Dürr Ecoclean’s PulseBoreCenter Uses Reduced Pressure for Superior Efficiency
High-pressure water jetting is becoming increasingly widespread as a method of activating the cylinder bore surfaces of engine blocks prior to thermal coating.
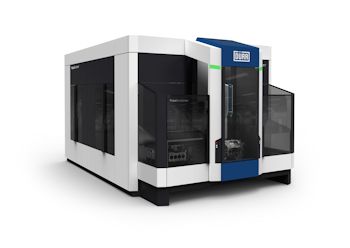
This technology is a very costly one, involving pressures of as much as 3000 bar. Now, however, Dürr Ecoclean’s PulseBoreCenter permits the use of no more than 600 bar in this ultra-high pressure application. The gain is due to the integrated innovative EcoCBooster, which generates a pulsating water jet of much higher kinetic energy. Users will thus benefit from substantial savings in investment and operating cost as well as from improved process results. This innovative technology offers advantages also in other operations such as cleaning, deburring and decoating.
With today’s quest for reduced CO2 emissions and fuel savings despite increasing power outputs, components for both spark ignition and diesel engines are becoming ever more complex and compact in design. As part of this downsizing trend, thermal coatings are increasingly replacing grey cast iron cylinder liners in engine blocks. To optimize the adhesive pull strength of the coating, the aluminium cylinder bore surface is activated by roughening before the extremely thin (150 to 300 µm) and very hard metal layer is applied. This activating operation is increasingly carried out by high-pressure water jetting, mainly because this technology causes no wear and the roughened surface will not require cleaning afterwards.
Activation with 600 instead of 2500 bar
High-pressure water jetting as employed in today’s activation processes uses pressures of at least 2500 bar. Apart from the substantial investment, this involves high operating costs, not least because of the very complex filtration required or, alternatively, due to the fresh water input in systems not having a closed water circuit. Dürr Ecoclean’s new EcoCBooster used in the PulseBoreCenter enables bore activation treatments to be carried out at no more than 600 bar. The secret behind this huge pressure decrease lies in the fact that this innovative process uses a pulsed water jet which boosts the kinetic energy by a factor of 5 to 10.
Outstanding adhesion, even on grey cast iron surfaces
The results achieved with an EcoCBooster are equal to or better than those obtained by conventional processes using ultra-high pressures. This is confirmed by the industrial applications implemented to date. Adhesive pull strength levels have been found to exceed 60 MPa throughout, regardless of whether the metal coating is applied by atmospheric plasma spraying (APS) or arc wire spraying (AWS). The method allows even cast surfaces to be roughened to a degree that allows the molten metal particles to be firmly interlocked with surface. The EcoCBooster thus opens up new fields of application, such as the treatment of grey cast iron liners for truck engines, which had not been feasible before even with ultra-high pressure water jetting at 3000 bar.
High savings in investment and operating costs
The new process also scores high in the cost efficiency department. Thus, the purchase cost of a pump delivering 600 bar is substantially lower than that of a 3000 bar unit. At the same time, its filtration system can be of less complex design. To minimize wear on an ultra-high pressure pump, it is necessary to remove solid particles down to 1 µm from the fluid by filtration. This means that even fresh water needs to be filtered. The EcoCBooster’s 600 bar pump is clearly less sensitive. With this high-pressure pump, it is enough to remove particles down to 3 – 5 µm and the water is run in a closed circuit. This has a significant effect on investment and operating costs. Moreover, costs will be recovered more quickly due to the pump’s low power consumption. It needs up to 50 percent less energy than a pump in the ultra-high pressure water jetting process. In addition, maintenance costs for a 600 bar pump amount to only about one-third to one-fourth of what must be expected for a 3000 bar unit. At the user’s choice, the process can be carried out either with pure water or with a corrosion-inhibiting fluid.
High-flexibility modular equipment design
For its EcoCBooster, Dürr Ecoclean has developed an all-new equipment concept referred to as the PulseBoreCenter. It consists of the application system with NC controller and booster units in addition to a supply module comprising the high-pressure pump plus the entire water supply and filtration equipment. The system can process any engine block, from inline 2-cylinder to all V-engine units, including sophisticated W12 and W16 engine designs. Thanks to its modular design it can be easily adapted to diverse loading methods and cycle times.
Applications ranging from medical equipment to jet engine construction
Uses of the new EcoCBooster are by no means limited to roughening cylinder bores. The system’s process technology and economic advantages will benefit any application which involves water jetting in the high-pressure range, i.e., at over 1000 bar. Applications extend from medical equipment and jet engine manufacturing, through paint stripping, decoating, deburring and part cleaning to the restoration of concrete surfaces.
Picture: The innovative EcoCBooster forming part of the PulseBoreCenter provides a pressure reduction from 3000 to 600 bar in activating the cylinder bore surfaces of engine blocks. Apart from major savings, the technology provides a superior treatment result.(© 2014 Dürr Ecoclean GmbH)
Source: Dürr Technik GmbH & Co. KG