Druckzentrum Hagen spart mehr als 30 Prozent Energie mit drehzahlgeregelten Schraubenkompressoren von Atlas Copco
Effizienz steigern, Versorgung sichern: So lautete die Vorgabe, als im Druckzentrum Hagen vor zwei Jahren die Sanierung der Druckluftversorgung anstand. Die alten Maschinen aus den frühen 1990er Jahren konnten die hohen Anforderungen an Betriebssicherheit und Energieeffizienz nicht mehr optimal erfüllen. Heute stellen drei drehzahlgeregelte Schraubenkompressoren aus der GA-Serie von Atlas Copco die benötigte Druckluft zuverlässig bereit.
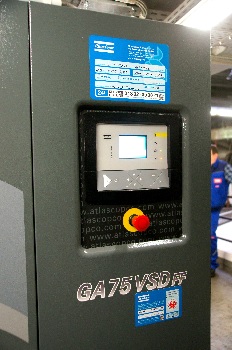
In die Kompressorgehäuse der FF-Varianten (für "Full Feature") sind Kältetrockner, Kondensatableiter und -trenner bereits ab Werk integriert. (Foto: Atlas Copco)
Die effizientere Fahrweise der neuen Station sowie ein um 1,5 bar geringerer Betriebsdruck senken den Energieverbrauch um mehr als 30 Prozent. Amortisationszeit: drei Jahre.
14 Millionen Druckstücke laufen jede Woche durch die Rotationsdruckmaschinen und Versandlinien im Druckzentrum Hagen, einer Druckerei der Essener Funke Mediengruppe. Insgesamt 160 Mitarbeiter sind von Sonntag bis Freitag rund um die Uhr im Einsatz, bringen Politisches, Kulturelles, Lokales aufs Papier und drucken jede Menge Anzeigenblätter. Tageszeitungen machen einen Großteil der Palette aus, die Gruppe gibt etwa das Hamburger Abendblatt und die Berliner Zeitung heraus. Die Druckzentren in Essen, Hagen, Braunschweig und Erfurt produzieren nicht nur die verlagseigenen Titel, sondern auch Fremdaufträge.
„Wir drucken hier die Ausgaben der Westfälischen Rundschau, der Westfalenpost Hagen und Teilausgaben der WAZ“, erklärt Klaus-Dieter Strauß, Gruppenleiter E-Werkstatt Hagen und zusammen mit Werkstattleiter Jens Kaffka zuständig für die Druckluftversorgung. „Mit unseren Bestück- und Versandanlagen können wir bis zu 20 Beilagen in eine Zeitung beziehungsweise in ein Anzeigenblatt einfügen.“
Druckluftverbrauch unterliegt starken Schwankungen
Druckluft wird an den Rotationsdruckmaschinen und Falzapparaten benötigt, außerdem für die Plattenherstellung und an den Versandlinien. „Unser Druckluftverbrauch ist von großen Schwankungen gekennzeichnet“, erläutert Strauß. „Den größten Bedarf haben wir jede Nacht beim Andruck um 22 Uhr. Da fahren alle Maschinen gleichzeitig hoch und benötigen dann zum Teil 420 Liter pro Sekunde. Im Schnitt liegt der Verbrauch bei 240 Litern pro Sekunde, die Grundlast am Wochenende bei 60 Litern pro Sekunde.“ Das Thema Versorgungssicherheit steht durch das genau bemessene Zeitfenster für den nächtlichen Druck der Tageszeitungen an erster Stelle. Fast ebenso wichtig ist die energieeffiziente Bereitstellung der benötigten Druckluft.
Drei neue Kompressoren sparen im ersten Jahr 200000 kWh ein
„Wir haben ein Energiemanagementsystem (EMS) nach ISO 50001 etabliert“, berichtet Jens Kaffka. „Einmal pro Monat diskutieren wir im Team mit den Abteilungsleitern und unserem EMS-Beauftragten die Verbrauchswerte und Reduktionsmöglichkeiten. Unsere neuen Kompressoren konnten jetzt kräftig zu den angestrebten Einsparungen beitragen. Der Stromverbrauch für die Drucklufterzeugung sank im ersten Betriebsjahr der neuen Anlage um knapp 200000 Kilowattstunden beziehungsweise um 31 Prozent.“
Seit Februar 2017 arbeiten im Druckzentrum Hagen drei luftgekühlte drehzahlgeregelte Kompressoren des Typs GA 75 VSD FF von Atlas Copco. VSD (Variable Speed Drive) steht für die integrierte Drehzahlregelung, FF für „Full Feature“. Das heißt, ab Werk sind bereits Kältetrockner, Kondensatableiter und -trenner in die Maschine integriert. Zu den Vorteilen dreier gleicher Maschinen zählt, dass sie die gleichen Ersatzteile benötigen und dass man in Hagen auf die stark schwankenden Druckluftverbräuche mit mehreren drehzahlgeregelten Maschinen am besten reagieren kann, weil sich so der größte Regelbereich ergibt. Drei Speicher mit einem Volumen von jeweils 3000 Litern und ein Öl-Wasser-Abscheider komplettieren die Druckluftversorgung.
Ölfreiheit entscheidend bei Plattenherstellung
„Wir arbeiten mit einem Taupunkt von plus zwei Grad Celsius“, beschreibt Jens Kaffka die Anforderungen an die Druckluftqualität. „Außerdem muss die Druckluft ölfrei sein, da Ölnebel bei der Plattenherstellung die empfindlichen Laser beschädigen würde.“ Da es sich bei den GA-Maschinen um öleingespritzte Kompressoren handelt, muss eventuell vorhandenes Restöl sicher aus der Druckluft entfernt werden. Dies gelingt mit UD+-Filtern, die in die Kompressoren integriert sind. Sie eliminieren alle Partikel, die größer als 0,01 µm sind, und reduzieren den Restölgehalt auf 0,001 mg/m³. Redundanz garantieren dezentral installierte Ölfilter vor den Maschinen in der Plattenherstellung.
Das optimale Zusammenspiel der Kompressoren wird von einem Energiesparsystem ES 16 von Atlas Copco gesteuert. Prioritäten liegen auf der gleichmäßigen Auslastung der Maschinen und einem möglichst energieeffizienten Betrieb. „Den Bedarf decken wir mit ein bis zwei Kompressoren. Der dritte dient jeweils als Redundanz“, erläutert Strauß. „Alle 30 bis 40 Stunden wechseln sich die Maschinen ab.“ Auf diese Weise kommen alle auf die gleiche Betriebsstundenzahl und können bei einem Serviceintervall gleichzeitig gewartet werden. Die übergeordnete Steuerung gibt den Maschinen zudem automatisch immer eine Drehzahl im effizienten Regelbereich zwischen 20 und 85 Prozent ihrer maximalen Leistung vor.
Druckreduzierung von 8,5 auf 7 bar spart über 10 Prozent Energie
Auch ein deutlich reduzierter Betriebsdruck trägt zu den erzielten Energieeinsparungen bei. „Wir haben den Netzdruck schrittweise von 8,5 bar auf derzeit 7 bar reduziert“, sagt Strauß. „Geplant ist eine weitere Absenkung auf 6,8 bar, das würde für die Druckmaschinen noch ausreichen. Das Profil haben wir in der Steuerung bereits angelegt. Wir brauchen nur noch umzuschalten.“ Rechnet man mit der Faustformel, die von 6 bis 7 Prozent geringeren Energiekosten pro Bar ausgeht, konnte das Druckzentrum Hagen seinen Stromverbrauch allein durch diese Maßnahme um mehr als 10 Prozent reduzieren. Weiter als auf 6,8 bar will man den Druck jedoch nicht absenken, um die Produktionssicherheit nicht zu gefährden. „Unsere Druckmaschinen brauchen 6 bar, darunter arbeiten die Zylinder und die Ventile nicht mehr“, erklärt Strauß.
Möglich wurde die Senkung des Netzdrucks durch den Umstieg auf drehzahlgeregelte Kompressoren, mit denen eine Regellücke der alten Station geschlossen wurde. Denn die früheren Maschinen mussten streckenweise im Last-Leerlauf-Betrieb laufen. Die Folge war ein breiteres Druckband, verbunden mit einem höheren Betriebsdruck. Beides wurde nun optimiert, so dass sich in Summe die genannten Einsparungen von mehr als 30 Prozent ergeben.
Verbesserte Betriebssicherheit bei höherer Effizienz
Vor der Erneuerung der Druckluftstation liefen in Hagen zwei Schraubenkompressoren vom Typ GA 375, ein GA 75 und ein drehzahlgeregelter GA 50 VSD von Atlas Copco. Betrieben wurden die Kompressoren über eine Vorrangschaltung, eine übergeordnete Steuerung gab es nicht. Zum Zeitpunkt des Umbaus waren die Maschinen bereits zwischen 20 und 30 Jahre alt. „Wir wollten Energie einsparen und die Betriebssicherheit gewährleisten“, erläutert Jens Kaffka die Beweggründe für den Austausch. „Aufgrund der guten Wartung sind die alten Maschinen zwar bis zuletzt einwandfrei gelaufen, aber die Ersatzteile waren bereits seit längerem abgekündigt.“
Im Frühjahr 2016 begann Jens Kaffkas Team gemeinsam mit Atlas Copco damit, ein Konzept zu erstellen. „Wir haben zunächst über eine Woche die Verbräuche an den einzelnen Kompressoren gemessen“, beschreibt Bernd Wälter, technischer Berater bei Atlas Copco, die Vorgehensweise. „Die Messergebnisse gaben Aufschluss über den durchschnittlichen Druckluftbedarf und die vorliegenden Schwankungen und lieferten uns die Grundlage für die Auslegung der aktuellen Station. Bereits zu diesem Zeitpunkt stand fest, dass der Energiebedarf deutlich sinken würde.“
20 Prozent BAFA-Förderung verkürzt Amortisationszeit auf drei Jahre
Ende 2016 wurden die drei Kompressoren und die ES-16-Steuerung geliefert. Eine angedachte Wärmerückgewinnung erwies sich aufgrund der großen Entfernung zwischen Kompressorstation und potenziellen Abnehmern als technisch sehr aufwendig und wurde deshalb verworfen.
Eine Förderung aufgrund ihrer hohen Effizienz erhielt die neue Druckluftstation auch ohne diese zusätzliche Maßnahme. „Das Förderprogramm des Bundesamtes für Wirtschaft und Ausfuhrkontrolle (BAFA), über das der Antrag lief, nennt sich ‚Effiziente Querschnitts-Technologien im Mittelstand‘“, erklärt Bernd Wälter. „Im Förderkatalog des BAFA sind unsere GA-VSD-Maschinen als förderfähige Einzelmaßnahme gelistet und werden bei einer Betriebsgröße wie hier in Hagen mit 20 Prozent des Kaufpreises bezuschusst. Durch die Förderung und die jährlichen Energieeinsparungen wird sich die neue Druckluftanlage bereits in rund drei Jahren amortisiert haben.“
Zusammen mit den neuen Kompressoren entschied man sich in Hagen für den Atlas-Copco-Service „Xtended Warranty+“. Dieser verlängert die Standardgarantie auf fünf Jahre und deckt alle Reparaturkosten ab, die nicht auf Fahrlässigkeit des Kunden oder ungeeignete Standortbedingungen zurückzuführen sind. Darüber hinaus umfasst der Service auch die proaktive Wartung der Maschinen durch erfahrene Service-Techniker von Atlas Copco.
Smartlink Energy dokumentiert kontinuierlich die Effizienzparameter
Der optimale Zeitpunkt für die Wartung wird über das Atlas-Copco-Fernüberwachungssystem Smartlink ermittelt. In Hagen setzt man die erweiterte Variante Smartlink Energy ein. Diese liefert eine monatliche Übersicht über die Betriebsstunden der Kompressoren und die verbleibende Zeit bis zum nächsten Servicetermin. Darüber hinaus überwacht das System die komplette Druckluftstation und schickt im Notfall eine Warnmeldung per E-Mail oder SMS an den Betreiber. Last but not least erhält der Anwender alle notwendigen Werkzeuge, um die Anforderungen eines Energiemanagementsystems gemäß ISO 50001 zu erfüllen. Alle Effizienzparameter können einfach und kontinuierlich verfolgt und dokumentiert werden.
Mit der neuen Anlage und dem Service durch Atlas Copco ist man in Hagen mehr als zufrieden. „Hinsichtlich der Effizienz haben wir mehr erreicht als gedacht“, lobt Klaus-Dieter Strauß. „Alle Versprechen wurden eingehalten und unsere Vorgaben optimal umgesetzt. Alles läuft einwandfrei.“
Autorin: Stephanie Banse, Journalistin in Hamburg
Quelle: Atlas Copco Holding GmbH