the speed of the pump motor via the frequency of an inverter. In newer concepts, the speed of a fanless synchronous motor or permanent magnet synchronous motor (PMSM) is variable and operating points can be approached precisely and reproducibly without manual stroke adjustment – thus making them compliant with GMP. At ±1 percent, metering accuracy is extremely accurate. To prepare the mixtures in the chromatographic environment, the flow rates of the individual pump lines must be precisely maintained. For this purpose, they are determined by Coriolis flow meters and precisely controlled at the specified target values using the speed control of the pumps. Additional online monitoring of the pH value and electrical conductivity ensures continuous control of the process conditions.
To ensure that the specified accuracies are maintained over wide adjustment ranges, correct suction-side pressures (NPIPA) must be ensured at the pumps. The abbreviation NPIP stands for "Net Positive Inlet Pressure" and NPIPA for "Net Positive Inlet Pressure Available". The NPIP is similar to the well-known NPSH, although the latter is only defined by the height. In contrast, the NPIPA is the measure of the pump inlet pressure present at the inlet valves through the system. The NPIP is determined by the static pressure upstream of the pump, for example by a vessel with or without pressure superposition or by the pressure in closed circular piping. If the NPIP is too low, cavitation may occur in the pump heads if the steam pressure falls below the value specified. If, on the other hand, a diaphragm metering pump has a net suction pressure that is too high, there is a risk of excessive and uncontrolled flow, particularly with low metering quantities in pumps that do not have built-in valve springs due to hygiene requirements, which can impair metering accuracy and dilution rate. To control the pump-specific hydraulic conditions, pressure (retaining) control valves are therefore used on the discharge side of the pumps after all installations with pressure losses to ensure a constant back pressure. This can also be used to compensate for and smooth out small residual pulsations in the multiplex pump heads. A specific subset of sanitary control valves also contains a dampener to manage downstream pressure fluctuations which aid in the production stability of Oligonucleotides. One such example is made by Equilibar, which are used in current package units.³
1 Text information from ABDATA database of pharmacies.
² Large scale purification of oligonucleotides with ion exchange chromatography (U. Krop, T. Pöhlmann, N. Schneider).
³ Technical Information Equilibar, 320 Rutledge Rd., Fletcher, North Carolina 28732, United States
Author: Dr. Hans-Joachim Johl, Lead Product Manager Pharma, Food & Life Sciences at LEWA
Source: LEWA GmbH