EagleBurgmann Magnetic Couplings Seal New Zero-leakage KSB Refinery Pump
KSB South Africa in cooperation with EagleBurgmann specified high-efficiency magnetic couplings to seal the shaft for the newly designed API 685 process pump. It was also decided to use the couplings from the proven MAK685 series because they reliably cover a broad application field in the higher pressure and performance range.
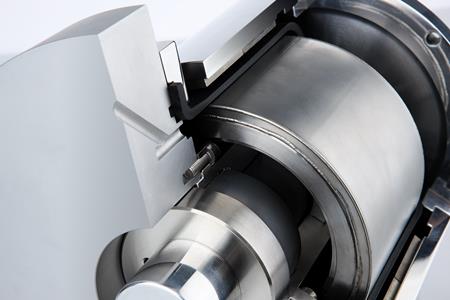
Reliable, powerful, and efficient: the EagleBurgmann magnetic coupling in the new KSB zero-leakage refinery pump, type PRHmdp (Image: Eagle Burgmann)
The requirements for pumping hydrocarbons in petrochemical plants and refineries are very high in terms of performance, efficiency, and emission limits. An increasing number of process pumps with magnetic couplings as per API685 are being used here. For several years EagleBurgmann and KSB have been cooperating to design a magnetic coupling pump. The new zero-leakage RPHmdp refinery pump stands for the experiences of the KSB design engineers, EagleBurgmann s coordinated magnetic coupling program, and the combination of an existing pump hydraulic with the matching magnetic couplings.
The universal MAK modular concept for pumps – for initial installation or retrofitting – is based on two proven magnet variants, depending on the requirement: samarium-cobalt for operating temperatures up to 300°C, and neodymium ferrum boron up to max. 120°C. As a result, the coupling size can be optimally adapted to the required operating conditions and capacities.
Different containment shell materials with the least electrical conductivity for minimum eddy current losses are offered as well. A carbon fiber reinforced PEEK containment shell is used for applications up to 120°C which eliminates completely eddy currents and seals with a maximum degree of efficiency. Due to the occurring loads, a metallic high-performance containment shell with a laminated structure, which reduces eddy current losses to a minimum, is used for more demanding applications up to 300°C with higher speeds and pressures.
The magnetic couplings are supplied with high-precision sliding bearings to securely bear the pump shaft. The bearing absorbs the axial and radial forces of the impeller; an effective product circulation in the interior of the magnetic coupling ensures lubrication and heat dissipation and guarantees high operational safety – even for low-viscosity media.
Bearings that can be cooled or heated are also optionally available. The gas from problematic gas-containing media is removed from the containment shell chamber by a hollow shaft which consequently prevents the risk of the sliding bearings from running dry.
An overview of the advantages
- Optimized circulation guidance to improve the bearing load capacity and cooling of the containment shell
- High-grade sliding bearing and magnetic materials enable a wide range of use.
- No eddy current losses due to carbon fiber reinforced PEEK containment shell and therefore no heating – increased safety, especially for high speeds.
- Resistance to a great number of aggressive media.
- Resistant to jolts caused by ductile material properties.
- High pressure limit with 42 bar, in conformance with the API 685 standard
Operating range
Torque:1.879 Nm (magnet material: NdFeB, 1.348 Nm (magnet material: SmCo)
Pressure: 45 bar
Temperature: -40°C ... +300°C
Rotational speed: 3.600 rpm