Custom-Engineered Seal Yields Cost Savings in Severe Applications
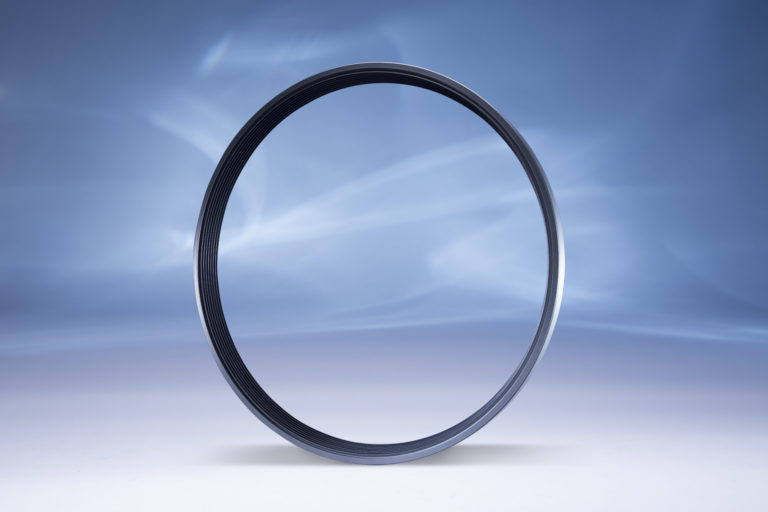
Arlon 4020 Labyrinth Seal (Image source: Greene, Tweed & Co. – Corporate)
Customer test results show up to a 1.5% gain in efficiency compared to traditional seals, correlating with field tests and predictions from FEA analysis.
Non-contacting labyrinth seals reduce leakage in centrifugal applications. This is accomplished by restricting flow through a series of chambers formed between the rotating element while the teeth control the passage of the media.
Greene Tweed’s labyrinth seals deliver superior performance due to the innovative combination of custom-engineered tooth designs and high-performance PEEK thermoplastic materials. The materials reduce friction and eliminate galling which extends the seal’s life and lowers maintenance costs. This optimized thermal expansion allows for retrofit and like-for-like replacement of conventional metallic designs.
The erosion and corrosion resistance make the Arlon 4020 ideal for severe sealing applications including those with high acid, Mercury content, or high-velocity media. Other ideal applications include oil and gas production and transportation, air separation units, chemical industry, fertilizer plants, carbon capture and storage, and industrial applications.
The Arlon 4020 has dramatically increased efficiency and reliability for longer run times due to the tooth profile. The seal uses a cyclic flex-and-return motion that withstands contact during critical speeds and tighter clearances. The tight running clearances increase efficiency and reduce flow rates to enhance the seal performance. This in turn decreases the compressor footprint and leads to cost savings and environmental benefits.
Source: Greene, Tweed & Co. – Corporate