Compact Diaphragm Pump for Applications with Limited Space Requirements
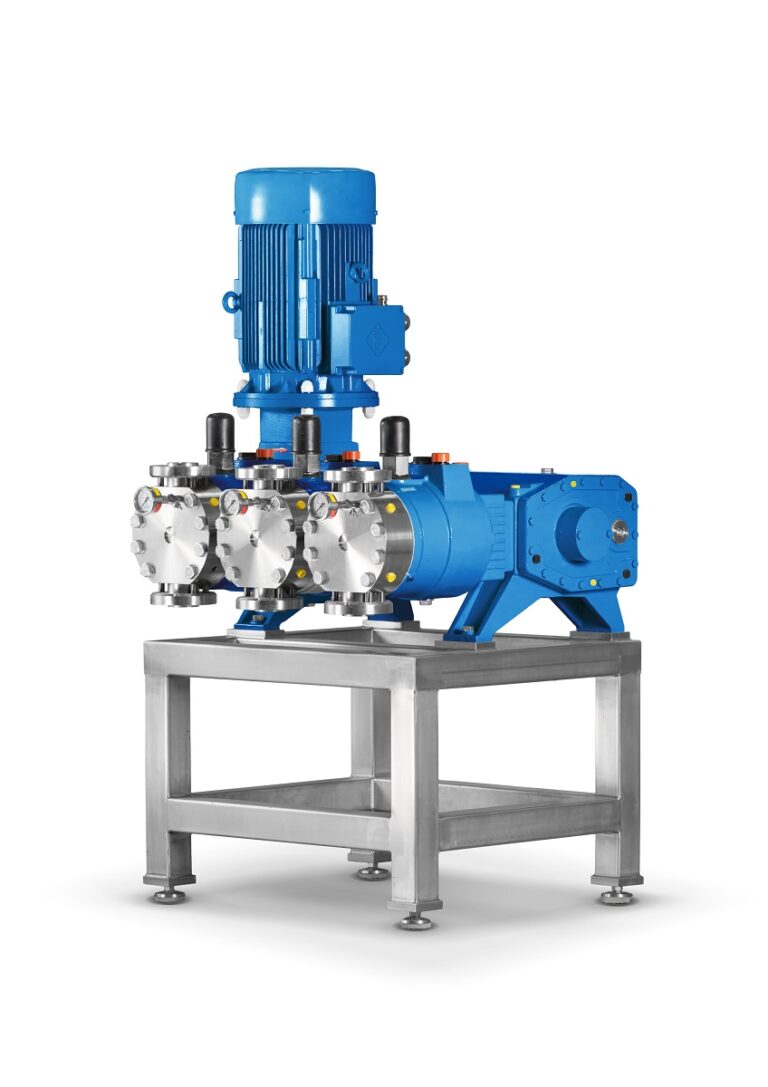
With a hydraulic output of 10 kW, the LEWA triplex G3E offers a low-pulsation alternative to single-head pumps in the medium output range. (Image source: LEWA GmbH)
However, their high residual pulsation can be the deciding factor for switching to a three-headed pump, which only has approx. 20 percent residual pulsation due to the superimposition of the flow rates. LEWA has therefore added a new size to its portfolio of triplex process diaphragm pumps in 2024. The LEWA triplex G3E is the smallest of its kind to date. With a hydraulic output of 10 kW, it offers a low-pulsation alternative to single-head pumps in the medium output range. Compared to a three-headed pump with a modular design, the G3E also requires a footprint that is around 30 percent smaller.
"Triplex pumps are the first choice for applications that rely on a particularly low-pulsation flow rate," says Thomas Bökenbrink, Lead Product Manager Pumps at LEWA. "Due to their design, these pumps have a residual pulsation of only approx. 20 percent, since the flow rates of the individual plungers overlap." In principle, 3-headed pumps can be built in a modular or monoblock design. The combination of several individual units in a modular design requires more space as well as additional couplings and gaskets, which comes at the expense of simplicity and robustness. So far, the lower costs of the modular solution have compensated for the disadvantages of this design. For this reason, LEWA generally met requests for particularly low-pulsation pumps with a three-pump combination of modular LEWA ecoflow drive units. With the new LEWA triplex G3E, however, the pump manufacturer from Leonberg, Germany, is now ushering in a new era for process technology applications with medium hydraulic outputs.
Monoblock design is efficient and "bullet proof"
As with all models in the LEWA triplex series, the three plungers of what is now the smallest triple process diaphragm pump are located in a common crankcase. The monoblock design not only makes the unit more compact than comparable modular solutions; it also has fewer individual components like gaskets and couplings, which makes the machine extremely robust. Thanks to this design, the LEWA triplex G3E can also be operated with stroke frequencies that are not possible with modular pumps. "Many of our customers appreciate that LEWA triplex pumps are virtually 'bullet proof' and can easily withstand even the most demanding application conditions," Bökenbrink notes. "However, the design also makes maintenance extremely easy for specialist personnel: for example, the gearbox is very easy to inspect even when it is installed."
Due to its robustness, the LEWA triplex G3E can run significantly faster than modular three-headed pumps. It has a permissible stroke frequency of up to 350 spm, which is very high for this size range. It thus achieves a maximum flow rate of around 20 m³/h at 16 bar. However, pressures of up to 400 bar are also possible at lower flow rates. With these technical specifications, the new development closes a crucial gap, also in terms of overall project costs, as Bökenbrink comments: "With the new triplex process diaphragm pump, a jump to the next larger machine can often be avoided. Above all, this reduces the investment costs for users."
High efficiency and long life espan
In several respects, the LEWA triplex G3E is more efficient than modular variants. As already mentioned, the monoblock design is more compact from the outset, since there is no need for additional connecting elements. And there is the vertical design of the motors, which reduces the footprint by a total of 30 percent. In addition, the new triplex process diaphragm pump achieves extraordinarily high efficiencies of between 80 and 90 percent over a very broad operating range. "In a fuel gas supply system on a ship, in this example a very large gas carrier (VLGC) with a cargo volume of approx. 90,000 m³, the energy costs would be reduced by around 20,000 to 30,000 euros per year compared to another pump technology with significantly lower efficiency," says Bökenbrink in conclusion. "In combination with the low wear of the few wear parts, this economic advantage is multiplied by the life expectancy of 20 to 40 years."
Source: LEWA GmbH